In today’s fast-paced manufacturing landscape, precision and efficiency are paramount. Injection mold manufacturers play a pivotal role in ensuring that the products we use every day are not only functional but also aesthetically pleasing. These skilled artisans are the unsung heroes behind the scenes, and this article delves into the world of injection mold manufacturers, shedding light on their crucial role in modern production.
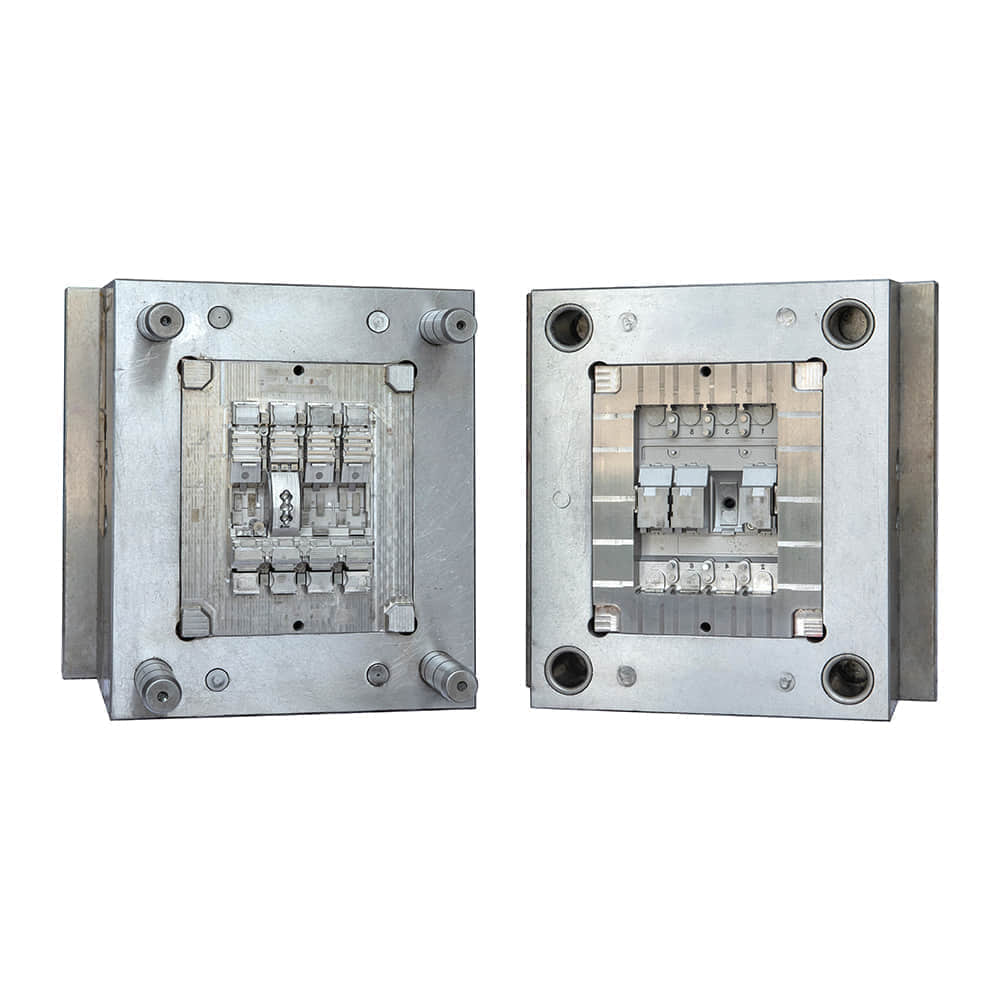
Molding the Foundation:
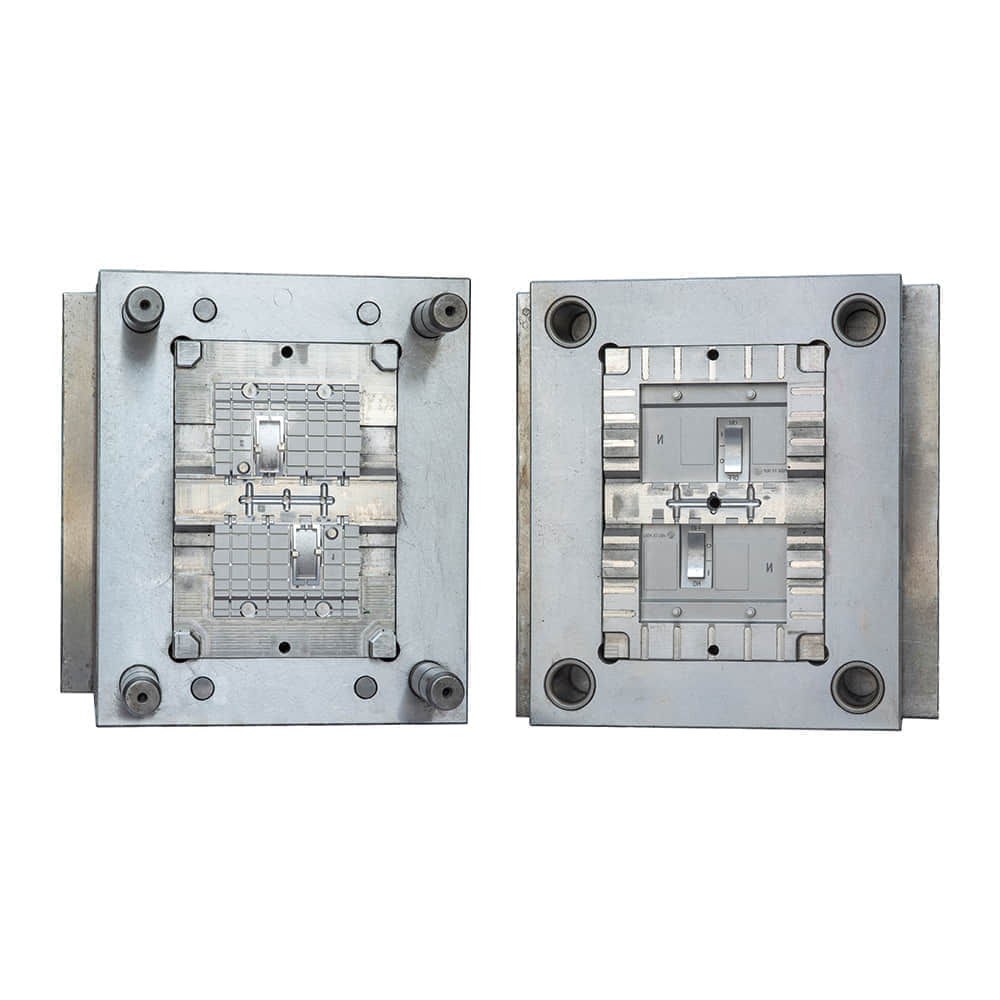
Injection mold manufacturing is a complex process that involves creating molds for mass-producing a wide range of plastic and metal products. These molds serve as the foundation upon which countless items are built, from car parts to consumer electronics and medical devices. Without these meticulously crafted molds, the modern world as we know it would not exist. The Art and Science of Mold Making: Creating injection molds is a blend of art and science. Manufacturers must have a deep understanding of materials, design principles, and engineering techniques. They must also possess a keen eye for detail and a high level of craftsmanship. The process typically begins with a product design. Engineers work closely with designers to create a 3D model of the desired product. From there, the mold design process begins. This stage is critical, as it determines the quality and consistency of the final product. Injection mold manufacturers meticulously design the mold’s cavities and cores to ensure precision and accuracy during production. Materials Matter: Injection molds are usually made from high-quality materials like steel or aluminum. These materials are chosen for their durability and ability to withstand the high temperatures and pressures involved in the injection molding process. The choice of material depends on the specific requirements of the product and the expected production volume. The Precision Process: Once the mold is designed and fabricated, it’s time for the injection molding process. This involves injecting molten material into the mold cavity at high pressure. The material then cools and solidifies, taking the shape of the mold. The mold is then opened, and the newly formed product is ejected. Precision is key during this phase. The mold must be able to create identical products, ensuring consistency and quality. Any imperfections in the mold can result in defects in the final product, which can be costly and compromise safety. Continuous Improvement: Injection mold manufacturers are constantly striving for improvement. They invest in cutting-edge technology and machinery to enhance the precision and efficiency of the mold-making process. Computer-aided design (CAD) and computer-aided manufacturing (CAM) systems have revolutionized the industry, allowing for even greater accuracy and speed in mold production. Meeting Industry Demands: The demand for injection mold manufacturers has surged in recent years. Industries such as automotive, electronics, and medical devices rely heavily on injection molding to produce components quickly and efficiently. This increased demand has driven manufacturers to innovate and adapt to new challenges. Environmental Considerations: In an era where environmental sustainability is a top priority, injection mold manufacturers are also taking steps to reduce their ecological footprint. Many are adopting eco-friendly materials and processes, such as biodegradable plastics and energy-efficient machinery, to minimize environmental impact. Conclusion: Injection mold manufacturers are the unsung heroes of modern manufacturing. Their precision craftsmanship and dedication to producing high-quality molds are essential for the production of countless products that improve our lives. As technology advances and the demand for precision and efficiency continues to grow, these skilled artisans will remain at the forefront of innovation in the manufacturing industry, shaping the future of production one mold at a time.
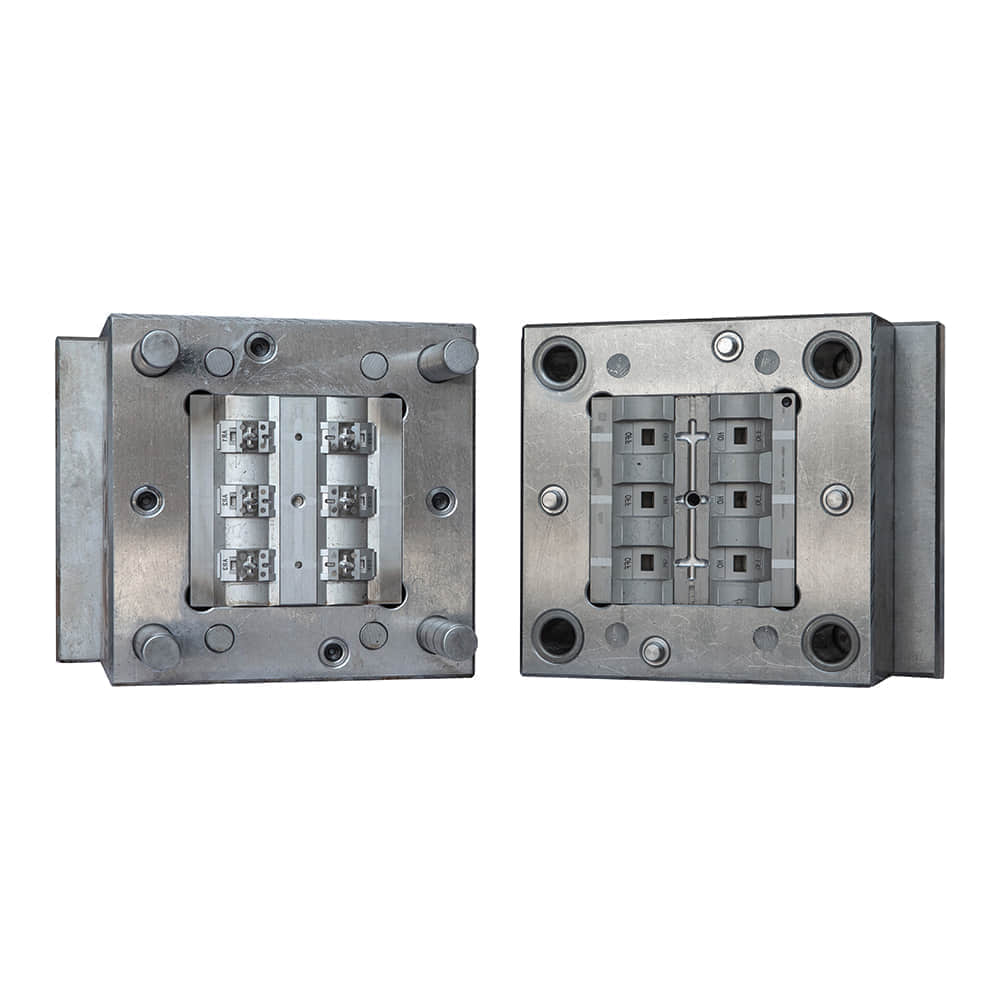