In the realm of modern manufacturing, the Blanking Die holds a pivotal position as a precision tool used for cutting or shearing materials into desired shapes and sizes. Also known as a cutting die or a shearing die, it is a specialized type of die that finds extensive application in the metalworking industry. This article delves into the essence of the Blanking Die, its working principles, and its significance in today’s manufacturing landscape.
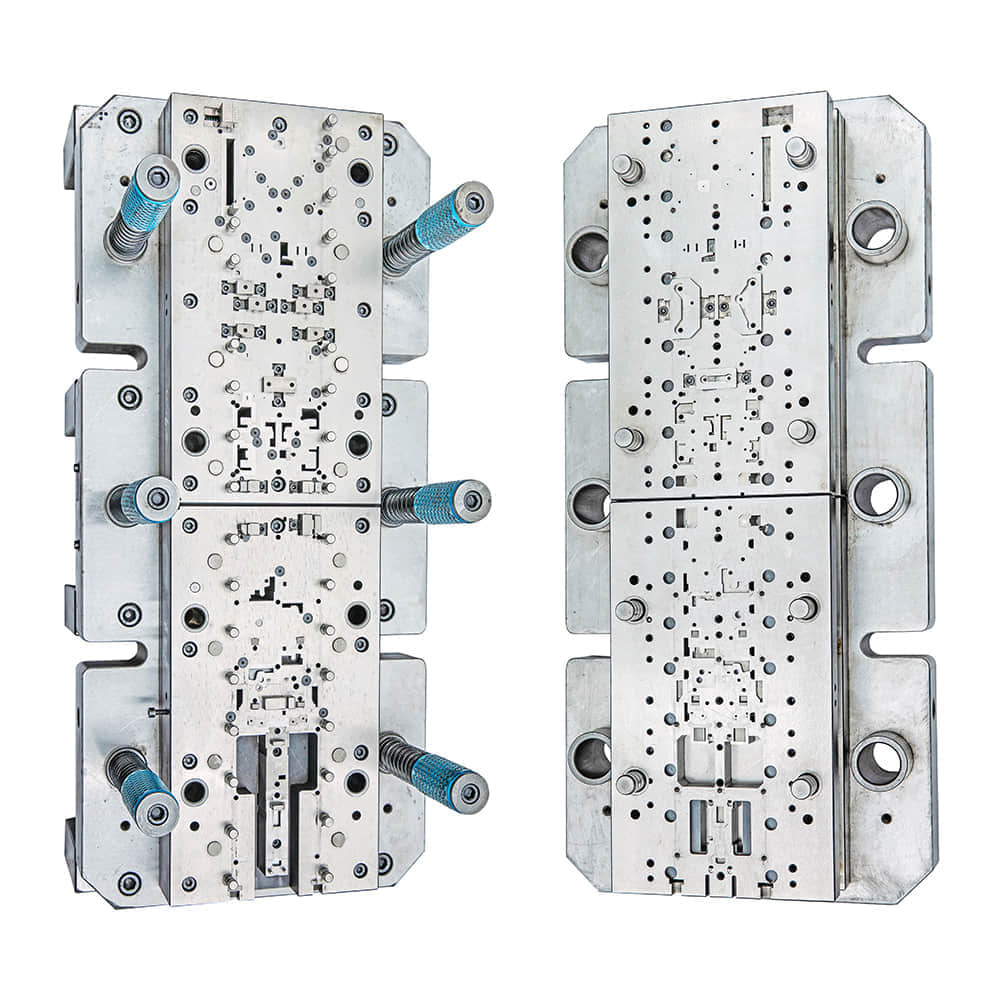
The fundamental function of a Blanking Die is to separate a workpiece from a larger sheet of material, often metal, in a single, swift stroke. This process, known as blanking, is crucial in the production of various components and parts for various industries, including automotive, electronics, and construction. The precision and efficiency of the blanking process largely depend on the design and quality of the die.
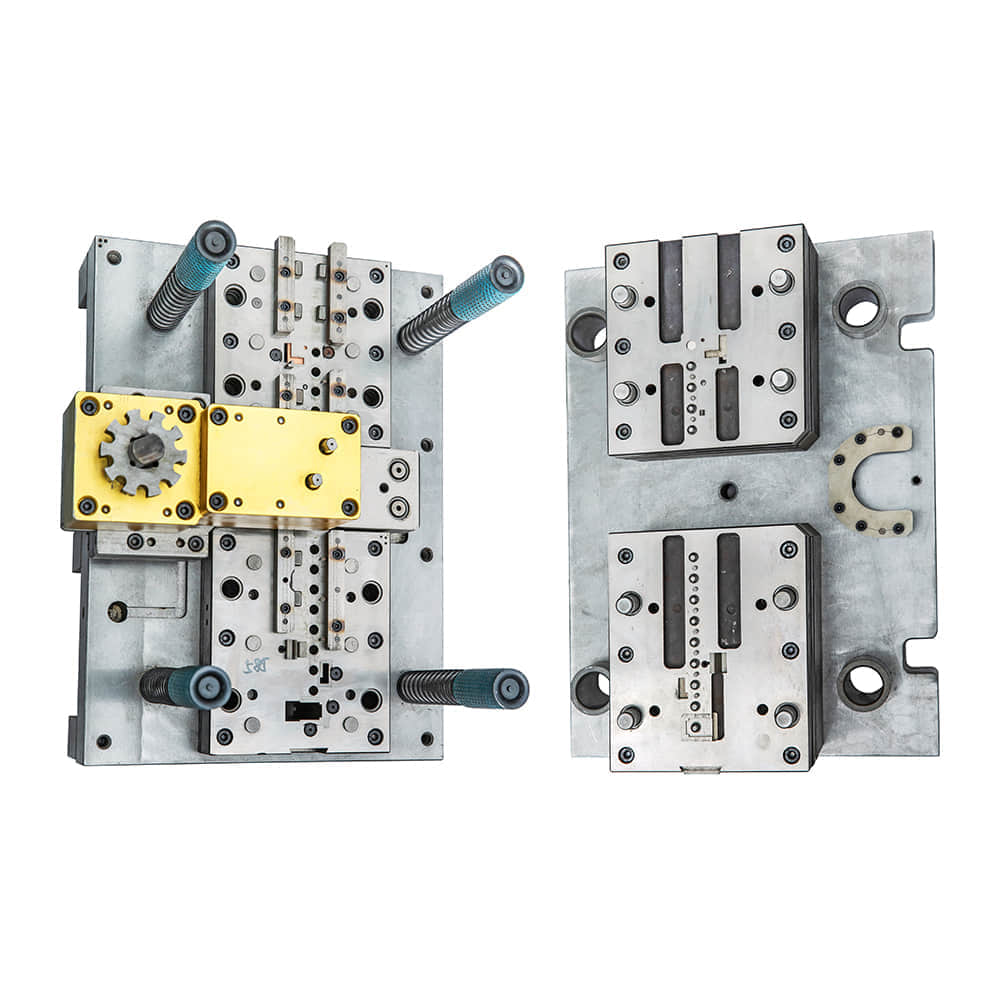
The Blanking Die typically consists of two main components: the upper die and the lower die. The upper die, often fitted with sharp cutting edges, is pressed down onto the workpiece, which is placed on the lower die. The force exerted by the upper die causes the material to shear cleanly, resulting in the desired shape. The precision of the cutting edges and the alignment of the two dies are crucial factors that determine the quality of the blanked part. The choice of materials for the Blanking Die is also crucial. High-strength and wear-resistant materials like tool steel or carbide are commonly used to ensure durability and longevity. These materials can withstand the repeated impacts and shearing forces encountered during the blanking process.
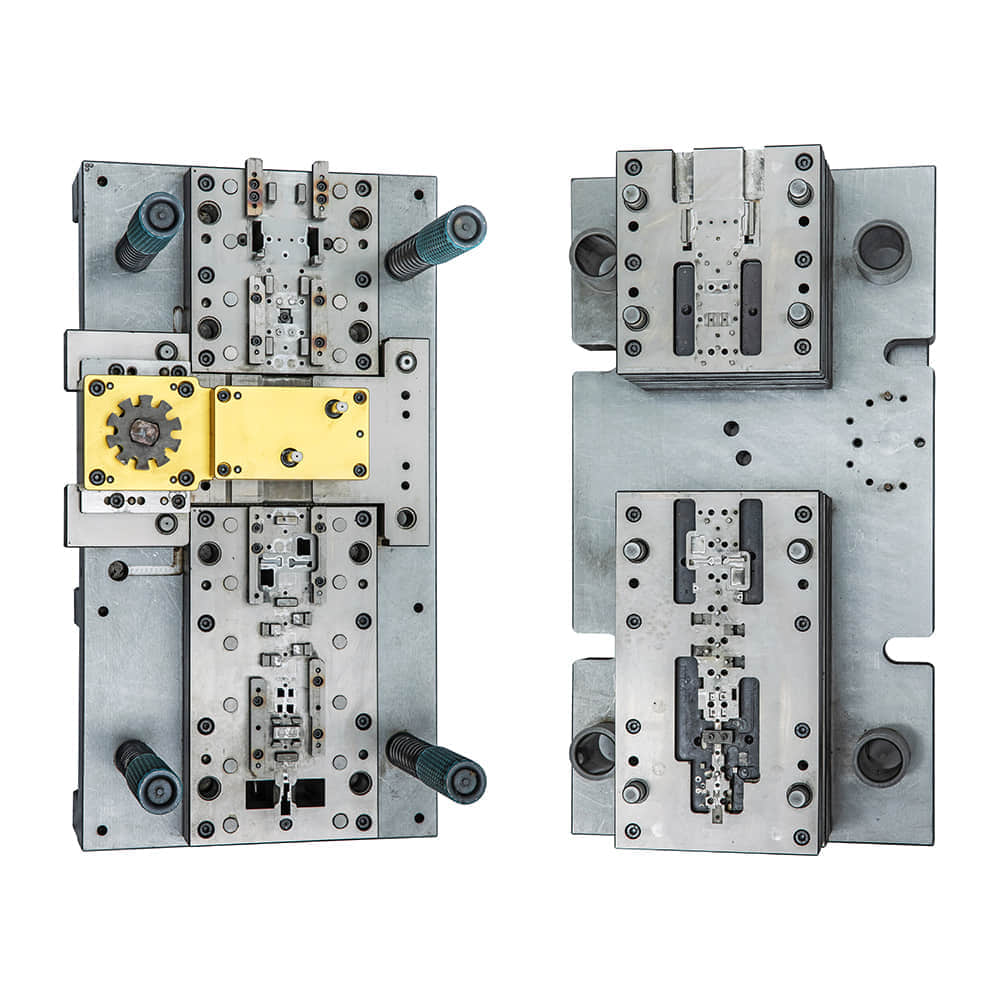