Injection molding is a widely used manufacturing process that has revolutionized the production of various parts and components across industries. This versatile technique involves the creation of intricate and precise parts by injecting molten material into a mold cavity. In this article, we will delve into the world of injection molded parts, exploring their applications, benefits, and the intricate process that brings them to life.
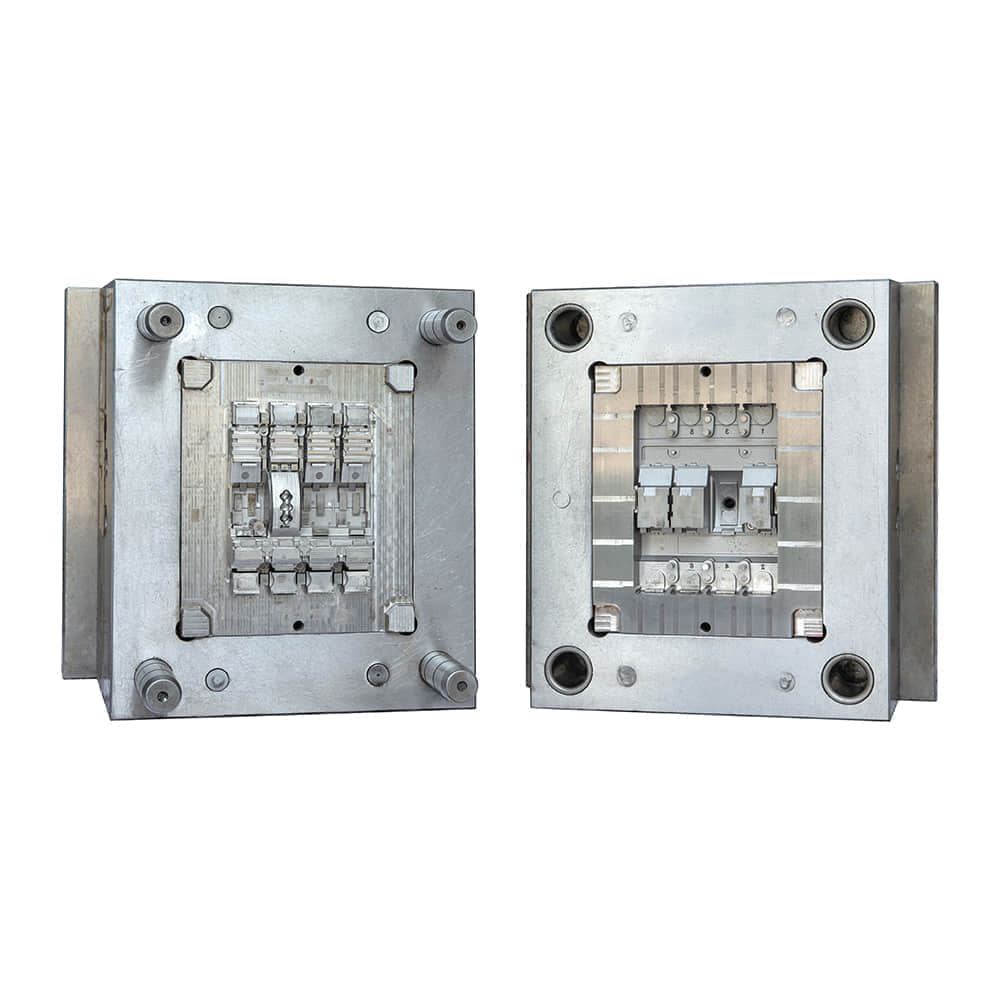
The Injection Molding Process
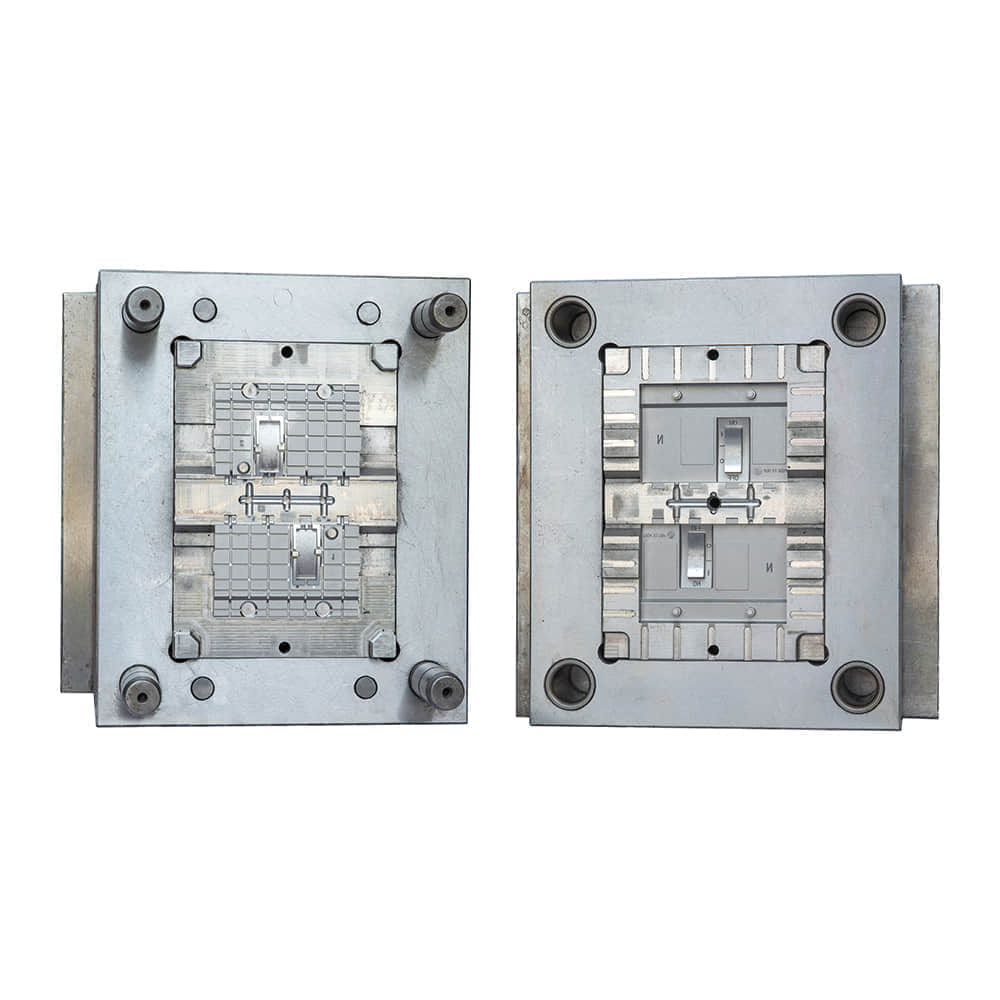
Injection molding is a highly controlled process that demands precision at every step. It begins with the selection of a suitable material, typically thermoplastics like ABS, polyethylene, or nylon. The chosen material is then melted to a specific temperature and injected into a mold cavity, which is the negative form of the desired part. Once the material cools and solidifies, the mold is opened, and the finished part is ejected. This process is remarkably efficient, producing large quantities of identical parts with minimal material waste. Applications of Injection Molded Parts The applications of injection molded parts span a multitude of industries, from automotive and aerospace to healthcare and consumer goods. Here are a few examples of how these parts are utilized: Automotive Industry: Injection molded parts are widely used in the automotive sector for interior and exterior components, such as dashboards, bumpers, and light covers. Their lightweight nature, durability, and ability to incorporate intricate designs make them ideal for enhancing vehicle performance and aesthetics. Medical Devices: Precision is paramount in the medical field, and injection molded parts are critical in the production of medical devices and equipment. Components like syringe barrels, IV connectors, and surgical instruments are often manufactured using this method, ensuring consistent quality and reliability. Electronics: Injection molding is employed in the electronics industry to create casings for various devices like smartphones, tablets, and remote controls. These casings not only protect the delicate electronics but also offer a sleek and uniform appearance. Consumer Products: Many everyday consumer products rely on injection molded parts, from toys and kitchen appliances to packaging materials. The ability to produce these items quickly and affordably while maintaining high precision is a testament to the versatility of injection molding. Advantages of Injection Molded Parts Injection molded parts offer several advantages that contribute to their widespread adoption: High Precision: Injection molding enables the production of complex and intricate parts with tight tolerances, ensuring consistency and accuracy in every piece. Cost-Efficiency: The ability to manufacture large quantities of parts in a short time reduces per-unit production costs, making injection molding a cost-effective option. Material Variety: Injection molding accommodates a wide range of materials, allowing manufacturers to choose the best-suited material for their specific application. Minimal Waste: The process generates minimal material waste since excess material can be recycled, reducing environmental impact. Quick Turnaround: Injection molding machines can produce parts rapidly, meeting tight production schedules and market demands. Challenges in Injection Molding While injection molding offers numerous advantages, it also presents some challenges, such as: Tooling Costs: Creating molds for injection molding can be expensive, particularly for complex parts, but the long-term cost savings often outweigh the initial investment. Design Constraints: Parts must be designed with injection molding in mind, taking into account factors like draft angles and material flow to ensure successful production. Material Selection: Choosing the right material is crucial for achieving the desired properties and performance of the final part. In conclusion, injection molded parts are integral to numerous industries, offering a combination of precision, efficiency, and versatility that few other manufacturing processes can match. From the automotive and medical sectors to electronics and consumer goods, injection molding continues to drive innovation and quality across a wide range of applications, making our daily lives safer and more convenient.
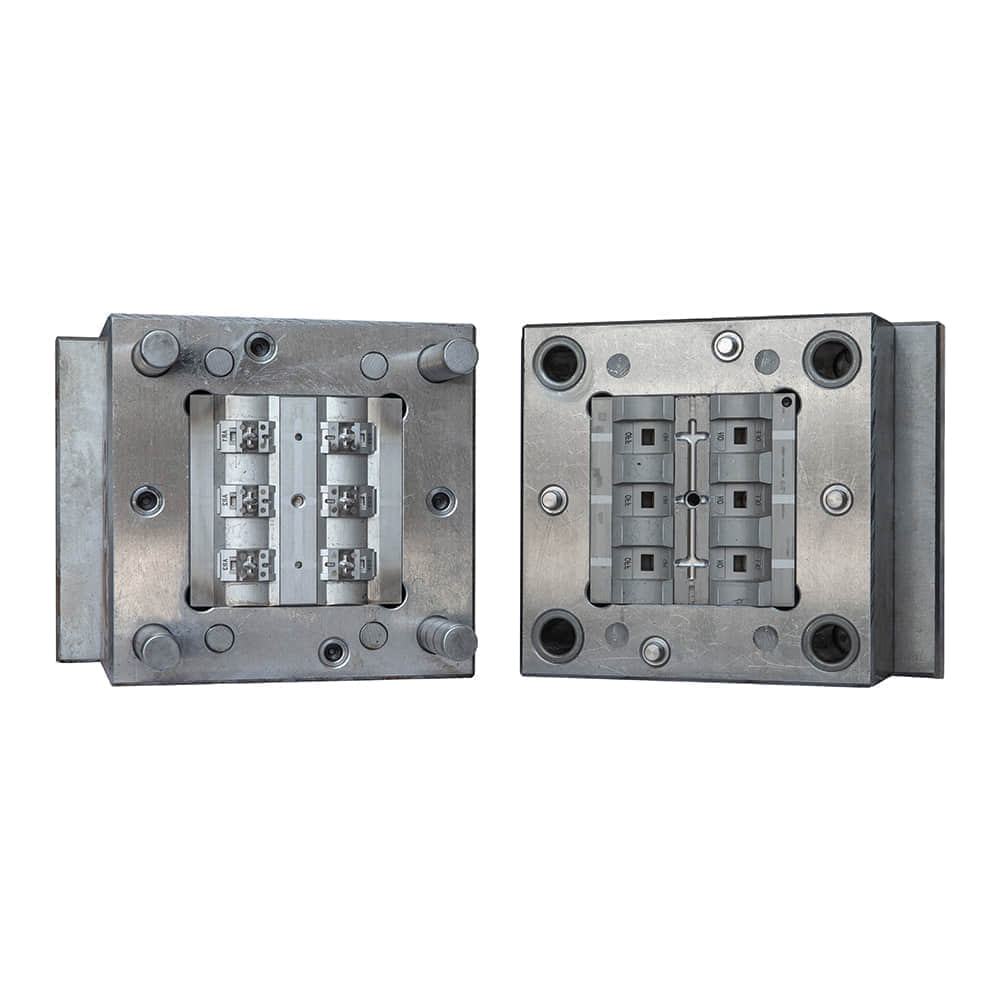