In the intricate world of modern manufacturing, thermoplastic injection molds occupy a pivotal position. These precision-engineered tools are not just mere containers for shaping plastic; they are the catalysts that transform molten thermoplastic into a diverse array of functional and aesthetic products.
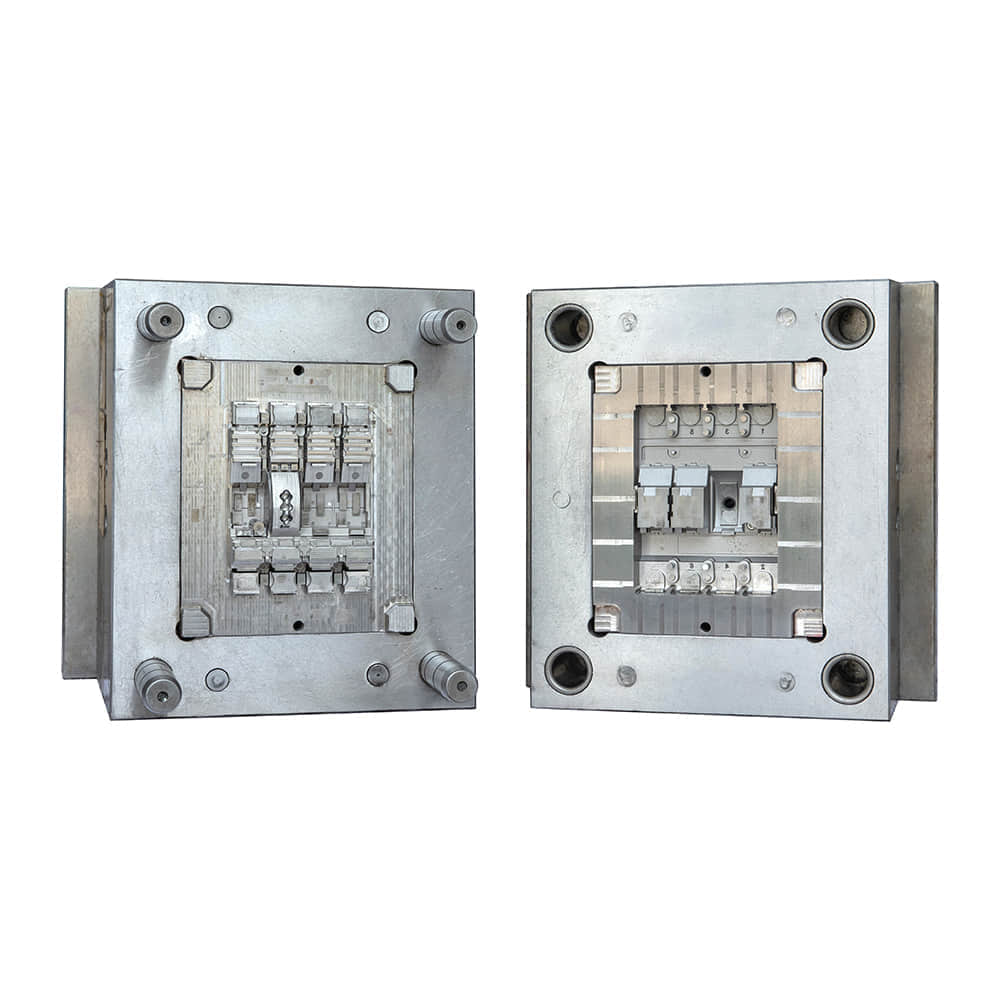
Thermoplastic injection molding is a highly specialized process that involves injecting molten thermoplastic into a mold cavity under high pressure. The mold, in essence, defines the shape, size, and features of the final product. Its design and construction are therefore paramount to achieving desired outcomes.
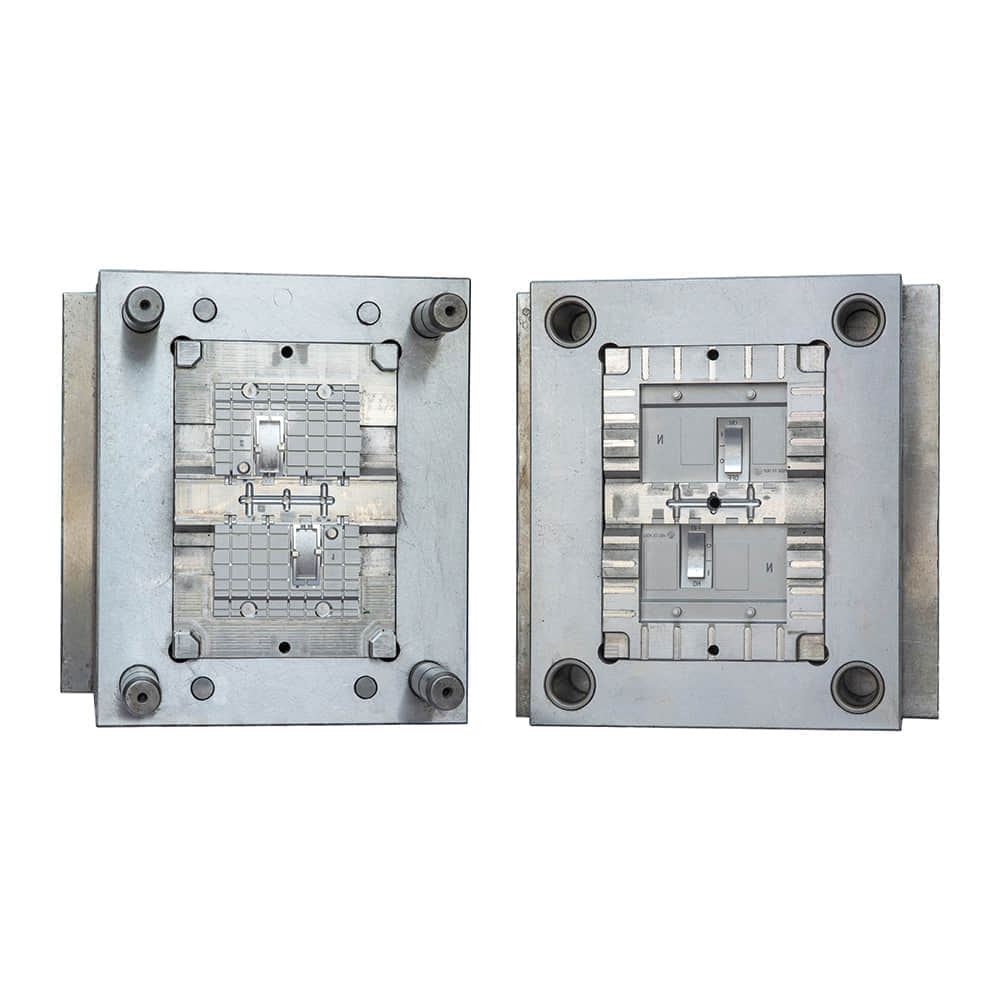
The process begins with the selection of the appropriate thermoplastic material, tailored to meet the specific requirements of the end product. The material is then heated to a molten state and injected into the mold cavity. The mold’s intricate geometry ensures that the molten plastic flows evenly, filling all corners and cavities, resulting in a uniformly shaped product. The cooling phase is critical in ensuring the plastic solidifies evenly, preserving the desired shape and preventing any distortions. The mold’s thermal conductivity and cooling channels play a vital role in this process, ensuring rapid and uniform cooling.
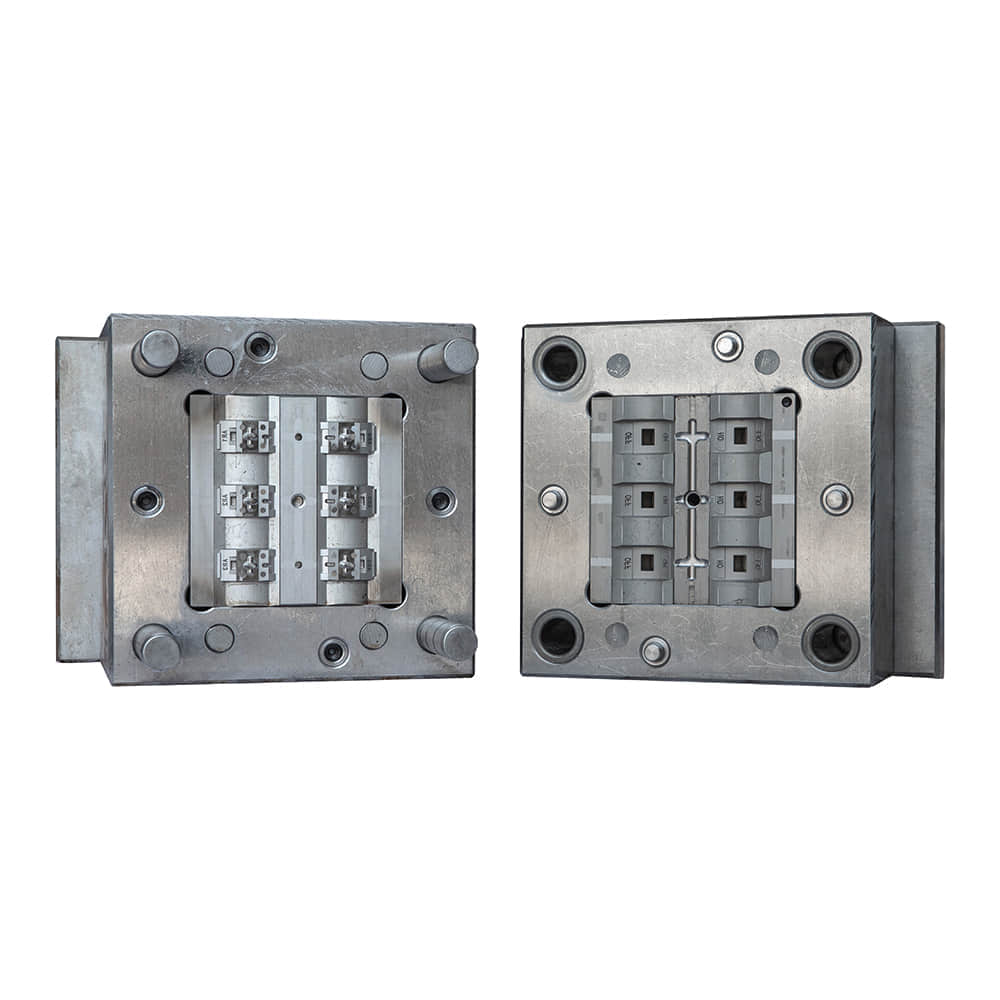