Injection molding is a highly versatile and widely utilized manufacturing process that plays a pivotal role in the production of countless products we encounter in our daily lives. From the casing of your smartphone to the interior components of your car, injection molded parts are everywhere, thanks to their precision, cost-effectiveness, and efficiency. In this article, we will delve into the world of injection molded parts, exploring their applications, the molding process, and their impact on various industries.
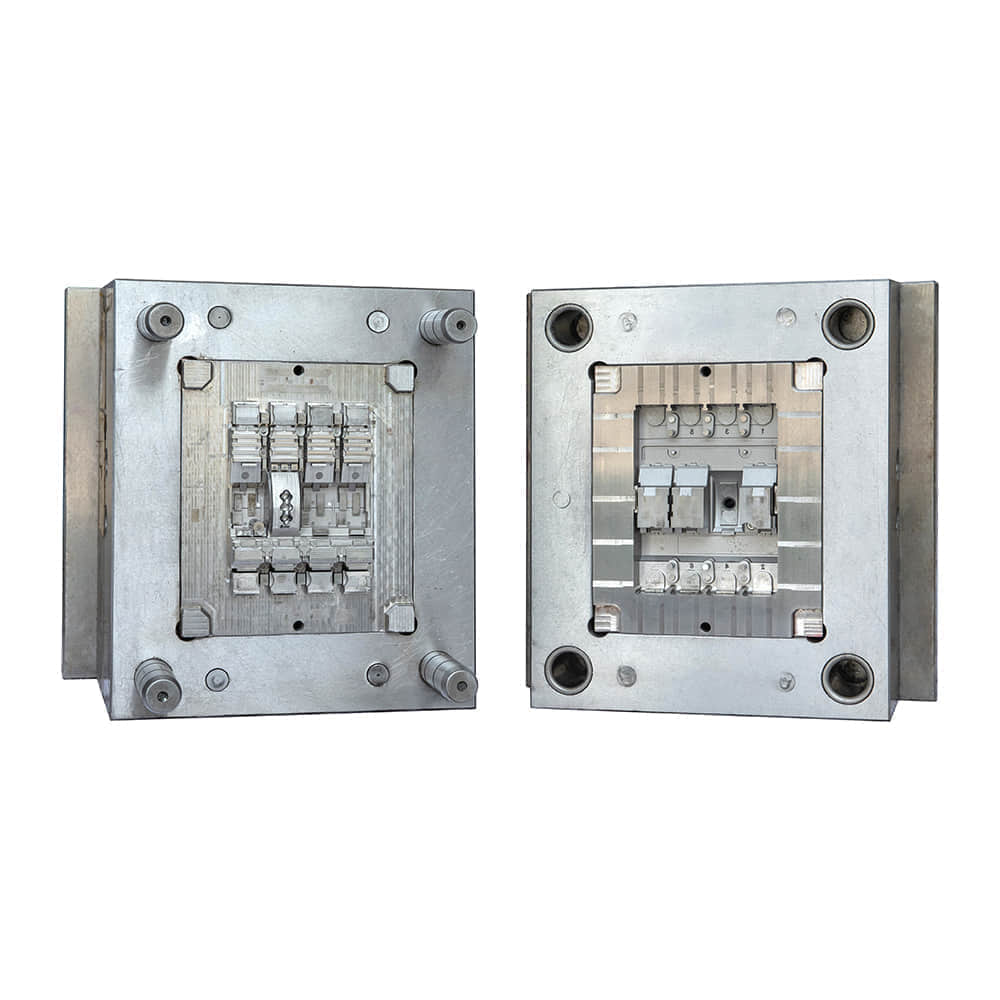
The Injection Molding Process
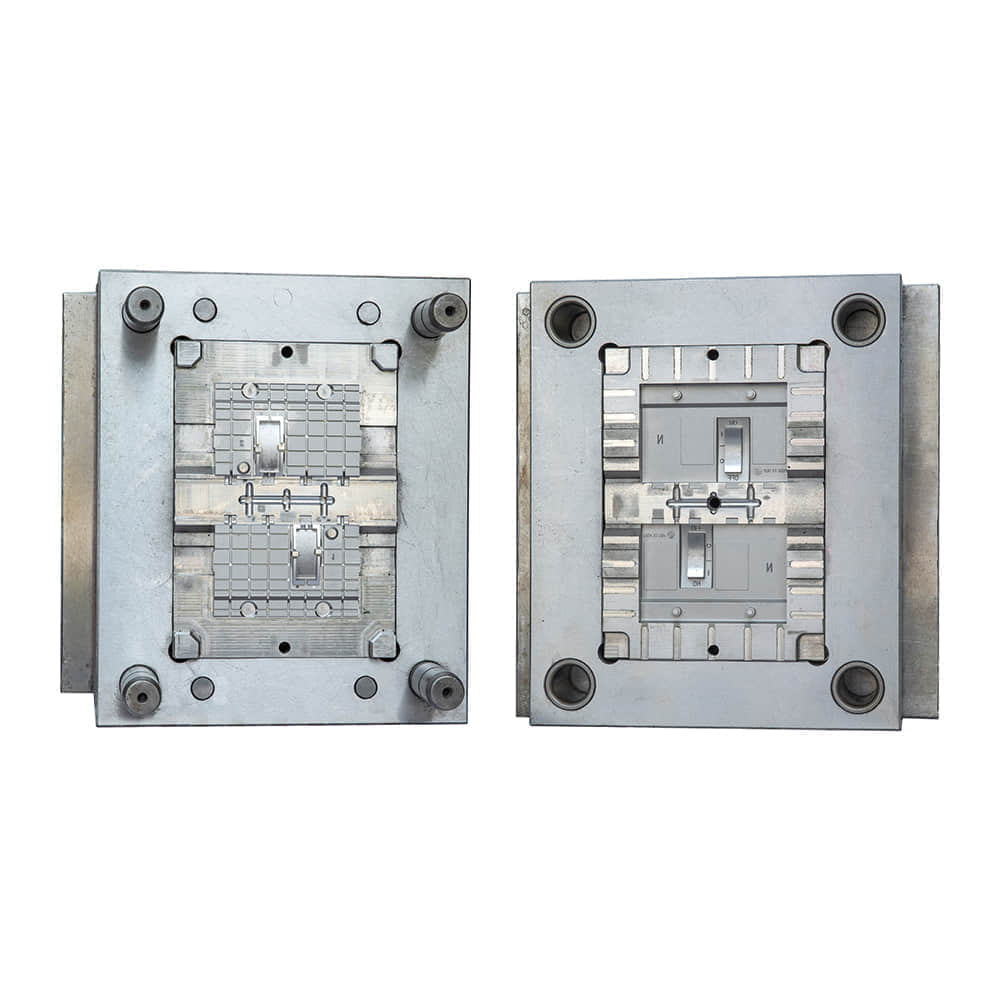
Injection molding is a manufacturing technique that involves injecting molten material into a mold cavity, allowing it to cool and solidify to create a three-dimensional object. The process is meticulously controlled and can accommodate a wide range of materials, including plastics, metals, ceramics, and even composite materials. Material Preparation: The process begins with the preparation of the raw material, typically in the form of pellets or granules. These materials are loaded into a hopper, where they are heated to a molten state. Injection: Once the material reaches the desired temperature, it is injected into the mold cavity under high pressure. The mold is typically made of two halves, known as the mold core and mold cavity, which come together to form the desired shape. Cooling and Solidification: The injected material rapidly cools and solidifies within the mold, taking on the precise shape of the cavity. Ejection: After solidification, the mold opens, and the finished part is ejected. The cycle then repeats for the next part. Applications in Diverse Industries Injection molding is celebrated for its versatility, making it a cornerstone of numerous industries: Automotive: From dashboard components to interior panels, injection molded parts are integral to the automotive industry. They offer lightweight, durable, and cost-effective solutions for various applications. Electronics: The compact nature of electronics demands precision in design and production. Injection molding produces intricately detailed casings and connectors for devices such as smartphones, laptops, and cameras. Medical: In the medical field, sterile and biocompatible materials are essential. Injection molding is used to create syringes, IV components, and medical device housings with high precision and consistency. Consumer Goods: Toys, kitchen appliances, and household items often feature injection molded parts due to their affordability and ability to replicate intricate designs. Aerospace: The aerospace sector relies on injection molding for lightweight, high-strength components like interior cabin panels, seat parts, and air ducts. Advantages of Injection Molded Parts Injection molding offers a myriad of advantages that contribute to its popularity: Precision: The process allows for intricate detailing and tight tolerances, ensuring that each part is consistent and accurate. Cost-Effective: Injection molding is cost-effective for high-volume production, as the cost per part decreases with increased quantities. Material Variety: An extensive range of materials can be used, from thermoplastics to thermosetting polymers, allowing manufacturers to select the most suitable material for their application. High Efficiency: The high-speed production cycles of injection molding result in efficient manufacturing, reducing lead times and production costs. Low Waste: Minimal material is wasted during the injection molding process, making it environmentally friendly. Conclusion Injection molded parts are the unsung heroes of modern manufacturing, contributing to the creation of countless products that enhance our lives. With their precision, versatility, and cost-effectiveness, they have become indispensable in industries ranging from automotive to electronics. As technology advances, injection molding continues to evolve, promising even greater possibilities for innovation in the future. Whether you’re holding a plastic smartphone case or driving a car with injection molded interior components, these parts are a testament to the remarkable capabilities of injection molding.
