Injection molding is a remarkable manufacturing process that has transformed industries by enabling the mass production of intricate, high-quality components. This method, widely used in the manufacturing sector, involves injecting molten material into a mold cavity to create a specific shape. In this article, we will explore the world of injection molded parts, delving into their applications, advantages, and the intriguing process behind their creation.
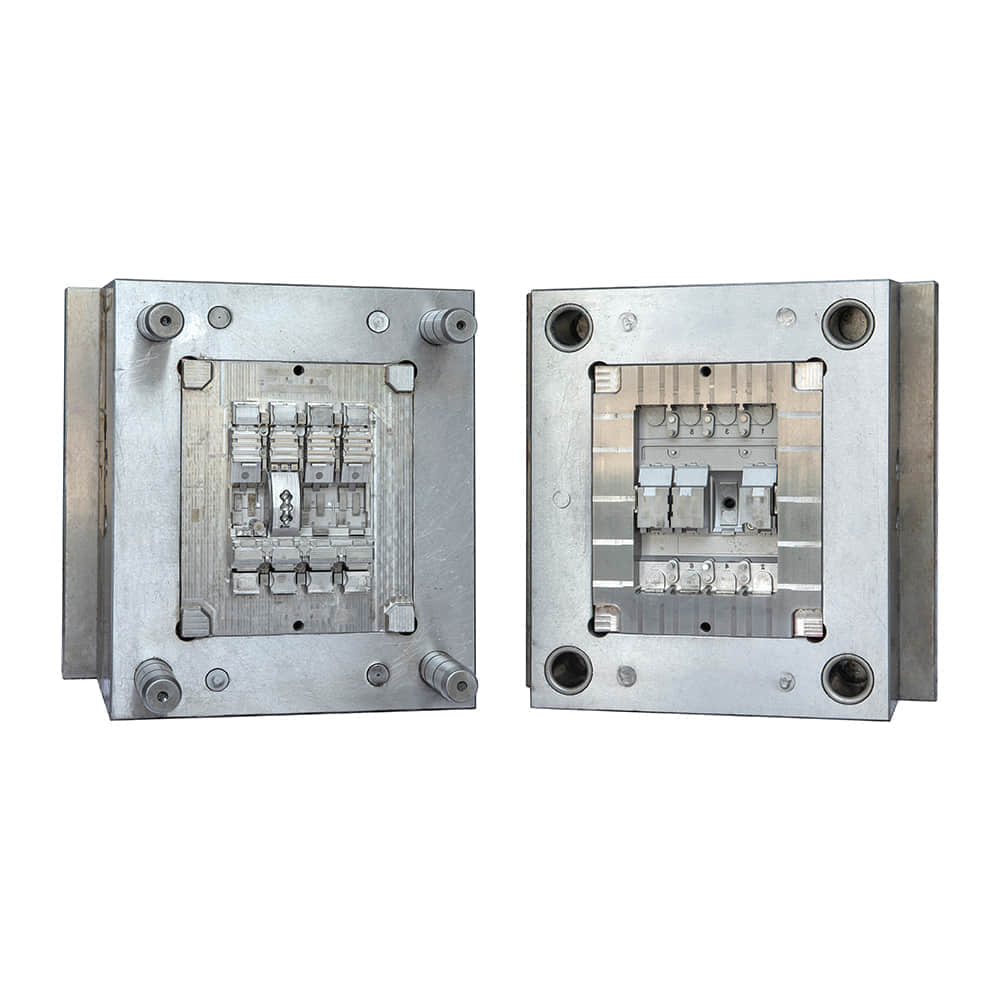
The Injection Molding Process
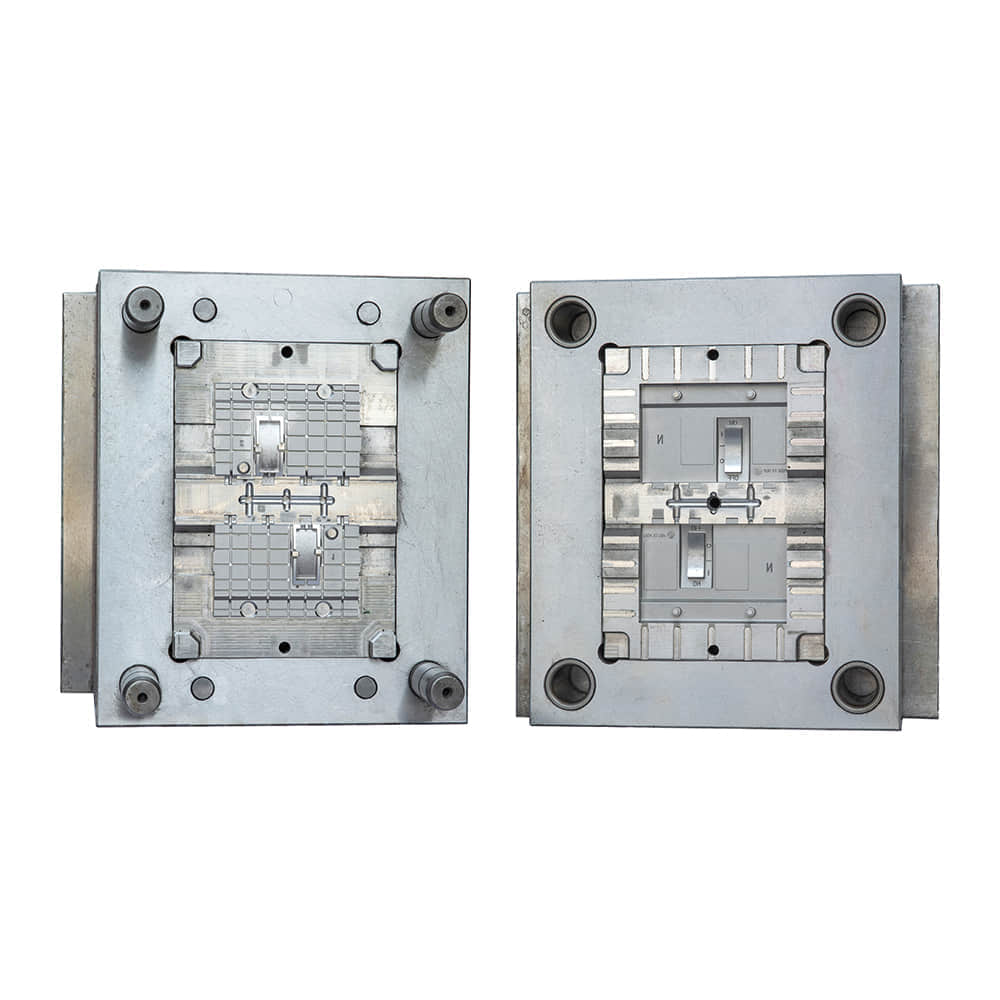
At the heart of injection molded parts lies a precise and efficient manufacturing process. It all begins with the selection of a suitable material, which can range from thermoplastics to metals. This material is heated until it reaches a molten state. Next, the molten material is injected into a carefully designed mold under high pressure. The mold itself is a critical component, as it defines the shape, dimensions, and surface finish of the final product. The injected material then cools and solidifies within the mold cavity, taking on its intended shape. Once cooled, the mold opens, and the newly formed part is ejected. This entire cycle can be completed in a matter of seconds, making injection molding one of the fastest and most efficient manufacturing processes available. Applications of Injection Molded Parts Injection molded parts find their way into an astonishing array of products and industries. From the dashboard of your car to the buttons on your TV remote, chances are that you interact with injection molded components daily. Some key areas where these parts excel include: Automotive Industry: Injection molding produces parts like bumpers, interior panels, and engine components, contributing to the safety, aesthetics, and functionality of vehicles. Electronics: The precise molding process is ideal for creating intricate parts found in smartphones, laptops, and consumer electronics. Medical Devices: Injection molding ensures the production of sterile and high-precision components used in medical equipment such as syringes, catheters, and IV connectors. Packaging: Many plastic containers, caps, and closures are made through injection molding, offering durability and cost-efficiency. Toys and Games: From action figures to board game pieces, injection molding allows for the mass production of colorful and detailed toys. Aerospace: The lightweight, high-strength materials used in aerospace applications benefit from injection molding to create complex and durable components. Advantages of Injection Molded Parts The popularity of injection molded parts can be attributed to several key advantages: High Precision: Injection molding offers exceptional dimensional accuracy and repeatability, ensuring consistent quality across production runs. Cost-Efficiency: The ability to produce large quantities quickly reduces per-unit costs, making it economical for mass production. Design Flexibility: Engineers and designers have the freedom to create intricate and complex shapes that would be challenging or impossible with other manufacturing methods. Material Variety: Injection molding supports a wide range of materials, from plastics and metals to elastomers and composites, allowing for versatility in product design. Minimal Waste: The process generates very little material waste, contributing to sustainability goals. Short Lead Times: Rapid cycle times mean that products can go from concept to market faster than many other manufacturing processes. Challenges and Considerations While injection molding is a powerful manufacturing technique, it does come with certain challenges. Designing molds can be expensive, especially for complex parts, and tooling can take time to develop. Additionally, material selection is critical, as different materials have varying properties and behaviors during the molding process. Ensuring proper cooling and ventilation in the mold is also essential to prevent defects. In conclusion, injection molded parts are the unsung heroes of modern manufacturing. They permeate nearly every aspect of our daily lives, contributing to the functionality and aesthetics of countless products. With its precision, efficiency, and versatility, injection molding continues to drive innovation and shape the future of manufacturing across various industries.
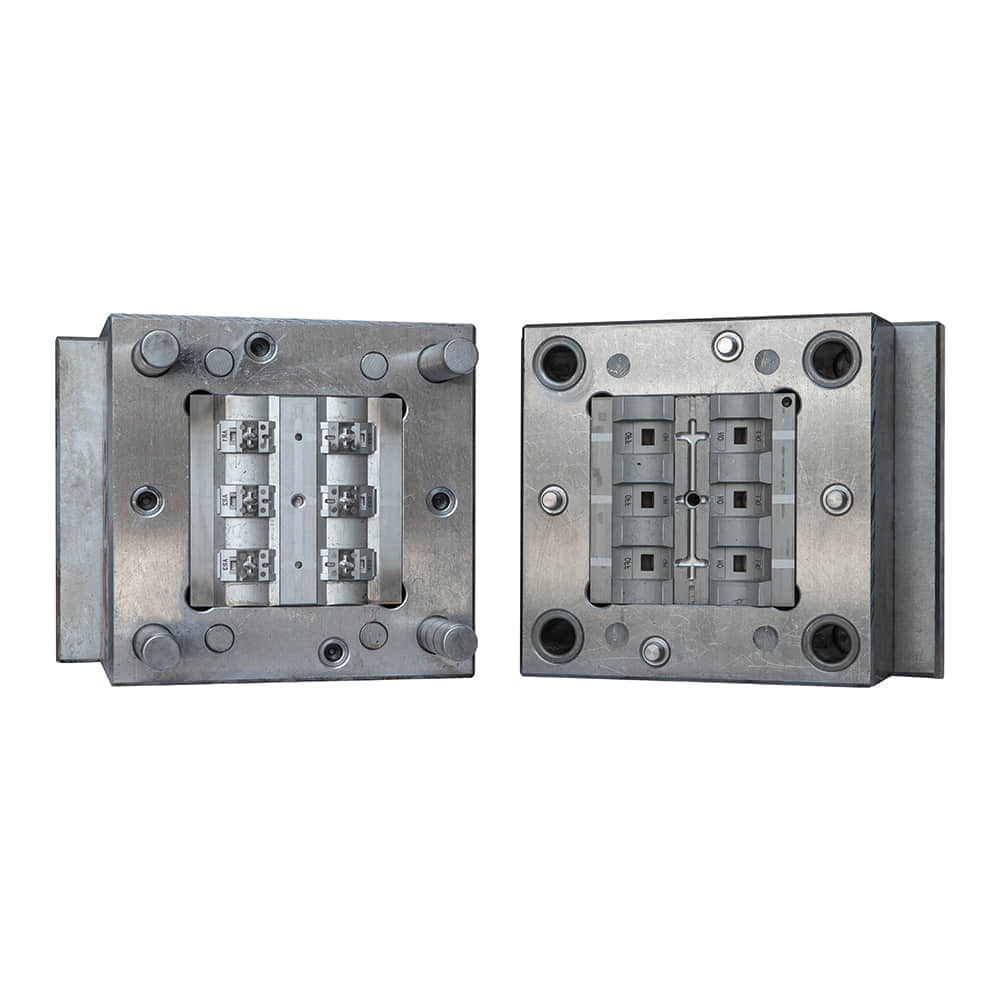