In the fast-paced world of modern manufacturing, the Progressive Die has emerged as a game-changing tool, revolutionizing the way we approach stamping and metal forming processes. This sophisticated mold type, with its ability to perform multiple operations in a single cycle, has become a cornerstone of high-volume production, ensuring efficiency, precision, and cost-effectiveness.
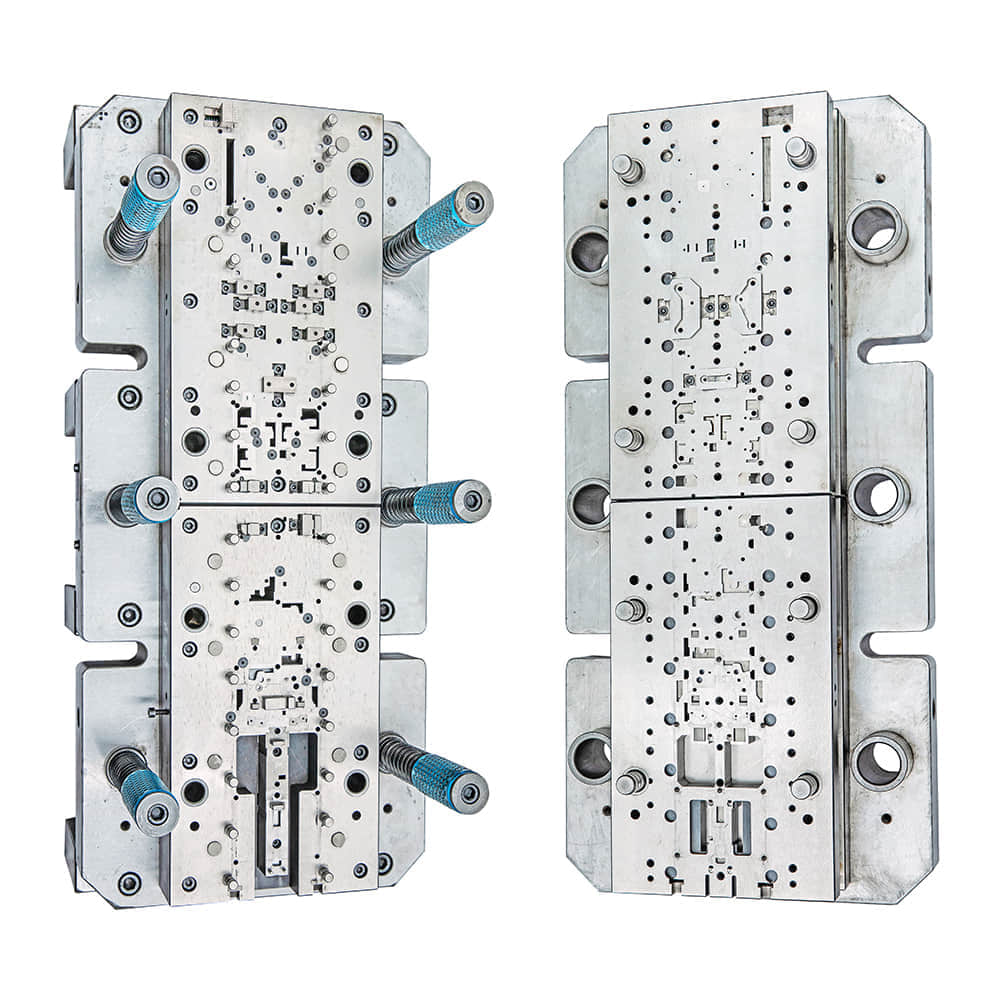
The Progressive Die, also known as a sequential mold or multi-station die, operates on a principle that involves the progressive movement of the workpiece through multiple stations. Each station performs a specific operation, such as punching, cutting, bending, or forming, on the material. As the workpiece advances through these stations, it gradually transforms into the desired final product.
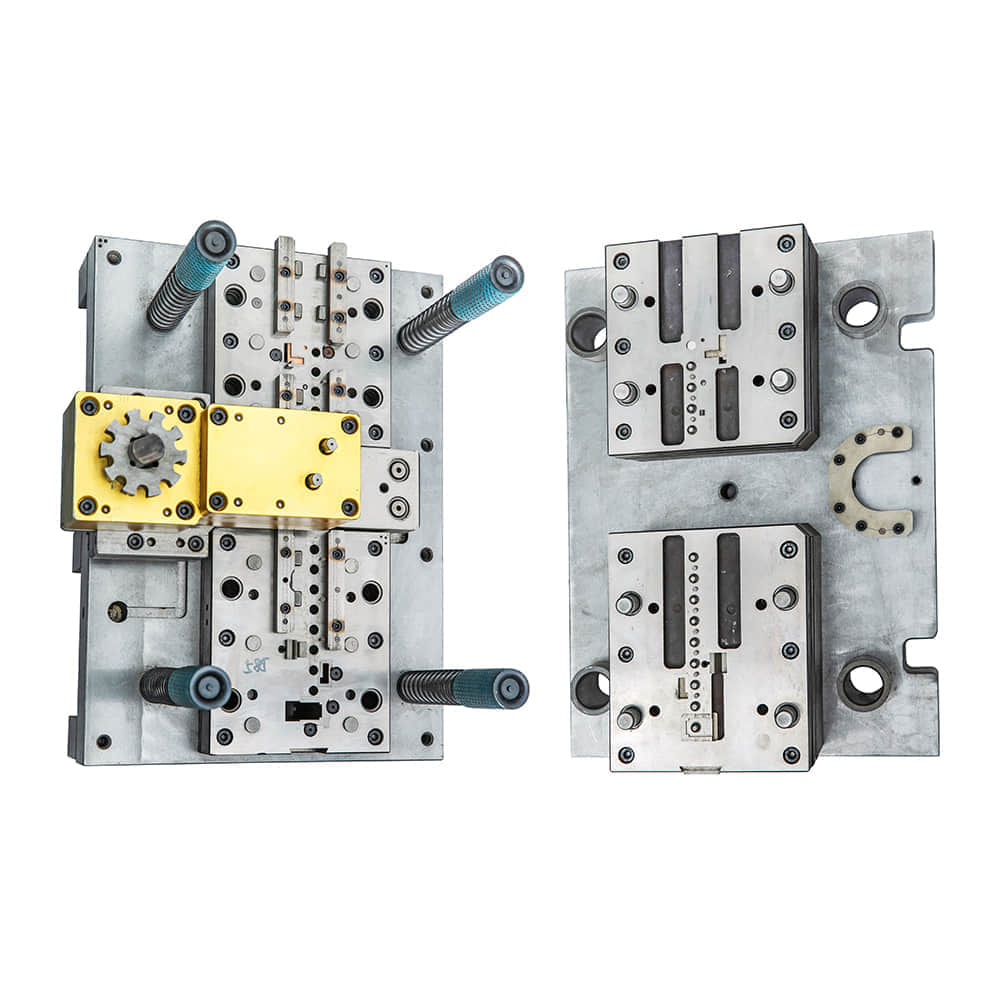
The beauty of the Progressive Die lies in its ability to streamline the manufacturing process. Instead of relying on multiple separate operations and tools, the Progressive Die combines them into a single, continuous cycle. This not only reduces the need for handling and transfer between different machines but also eliminates the potential for human error and variation. Moreover, the Progressive Die ensures a high degree of precision and consistency in the final product. Since all operations are performed within the same mold, there is minimal room for deviation or imperfections. This is particularly crucial in industries that demand tight tolerances and exacting standards, such as automotive and electronics.
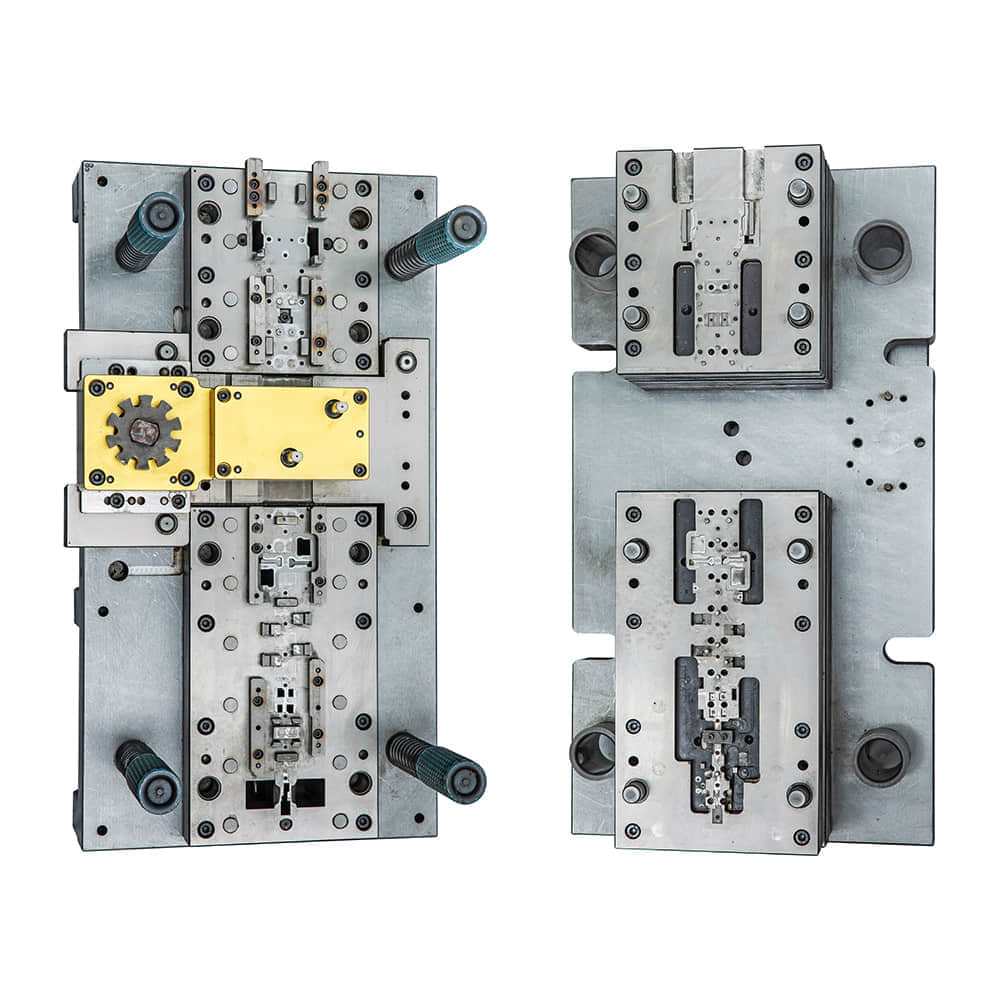