Thermosetting Compression Moulding, a crucial plastic molding technique, holds a significant place in the manufacturing industry. This process, primarily used for thermosetting plastics like phenolic, amino, and unsaturated polyester, involves the plasticization and flow of raw plastic materials under heat and pressure to fill the mold cavity, followed by chemical crosslinking to achieve solidification.
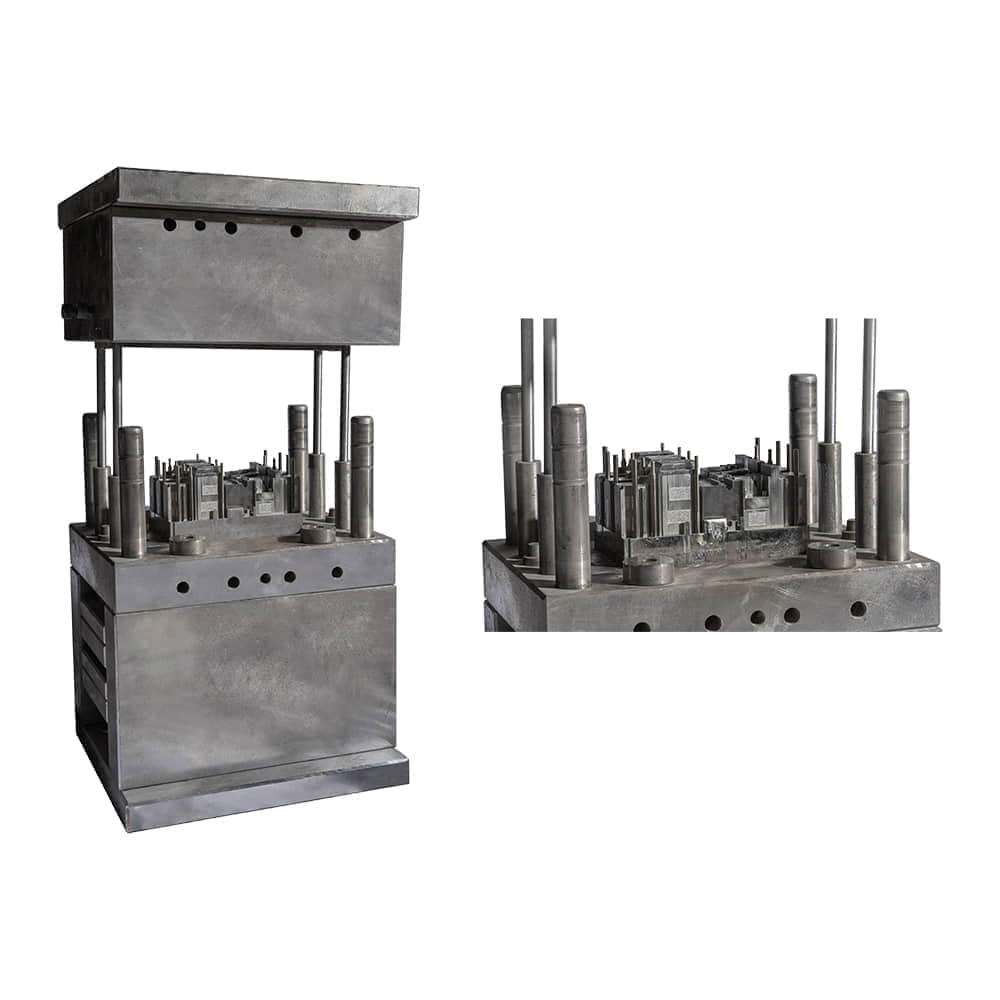
The process begins with the preparation of the mold, which is heated to a predetermined temperature. The accurately measured plastic material is then placed into the mold cavity. As the mold closes, the plastic material is compressed and heated, causing it to melt and flow, filling every corner of the mold. This stage is followed by the elimination of trapped air or gases from the molten plastic.
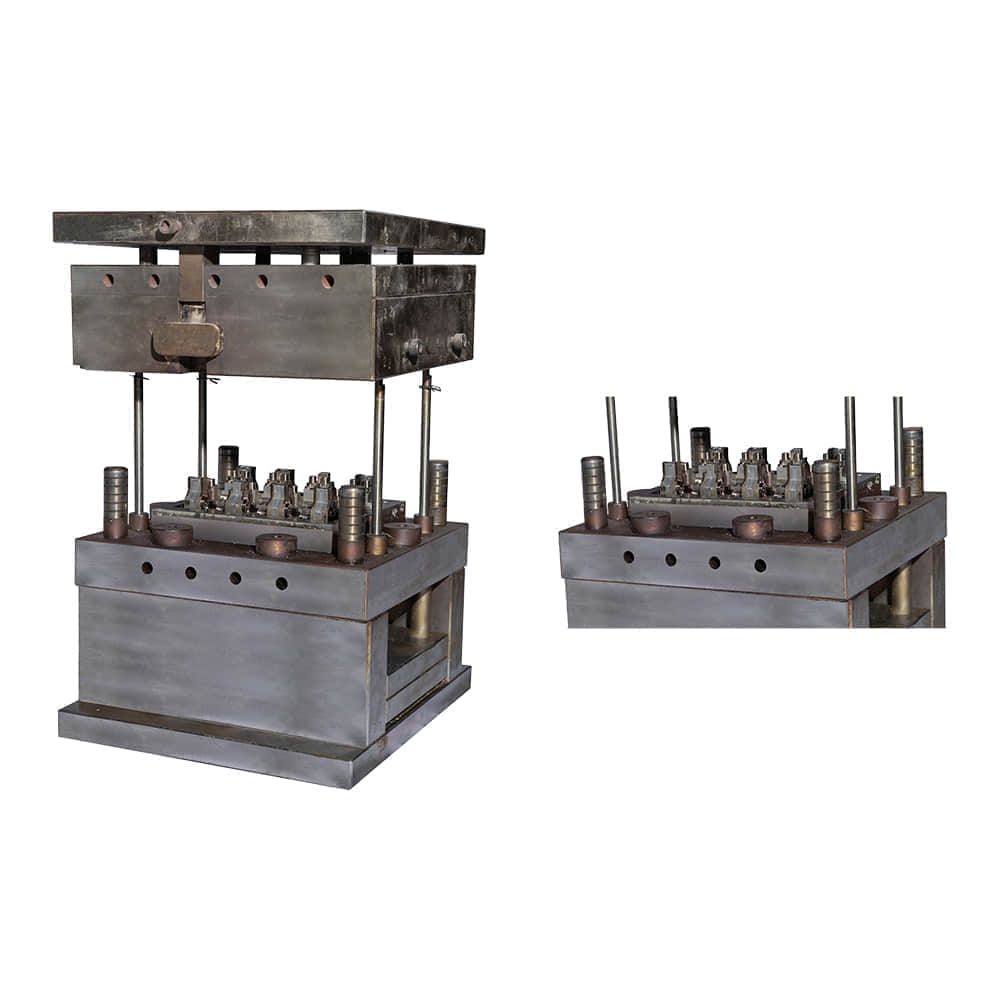
The heart of the process lies in the chemical crosslinking reaction that occurs during the curing phase. This reaction solidifies the plastic, giving it its final shape and properties. The curing time and temperature are carefully controlled to ensure optimal crosslinking and mechanical properties. Once the curing is complete, the mold is opened, and the solidified plastic part is ejected. Post-processing steps like trimming, sanding, or painting may be necessary to achieve the desired finish. The advantages of Thermosetting Compression Moulding are numerous. It produces parts with complex geometries and tight tolerances, ensuring high precision and accuracy. The low shrinkage rate during the curing process further enhances the dimensional stability of the final product. Additionally, the process allows for the use of reinforcements like fibers or fillers, enhancing the mechanical properties of the plastic.
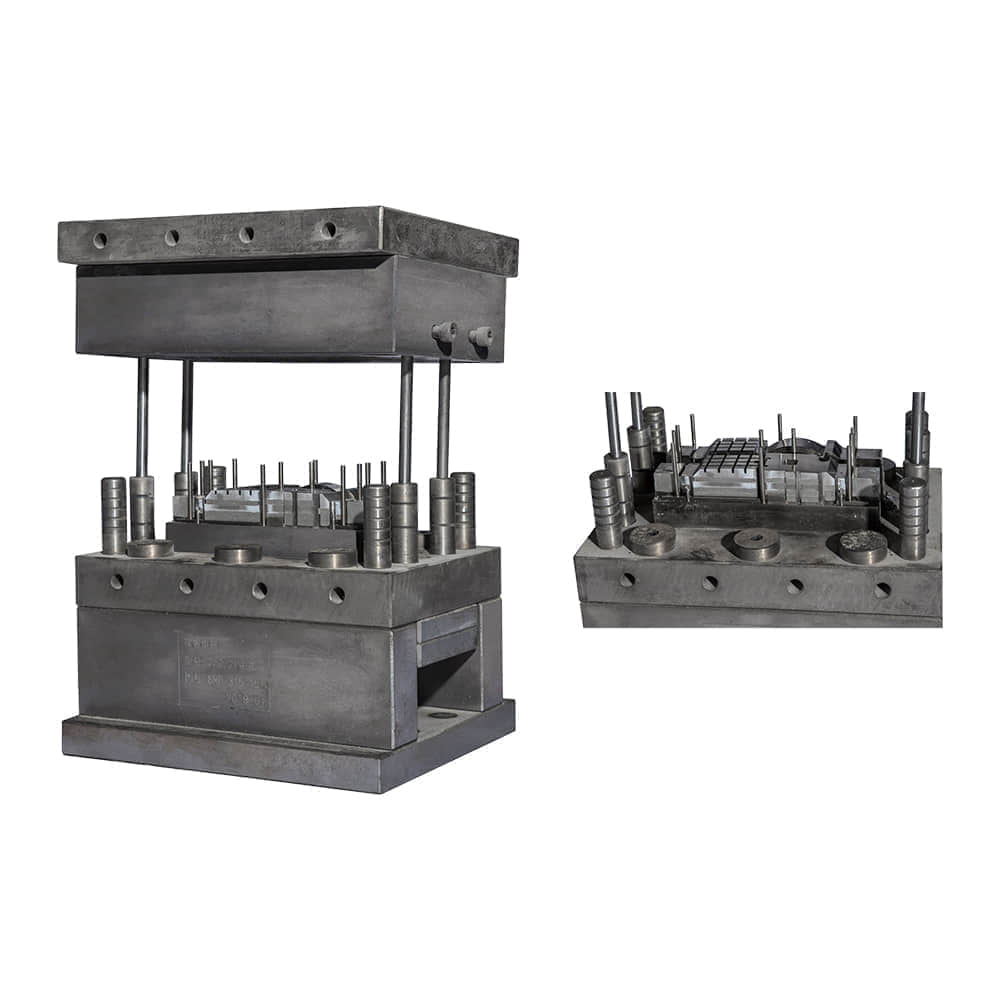