Electric ball valves are essential components in many industrial applications, offering efficient fluid control and automation. These valves combine the reliability of traditional ball valves with the precision of electric actuation, making them a popular choice in various sectors, including water treatment, HVAC systems, oil and gas, and manufacturing. This article delves into the construction, operation, advantages, applications, and maintenance of electric ball valves, highlighting their significance in contemporary engineering.
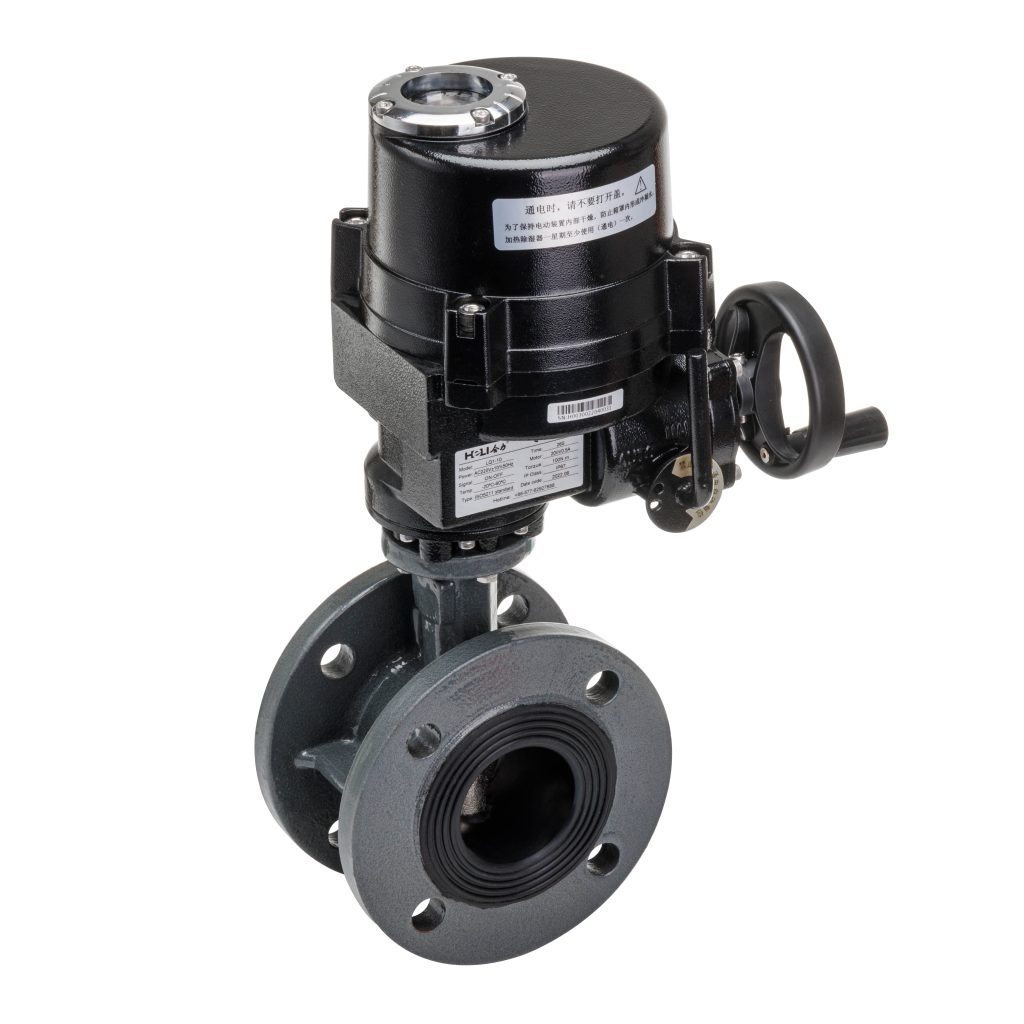
Construction of Electric Ball Valves
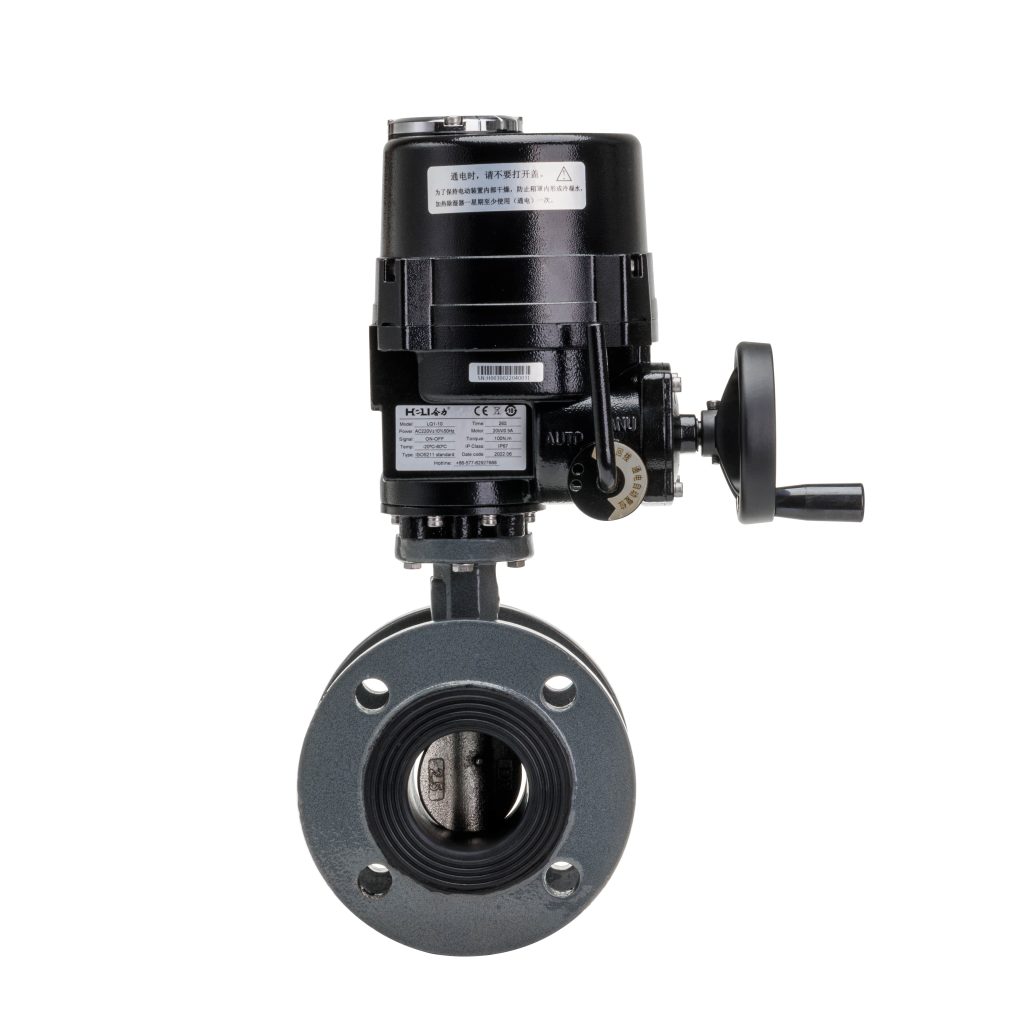
An electric ball valve consists of several key components: the valve body, the ball, the seat, the actuator, and the electrical controls. The valve body is typically made from durable materials such as stainless steel, brass, or PVC, ensuring resistance to corrosion and high pressures. The ball, which is the central element, has a spherical shape with a hole drilled through its center. This design allows for maximum flow when the valve is fully open and minimal resistance when closed. The electric actuator is responsible for opening and closing the valve. It contains an electric motor and a gearbox that translates the motor’s rotational movement into linear movement, turning the ball to the desired position. The actuator is often equipped with feedback sensors that provide real-time information on the valve’s position, enhancing the overall control system’s efficiency.
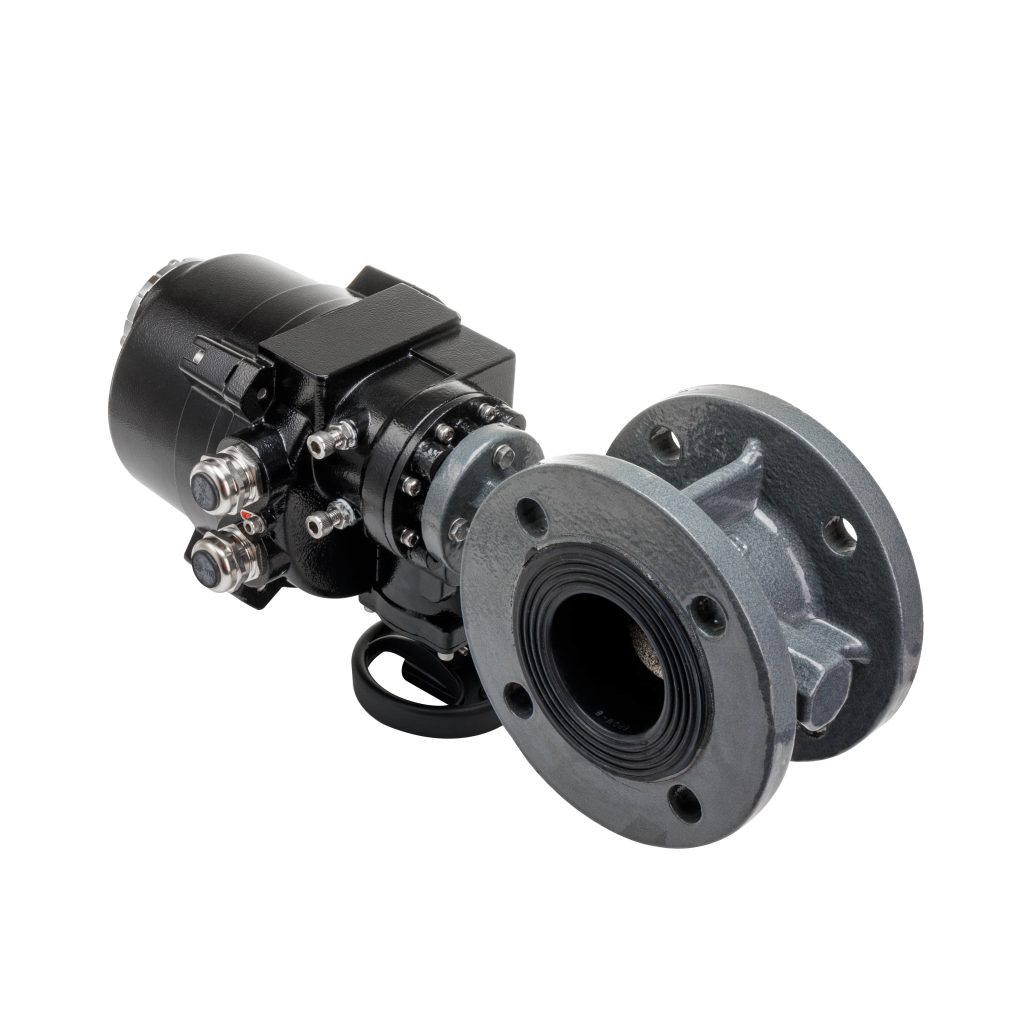