Thermoplastic injection molds have revolutionized the manufacturing industry, enabling the production of a wide range of products with precision and efficiency. In this article, we will delve into the fascinating world of thermoplastic injection molds, exploring their applications, advantages, and the innovative techniques driving this dynamic field.
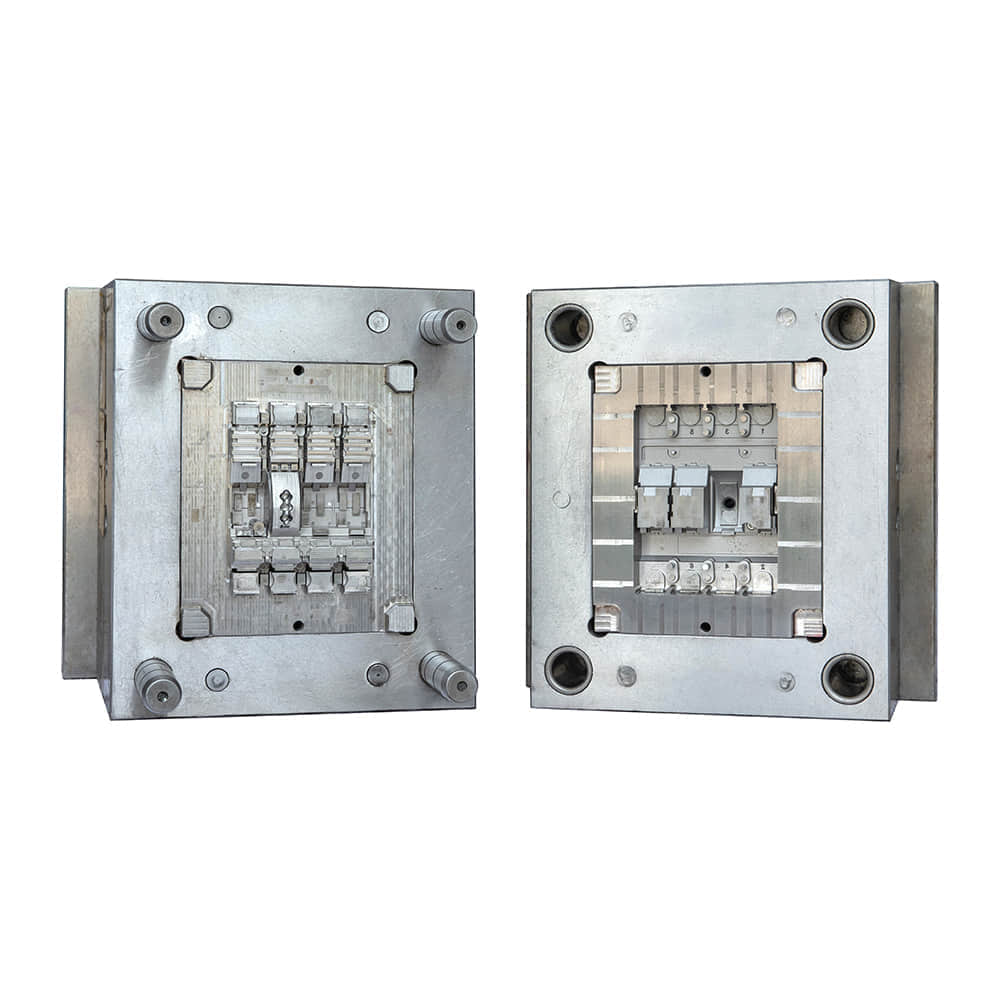
The Basics of Thermoplastic Injection Molding
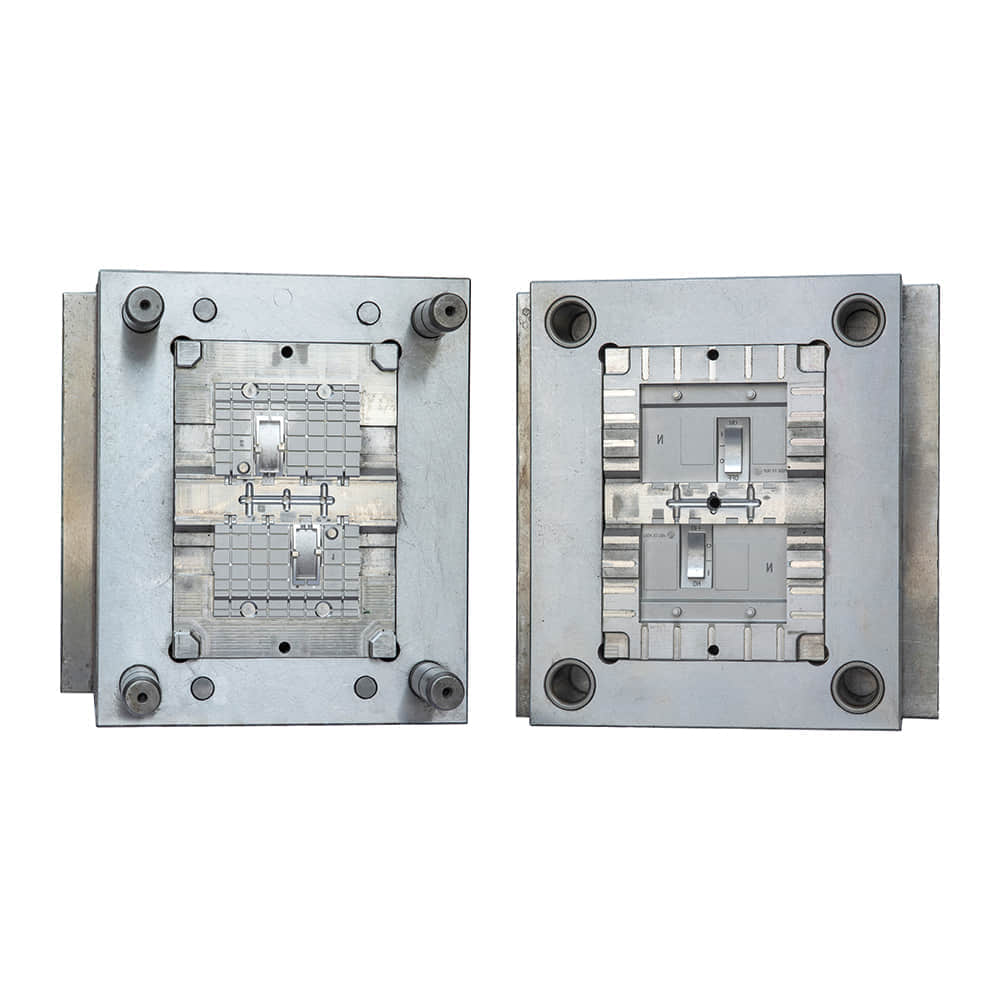
Thermoplastic injection molding is a manufacturing process that involves the injection of molten thermoplastic material into a mold cavity. Once the material cools and solidifies, the mold is opened, and the finished product is ejected. This process is known for its speed, accuracy, and ability to produce intricate and complex parts. Diverse Applications Thermoplastic injection molds find applications in various industries, including automotive, electronics, medical, and consumer goods. They are used to create components ranging from tiny microchips to large automotive parts. This versatility is a testament to the adaptability of thermoplastic injection molding technology. Advantages of Thermoplastic Injection Molds Precision: Thermoplastic injection molds offer unparalleled precision and repeatability, ensuring each product meets exact specifications. This precision is crucial in industries where safety and performance standards are paramount. Efficiency: The high-speed nature of injection molding allows for the rapid production of large quantities of parts. This efficiency reduces production costs and cycle times, making it an attractive option for manufacturers. Design Freedom: Injection molds can create intricate and complex shapes that would be challenging or impossible to achieve with other manufacturing processes. This design freedom encourages innovation in product design. Material Variety: Thermoplastic injection molding supports a wide range of thermoplastic materials, each with unique properties. Manufacturers can choose materials that offer the desired strength, flexibility, heat resistance, or other characteristics. Innovations in Thermoplastic Injection Molding The field of thermoplastic injection molding is continuously evolving, driven by technological advancements and the demand for more sustainable and efficient manufacturing processes. Some notable innovations include: 3D Printing Integration: 3D printing technology is increasingly integrated into injection molding processes, enabling rapid prototyping and tooling production. This synergy reduces lead times and allows for more efficient design iterations. Sustainable Materials: With growing environmental concerns, there is a focus on developing sustainable thermoplastic materials. Bioplastics and recycled plastics are becoming more common in injection molding, contributing to a greener manufacturing industry. Smart Manufacturing: IoT (Internet of Things) technologies are being employed to create “smart” injection molding machines that can monitor and adjust various parameters in real-time, optimizing production and minimizing waste. Micro Injection Molding: Advancements in micro injection molding techniques have opened doors for the production of tiny, high-precision components used in industries like medical devices and electronics. Conclusion Thermoplastic injection molds have firmly established themselves as a cornerstone of modern manufacturing. Their versatility, precision, and efficiency make them a vital tool in various industries. As technology continues to advance, we can expect even more innovations in this field, further expanding the possibilities and applications of thermoplastic injection molding. Whether it’s producing essential medical devices or crafting intricate consumer products, the world of thermoplastic injection molds continues to shape our modern world.
