Progressive Die, a cornerstone of modern manufacturing, has revolutionized the way we approach precision stamping and part formation. Its unique design and functionality have made it an indispensable tool in various industries, including automotive, electronics, and home appliances. This article delves into the evolution, principles, advantages, and future prospects of Progressive Die.
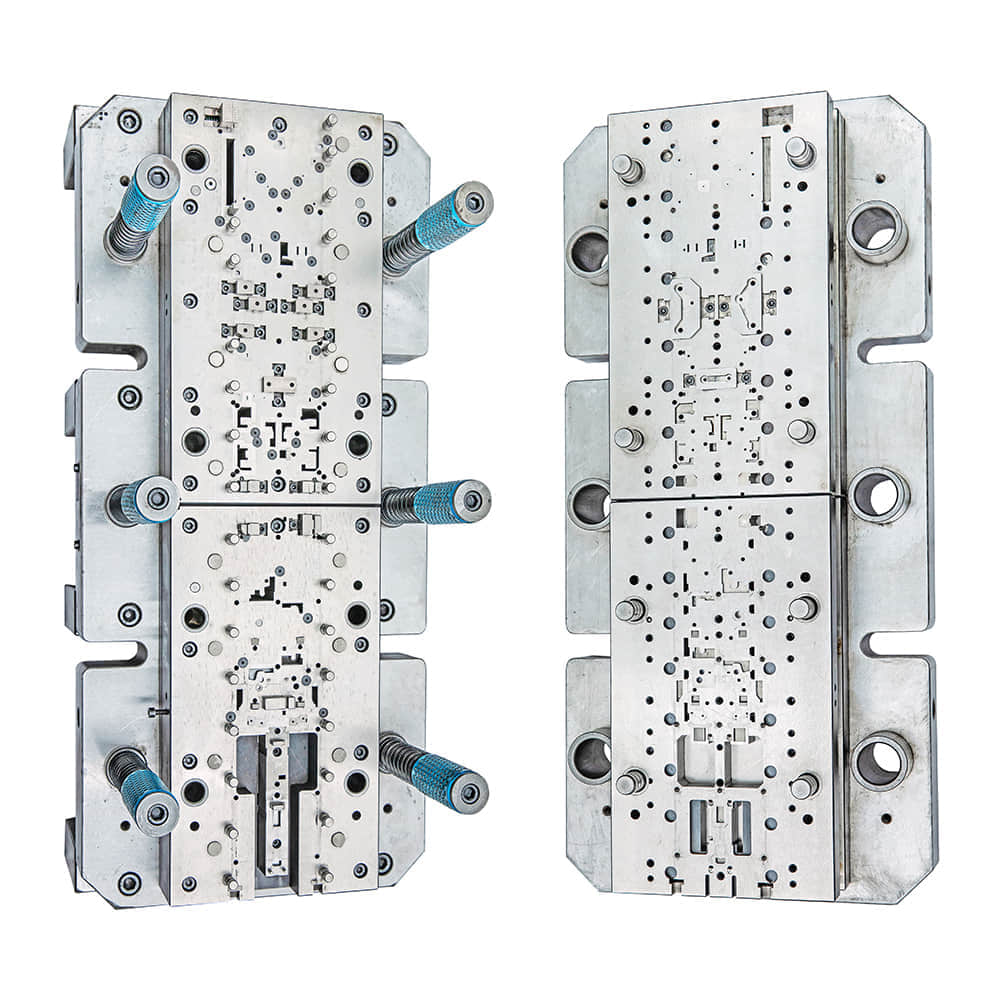
The concept of Progressive Die dates back to the early stages of metalworking, but it has evolved significantly over the years. Its core principle lies in the sequential and progressive nature of the stamping process. A Progressive Die is designed with multiple stations, each performing a specific stamping operation on the workpiece. As the material moves through these stations, it gradually transforms into the desired shape or component.
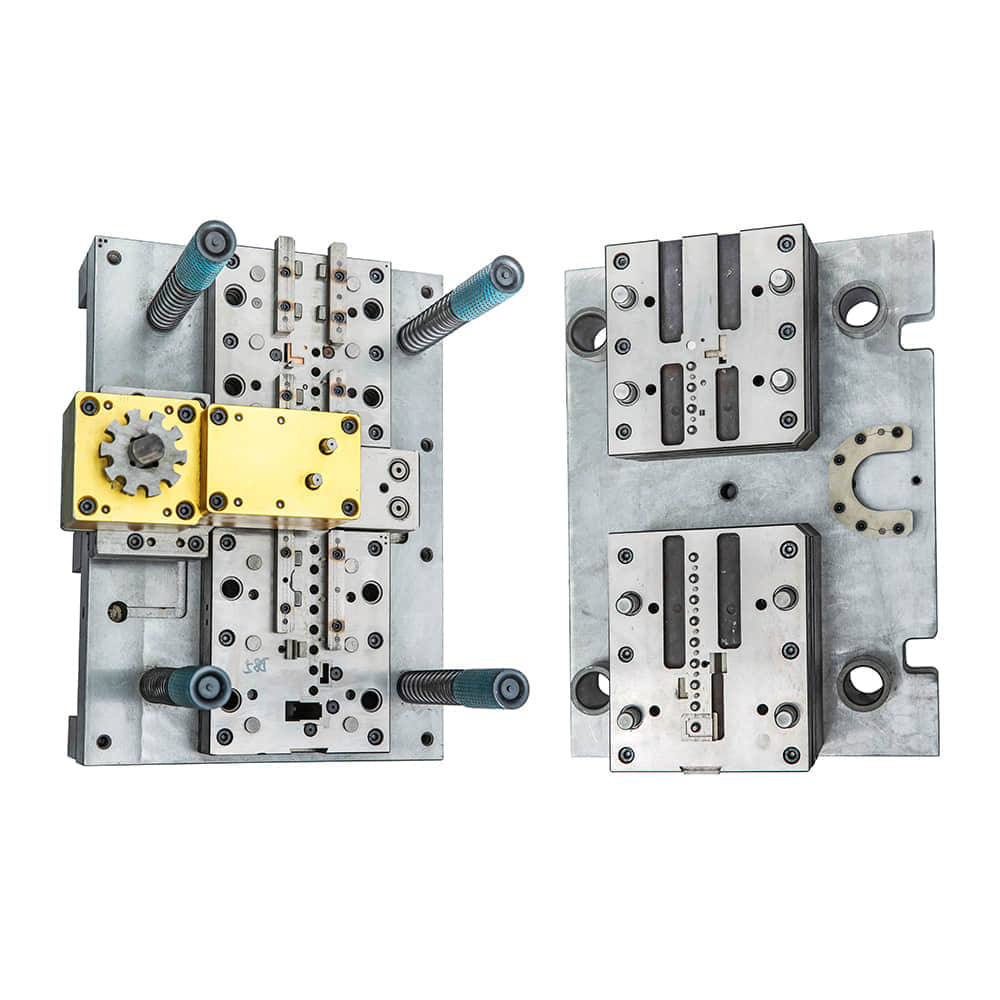
The key advantage of Progressive Die lies in its efficiency and precision. By combining multiple stamping steps into a single die, it significantly reduces the need for manual handling and setup changes, thereby increasing overall productivity. Furthermore, the continuous flow of material through the die ensures consistent quality and reduced material waste. Another notable aspect of Progressive Die is its versatility. Whether it’s creating intricate parts for high-end electronics or simple components for mass-produced goods, Progressive Die can be tailored to meet specific requirements. This flexibility, coupled with the ability to handle a wide range of materials, makes it a highly adaptable tool in various manufacturing scenarios.
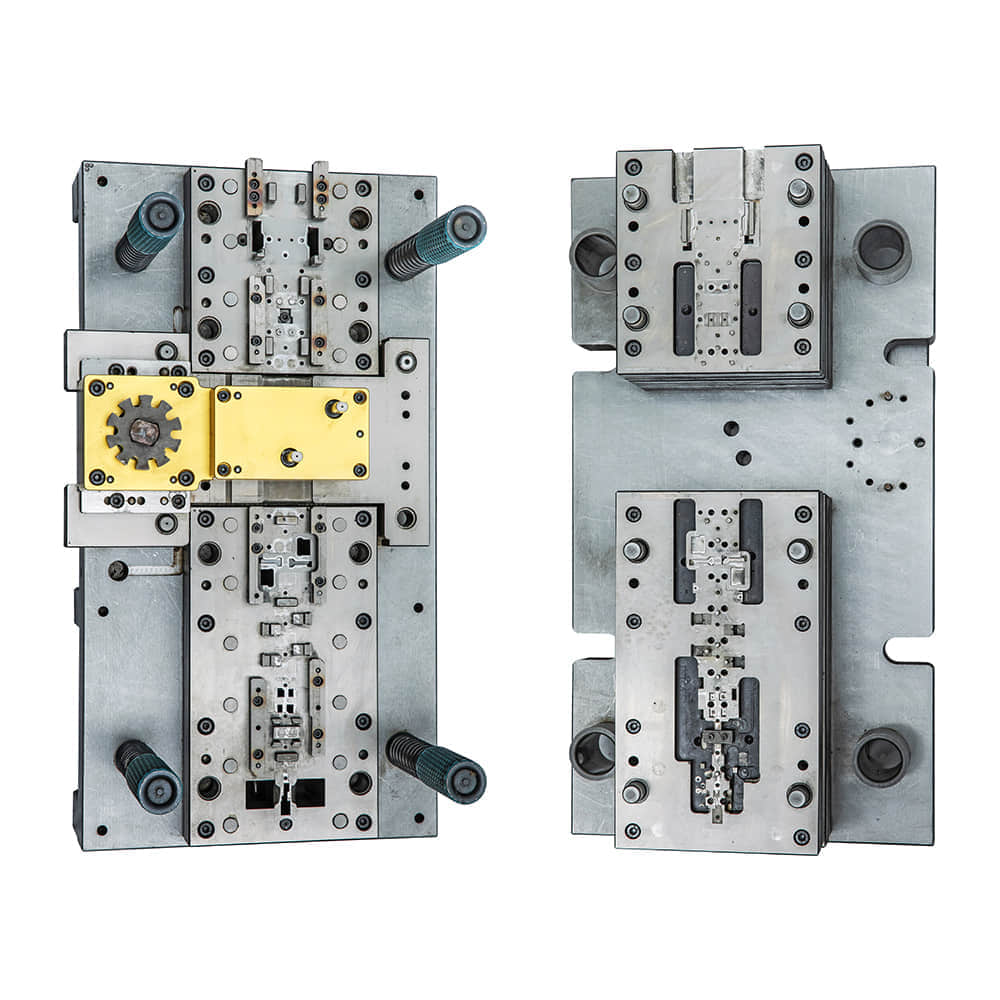