Metal stamping parts play a pivotal role in the modern manufacturing industry, serving as the backbone of various industrial applications. This process, also known as cold stamping or sheet metal stamping, involves the deformation of metal sheets into desired shapes and sizes using precision dies and stamping presses. The versatility and efficiency of metal stamping parts have made them indispensable in various industries, from automotive to electronics.
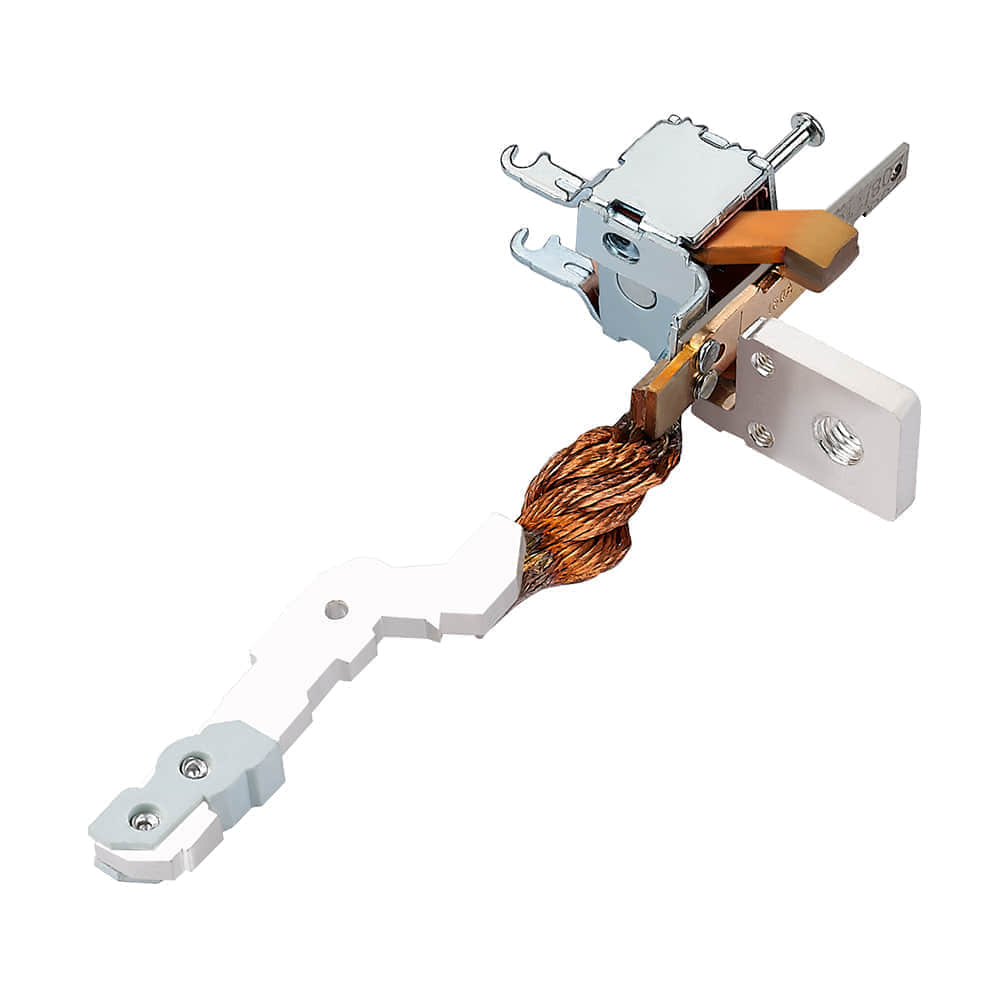
The fundamental principle of metal stamping lies in the plastic deformation of metal sheets under controlled conditions. The stamping press applies force to the metal sheet, causing it to flow into the contours of the die, resulting in the desired shape. This process is highly repeatable, ensuring consistent quality and accuracy in mass production.
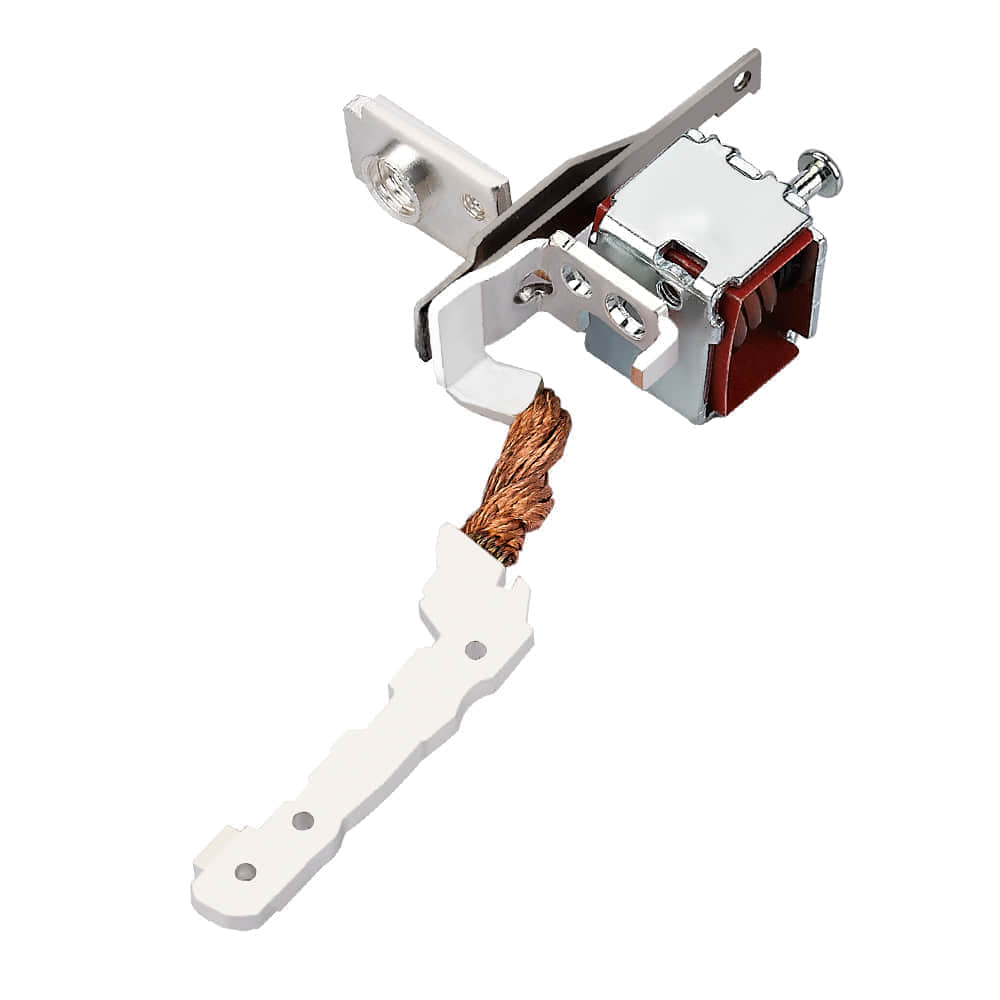
The widespread use of metal stamping parts is attributed to several key advantages. Firstly, the stamping process is highly efficient, allowing for rapid production of large quantities of parts. This is particularly beneficial in industries that require high-volume manufacturing, such as the automotive sector. Secondly, metal stamping parts exhibit excellent precision and dimensional stability, ensuring tight tolerances and high-quality finishes. This is crucial in applications where accuracy and reliability are paramount, such as in the aerospace and medical industries. Moreover, the stamping process offers flexibility in terms of material selection. A variety of metals, including steel, aluminum, and stainless steel, can be stamped into intricate shapes and sizes. This flexibility allows manufacturers to tailor the properties of metal stamping parts to meet specific application requirements, such as strength, corrosion resistance, or weight reduction.
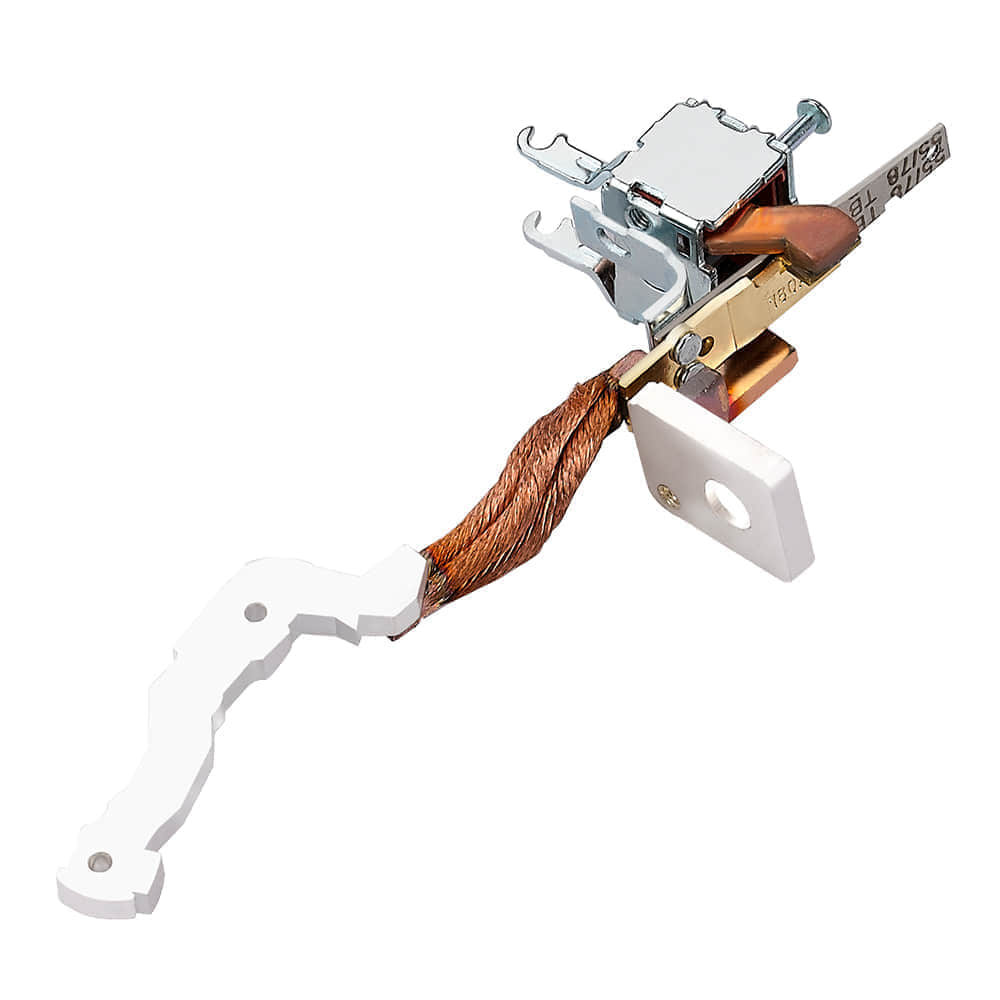