The concept of Progressive Die, also known as progressive tooling or simply progressives, has revolutionized manufacturing processes across various industries. It is a unique method of mass producing identical or similar products using a series of dies in a continuous sequence. Progressive Die design allows for the efficient and cost-effective production of a wide range of components, from simple to complex, in various materials such as metal and plastic.
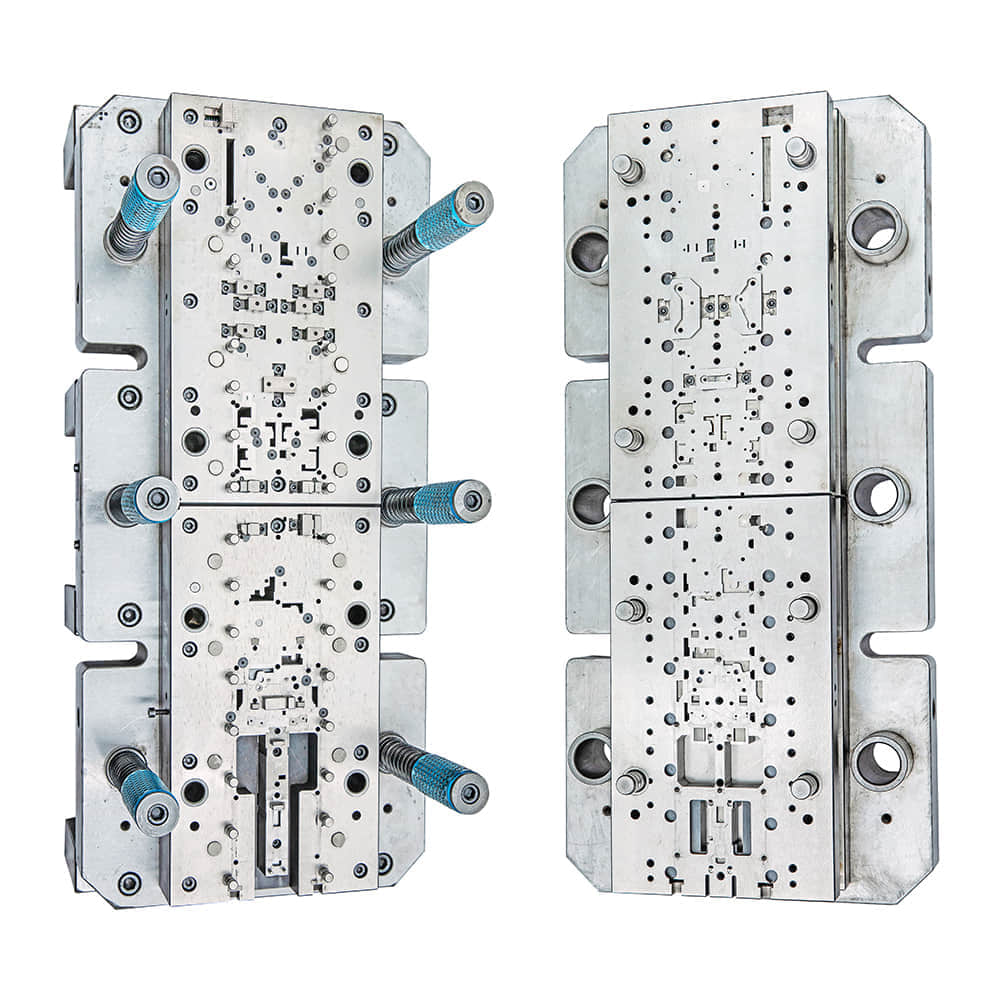
The fundamental principle behind Progressive Die is the integration of multiple manufacturing steps into a single continuous process. It eliminates the need for individual tooling for each step, reducing setup time and improving overall production efficiency. The dies are designed to perform specific operations on the material, gradually transforming it into the desired final product.
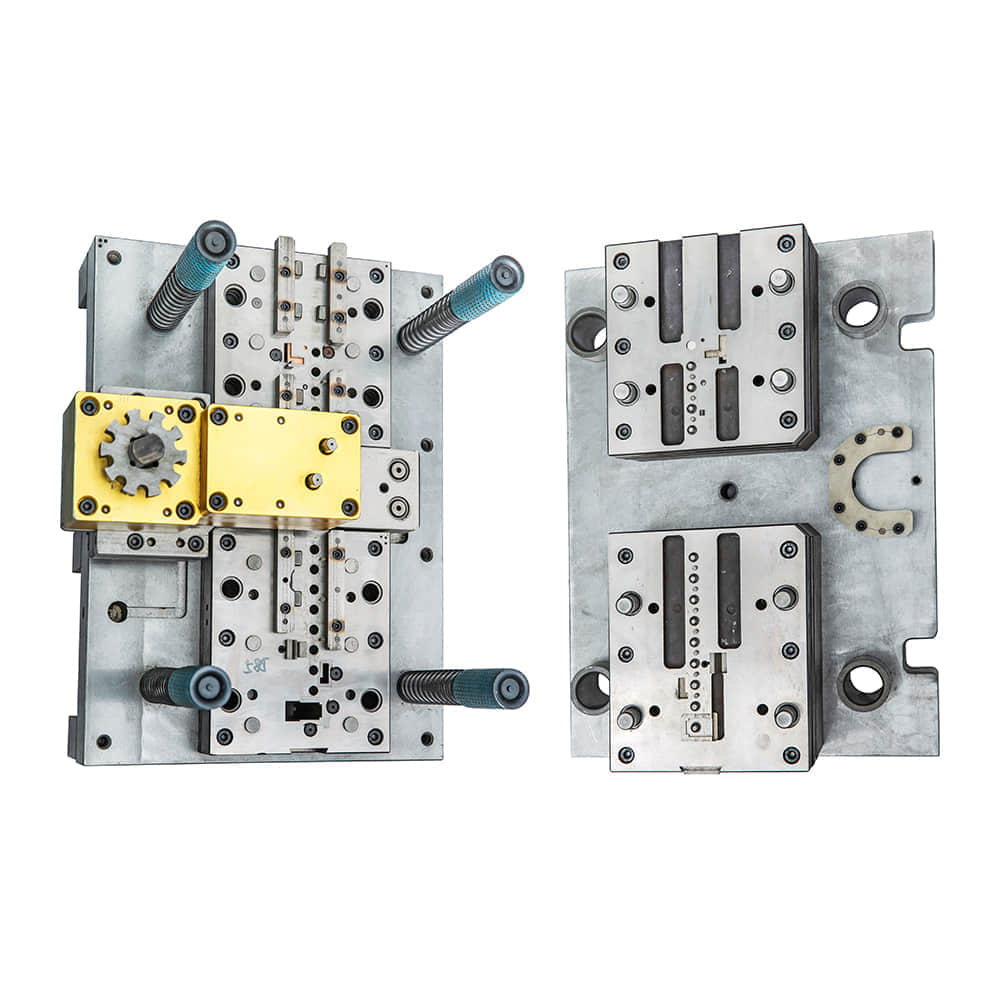
The progression of dies starts with the raw material, which is fed into the first die. Here, the initial shaping or cutting operations are performed, followed by a series of subsequent dies that further process the material. Each die complements the previous one, refining the shape and features until the final product emerges. The entire process is automated, ensuring consistent quality and repeatability. The advantages of Progressive Die are numerous. Firstly, it offers significant cost savings by reducing the need for individual tools and dies. This, in turn, lowers the overall cost of production and enables economies of scale. Secondly, the continuous nature of the process results in faster production rates, enabling manufacturers to meet demand for high-volume production runs efficiently.
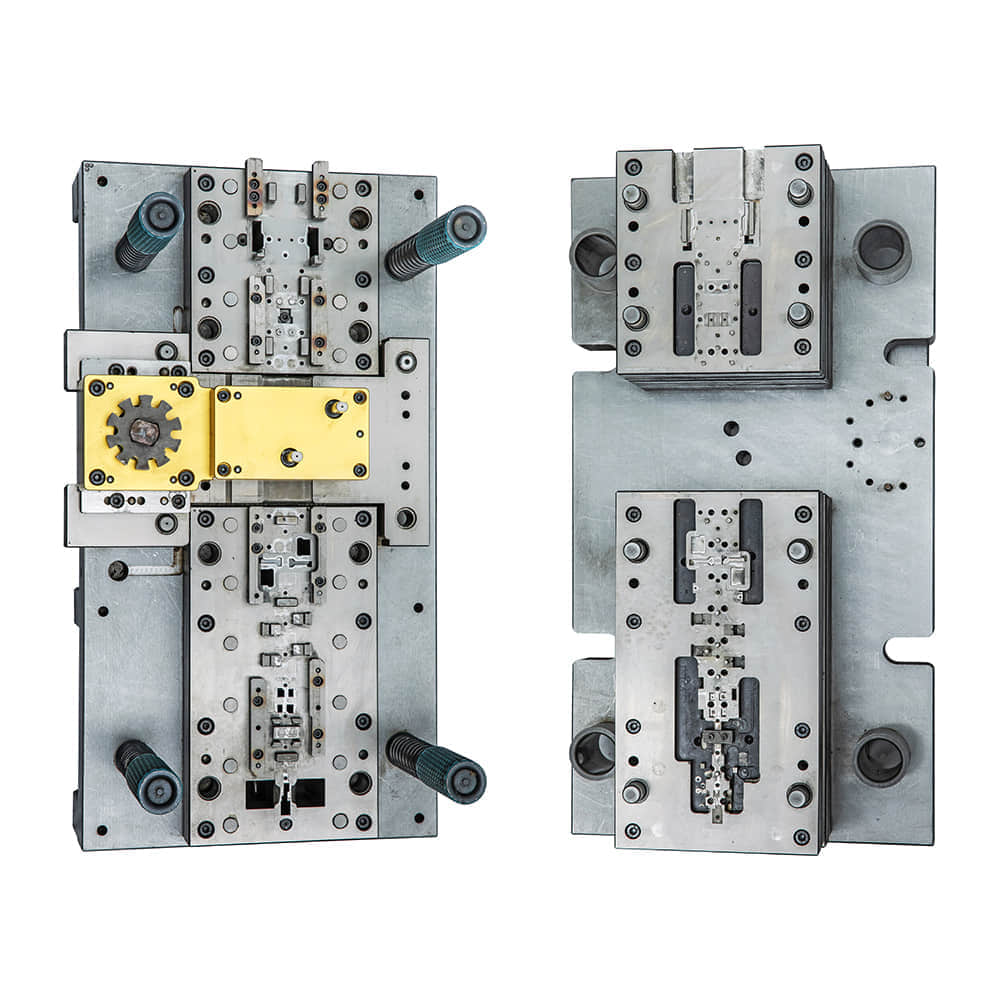