Electric actuators have emerged as a pivotal component in the landscape of automation and control systems. With the rapid advancement of technology, they have become increasingly prevalent across various industries, including manufacturing, robotics, HVAC, and even precision medicine. This article aims to delve into the fundamentals of electric actuators, their working principles, benefits, applications, and future prospects.
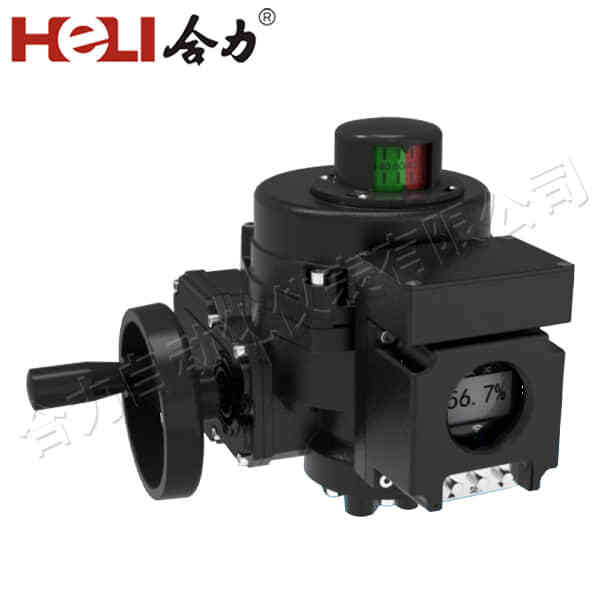
An electric actuator is a device that converts electrical energy into mechanical motion. The primary function of an electric actuator is to control the movement of a mechanism or system. This is achieved through the use of an electric motor, which drives the actuator to perform its assigned tasks, such as opening and closing valves, moving robotic arms, or adjusting positioning systems. The core components of an electric actuator include the motor, gearbox, and feedback systems, which ensure precise control and movement.
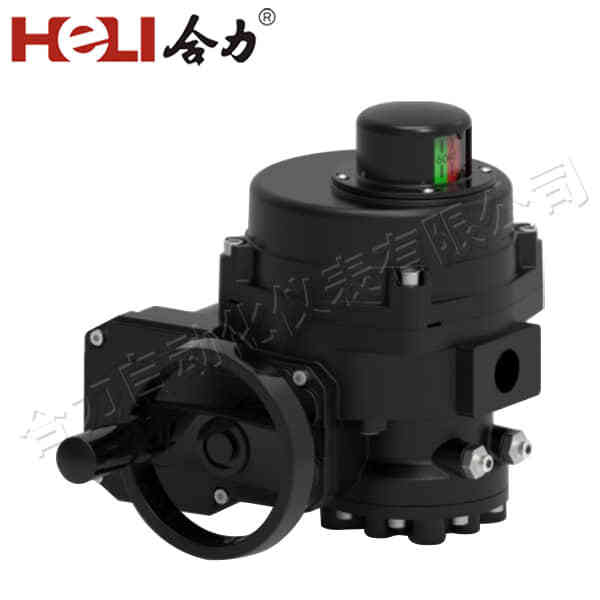
There are two main types of electric actuators: linear and rotary. Linear actuators produce straight-line motion, which is ideal for applications such as push-pull mechanisms or lifting devices. On the other hand, rotary actuators create rotational movement, suited for applications like turning valves or steering systems in vehicles. Each type has its unique designs and form factors, making them versatile for various implementation scenarios. One of the key advantages of electric actuators over traditional pneumatic or hydraulic actuators is their energy efficiency. They consume less power compared to their counterparts, leading to reduced operational costs. Electric actuators also offer faster response times, enabling rapid adjustments and enhancements in process control. This is particularly beneficial in industries that rely on real-time data processing and automation.
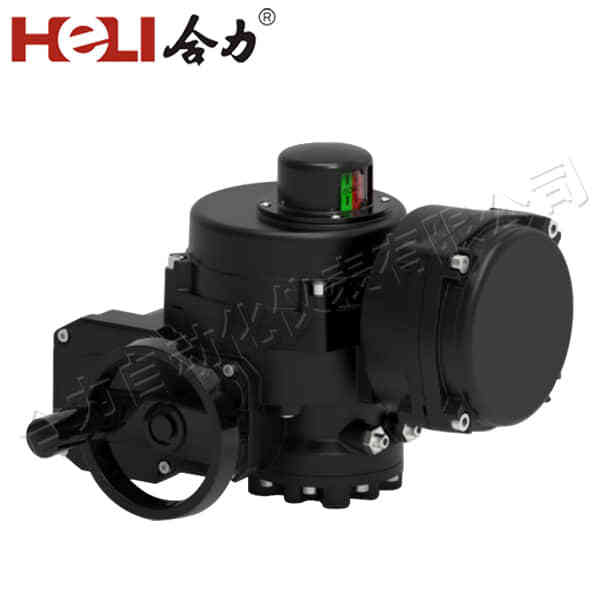