In the dynamic world of manufacturing, Thermosetting mold manufacturers occupy a pivotal position. These specialized companies are the unsung heroes behind the production of a wide range of products, from automotive parts to electrical components. The rise of thermosetting mold manufacturers can be attributed to the unique properties and versatility of thermosetting plastics.
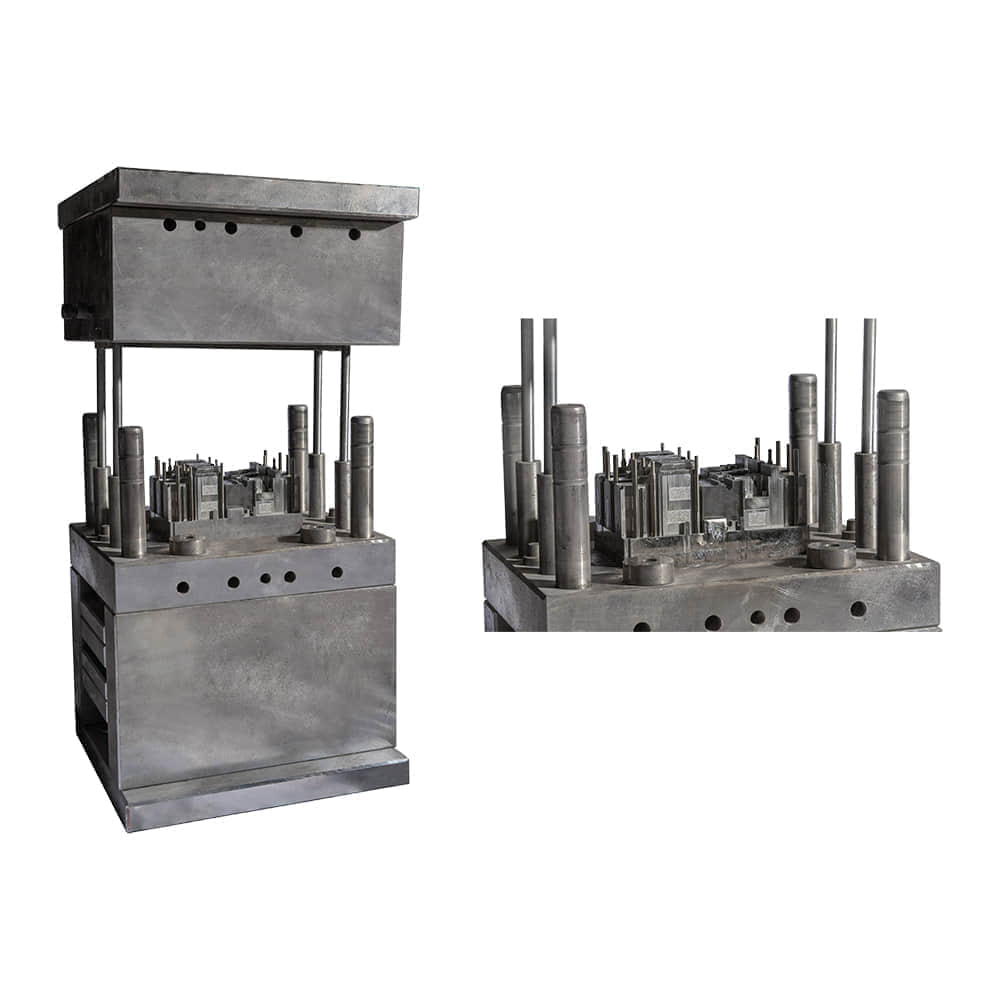
Thermosetting plastics, unlike thermoplastics, undergo irreversible chemical changes during the molding process, resulting in strong and durable finished products. This characteristic makes them ideal for applications that require high heat resistance, mechanical strength, and chemical stability. Thermosetting mold manufacturers leverage these properties to create molds that are precision-engineered and optimized for specific manufacturing needs.
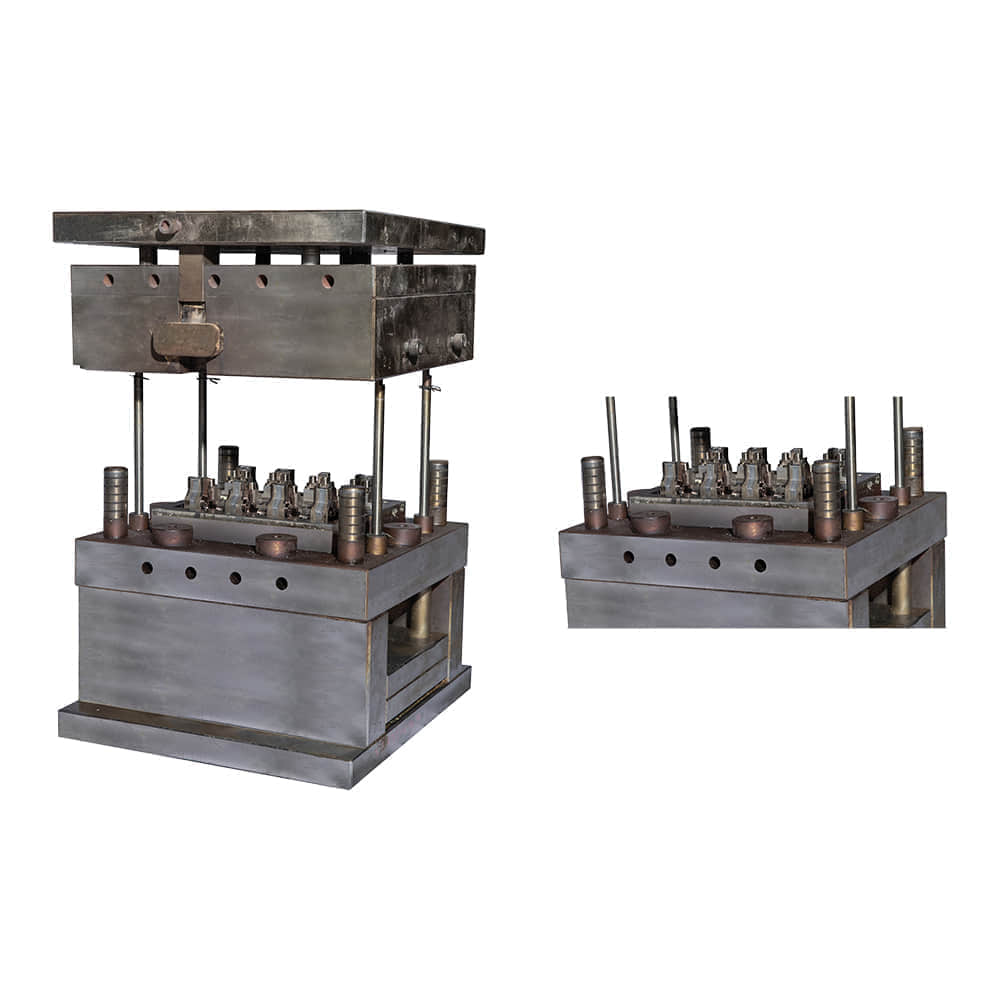
The manufacturing process of thermosetting molds involves intricate steps that require expertise and precision. Manufacturers begin with the design phase, where they collaborate with clients to understand their specific requirements and create a mold design that meets their needs. This involves considering factors such as part geometry, material selection, and production volume. Once the design is finalized, manufacturers proceed to the manufacturing phase. This involves the use of advanced machining techniques and equipment to create the mold from high-quality materials. The selection of materials is crucial as it directly impacts the performance and durability of the finished mold. Thermosetting mold manufacturers ensure that the materials used are compatible with the thermosetting plastic and capable of withstanding the high temperatures and pressures involved in the molding process.
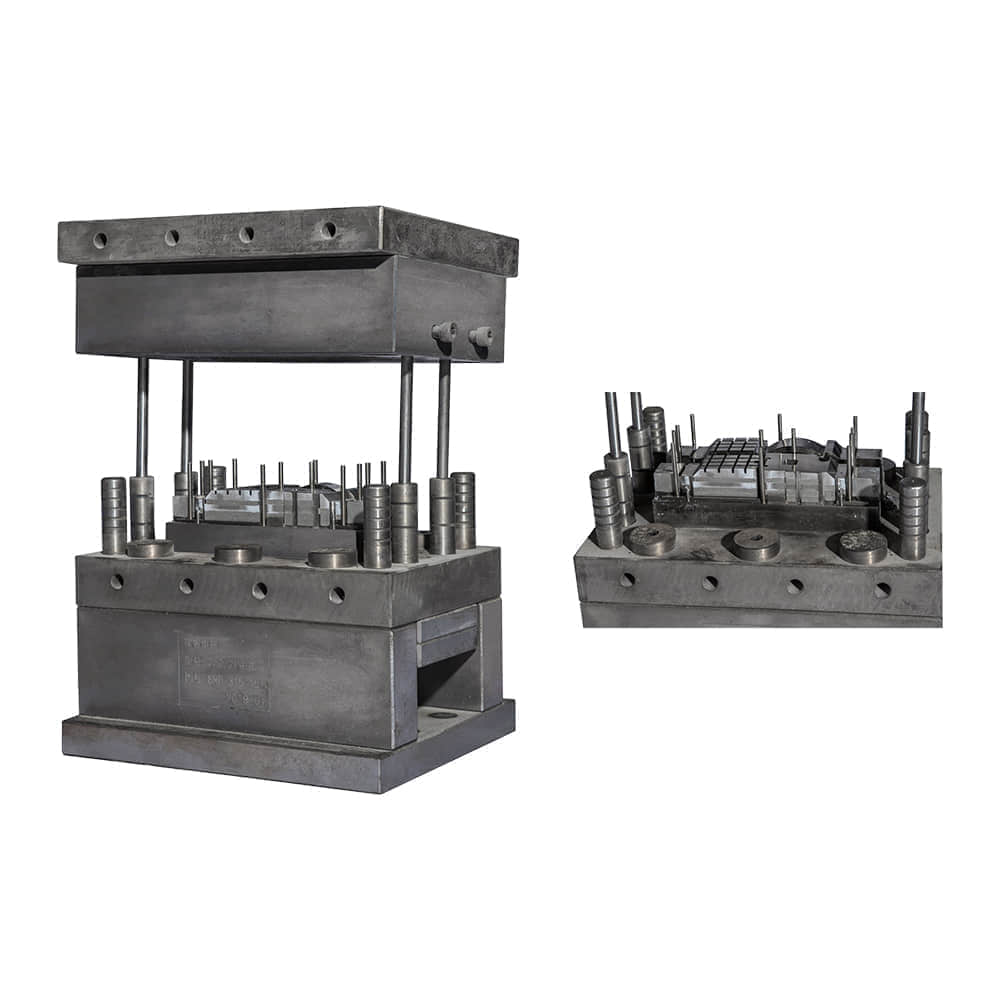