Blanking dies are essential tools in the world of metalworking and manufacturing. They play a pivotal role in cutting and shaping various materials with precision and accuracy. In this article, we will delve into the intricacies of blanking dies, exploring their functions, types, and the crucial role they play in modern industry.
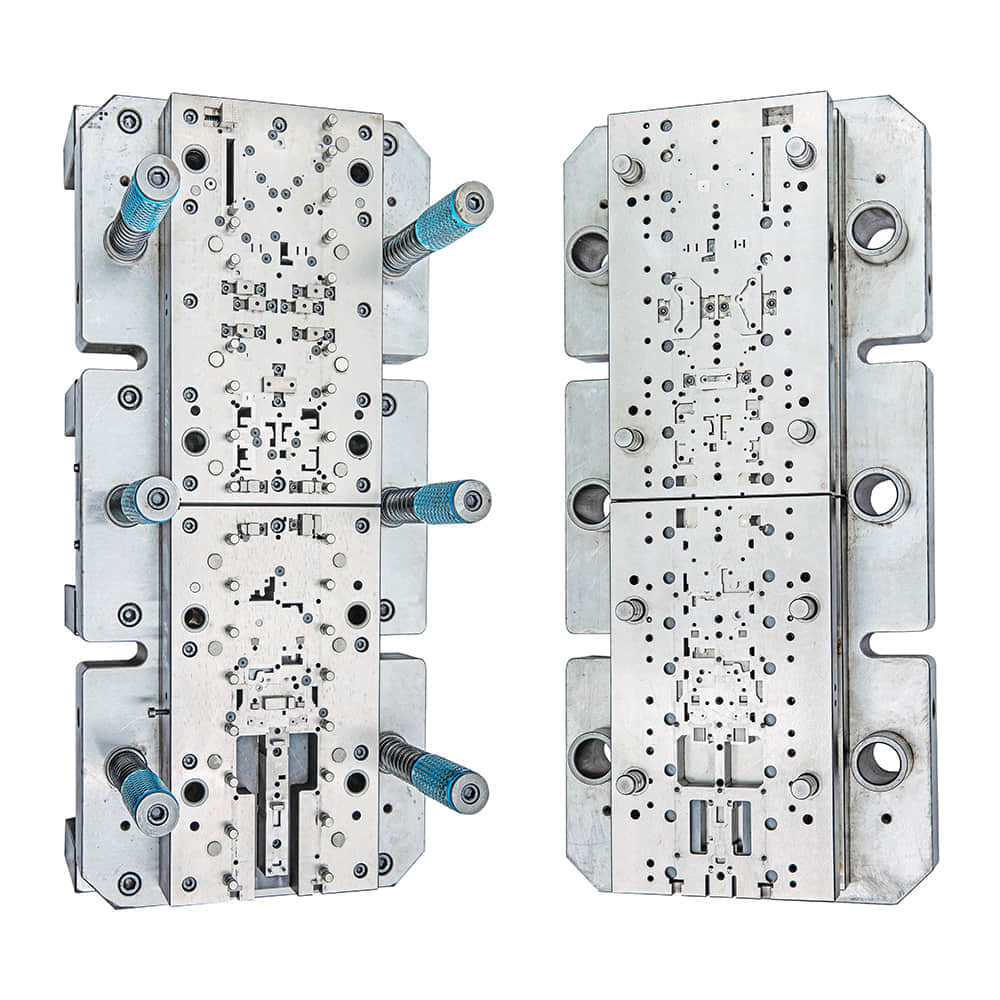
What Are Blanking Dies?
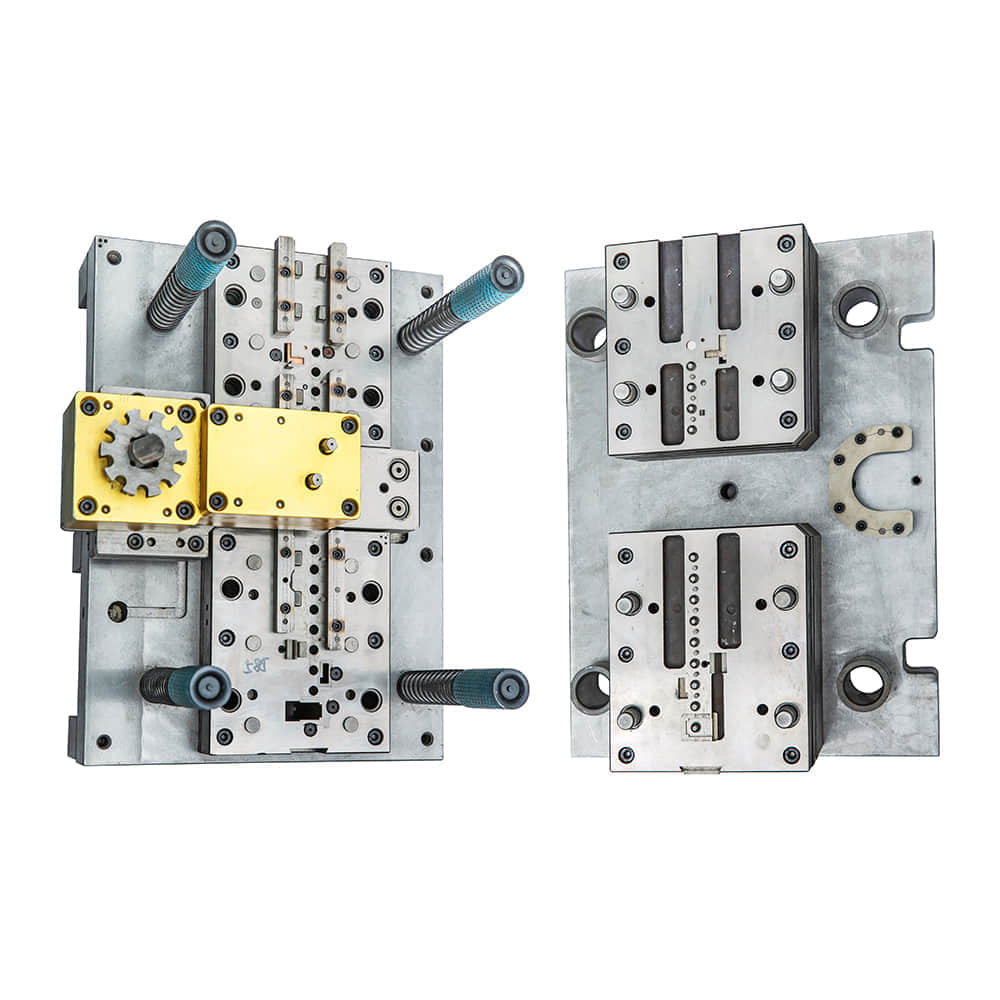
Blanking dies are specialized cutting tools used in manufacturing processes to create precise shapes or blanks from flat metal sheets. These blanks often serve as the basis for further processing, such as stamping, bending, or assembly in the production of various products, from automotive parts to electronic components. Blanking dies utilize mechanical force to cleanly cut the desired shape from the raw material, leaving behind the blank while removing the excess material, known as the scrap. The Function of Blanking Dies The primary function of blanking dies is to ensure accuracy and consistency in material cutting. This precision is crucial for the successful production of components that require tight tolerances. Blank shapes produced by these dies are used in various industries, including automotive, aerospace, and electronics, where even the slightest deviation can result in product defects or failure. Types of Blanking Dies There are several types of blanking dies, each designed for specific applications and materials. The most common types include: Pierce and Blanking Dies:These dies are used to create holes or cutouts in the blank simultaneously. They are commonly employed in the automotive industry for producing parts like car body panels. Progressive Dies:Progressive blanking dies consist of a series of stations through which the material passes, with each station performing a specific cutting or forming operation. Progressive dies are highly efficient and are often used in high-volume manufacturing. Compound Dies:Compound dies are versatile and capable of performing multiple operations, such as blanking, bending, and forming, in a single die set. They are ideal for producing complex parts. Blanking and Piercing Dies:These dies are designed to separate the blank from the scrap material and create holes or openings within the blank. They are commonly used in the production of electrical components and sheet metal parts. Notching Dies:Notching dies are used to create V-shaped notches or grooves in blanks. They find applications in industries where interlocking parts are required. Materials Used in Blanking Dies Blanking dies are typically made from high-quality tool steels, such as D2, A2, or M2, which offer excellent hardness, wear resistance, and toughness. The choice of material depends on the specific application and the type of material being cut. The die’s durability and longevity are crucial factors in maintaining production efficiency. Design Considerations The design of a blanking die is a complex process that involves considerations for material thickness, blank shape, die clearance, and the tonnage required for the cutting operation. Skilled engineers and toolmakers work together to create dies that ensure consistent and accurate cuts, minimize waste, and maximize productivity. Challenges in Blanking Die Production Producing high-quality blanking dies requires advanced machining and heat treatment processes. Additionally, maintaining and sharpening these dies is essential to ensure they perform optimally throughout their lifespan. Any deviation or wear in the die can result in defective parts and increased production costs. Conclusion Blanking dies are indispensable tools in modern manufacturing, contributing to the production of countless products that we rely on in our daily lives. Their ability to cut materials with precision and consistency is a testament to the intricate engineering and craftsmanship behind their design and production. As technology continues to advance, we can expect further innovations in blanking die technology, enabling even more complex and precise manufacturing processes.
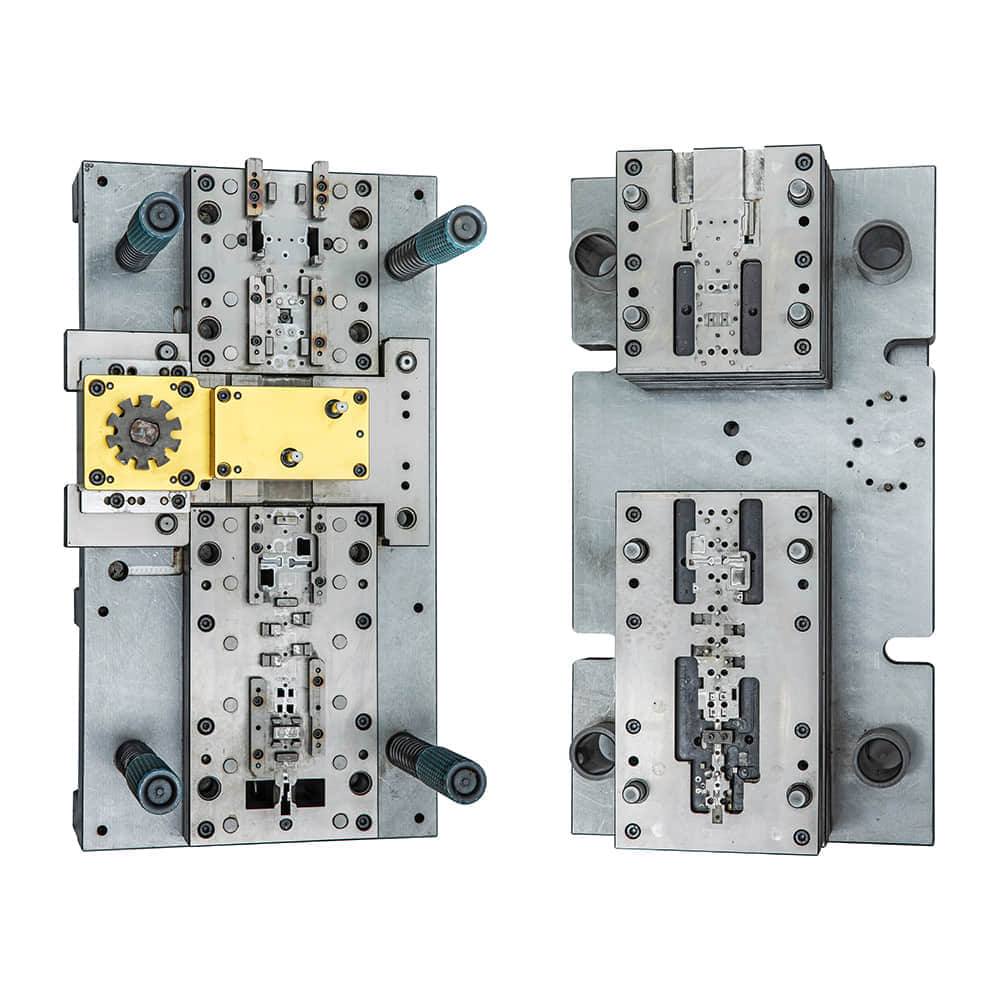