Electric actuator valves are essential components in modern industrial automation systems, offering efficient and reliable control over fluid and gas flow in various applications. These valves, equipped with electric actuators, are used to automate the operation of shut-off, throttling, or regulating valves. Their increasing adoption across industries such as oil and gas, water treatment, HVAC systems, and chemical processing is a testament to their effectiveness and growing popularity. In this article, we will explore the functionality, types, advantages, and applications of electric actuator valves, and how they contribute to the optimization of industrial processes.
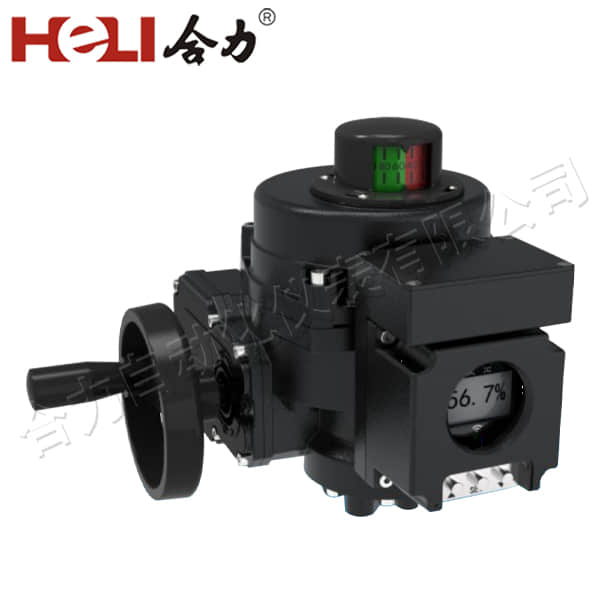
What is an Electric Actuator Valve?
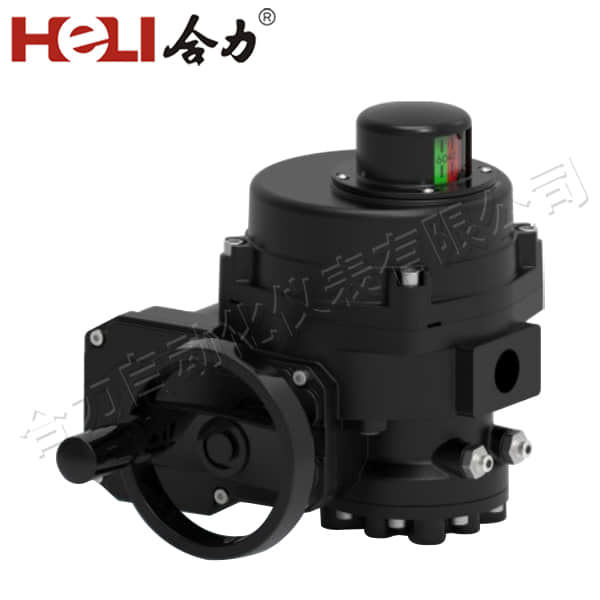
An electric actuator valve is a valve mechanism driven by an electric motor that controls the opening and closing of the valve. The electric actuator receives a signal from a controller (often part of a larger automated system) and uses electrical energy to convert rotational motion into mechanical force. This force operates the valve stem, which in turn opens or closes the valve. This electric control offers precise adjustments, making it ideal for applications where accurate flow regulation is crucial. The primary components of an electric actuator valve include the electric actuator (motor), valve body, actuator controller, and feedback system. The actuator itself may be a direct-drive or a gear-driven electric motor, depending on the required torque and stroke length. The feedback system ensures the valve’s position is communicated to the control system, allowing for continuous monitoring and optimization.
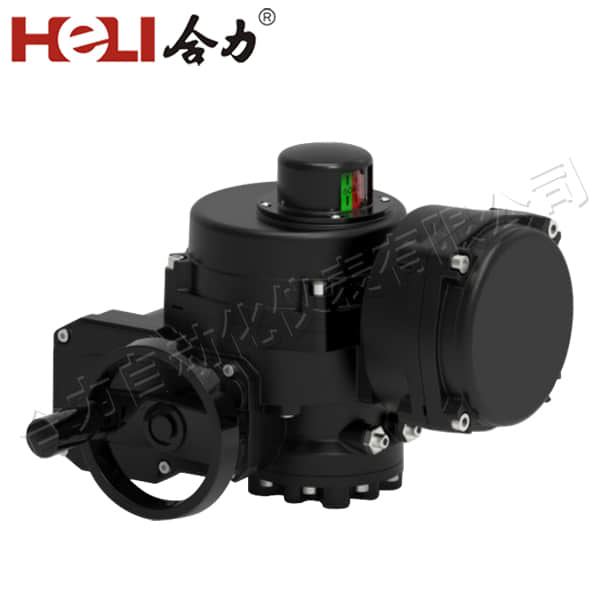