Blanking dies are an indispensable component in the world of manufacturing and metalworking. They play a crucial role in shaping various materials into desired forms, from intricate metal parts used in the automotive industry to simple yet essential components like electrical connectors. In this article, we will delve into the fascinating world of blanking dies, exploring their function, design considerations, and the crucial role they play in modern manufacturing.
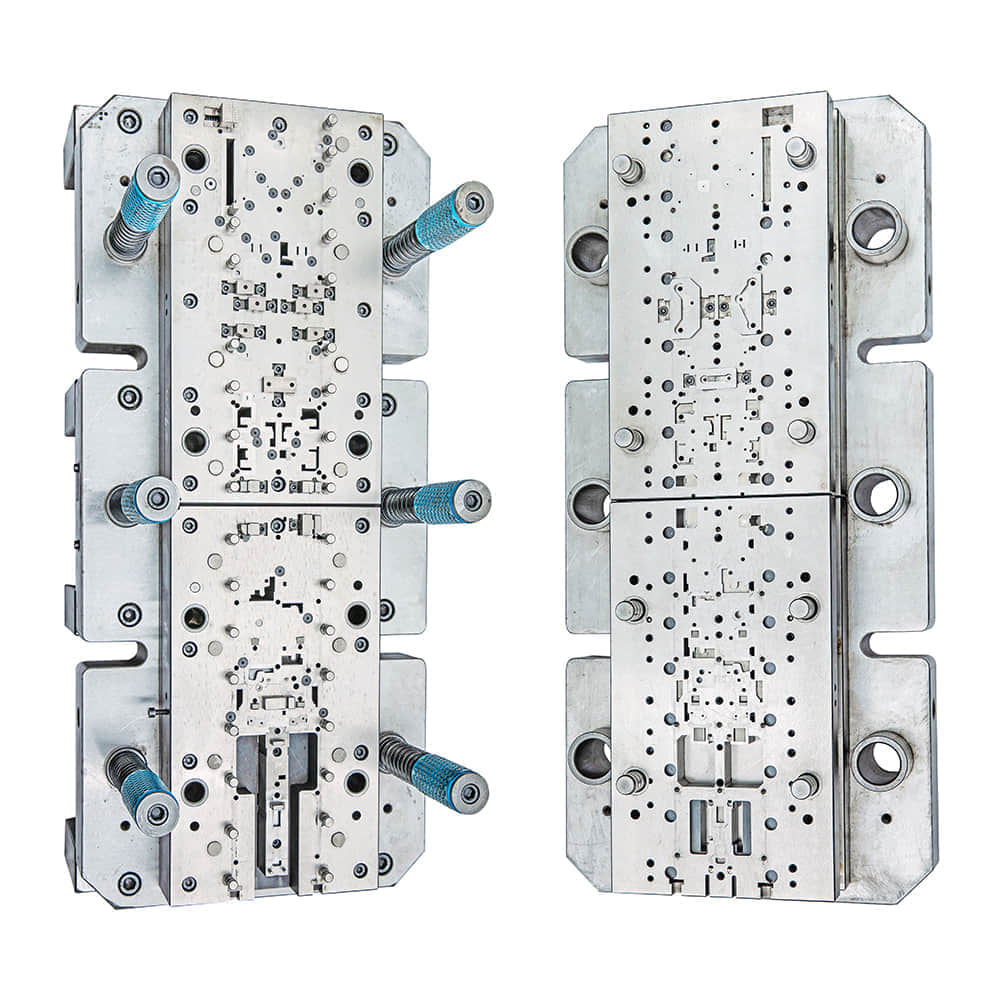
The Basics of Blanking Dies
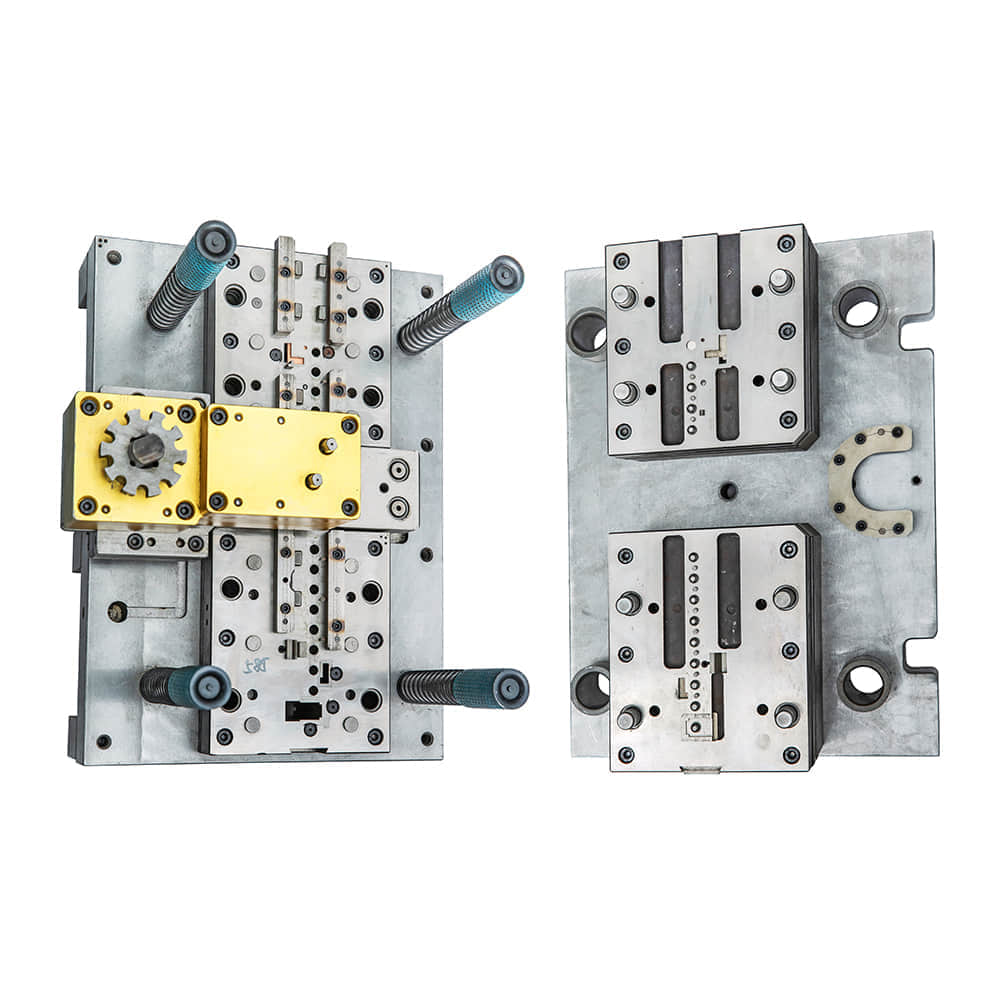
Blanking dies, often referred to simply as “blanks,” are specialized tools used to cut or shear sheet metal, plastic, or other materials into specific shapes. This process is known as blanking, and it is essential for producing precise components used in a wide range of industries. The primary purpose of a blanking die is to create parts with uniform dimensions and clean edges, meeting strict quality standards. Anatomy of a Blanking Die A blanking die consists of several key components, each playing a vital role in the cutting process: Die Block: This is the main body of the blanking die and provides structural support. It typically contains the cavity into which the material is inserted for cutting. Punch: The punch is the upper part of the die that descends to cut or shear the material. It’s designed to match the desired shape of the finished part. Stripper Plate: This component helps remove the cut material from the punch after each stroke, ensuring that the newly cut blank doesn’t stick to the punch. Pilots and Bushings: These guide pins and bushings ensure accurate alignment between the punch and die, allowing for precise and repeatable cutting. Die Shoe: The die shoe provides a stable platform for the die assembly and is often attached to the press or machine used for blanking. The Blanking Process The blanking process involves several steps: Material Feeding: Sheets of material are fed into the blanking machine, where they are aligned with the die. Cutting: The punch descends into the die, cutting out the desired shape. This process is precise and rapid, thanks to the careful design of the die and the power of the press. Stripping: After each stroke, the stripper plate lifts the newly cut blank away from the punch, preventing it from sticking. Ejection: Finally, the blank is ejected from the die for collection or further processing. Design Considerations The design of a blanking die is a complex process that requires careful consideration of several factors: Material: Different materials require different die materials and configurations. Harder materials may necessitate more robust dies. Tolerance: The required tolerance for the finished parts is a crucial factor in die design. High-precision parts demand highly accurate dies. Production Volume: The expected production volume influences the design. High-volume production may require automated or progressive dies for efficiency. Material Thickness: The thickness of the material being cut affects the design of the die and the power of the press required. Challenges in Blanking While blanking dies are incredibly versatile and precise, they are not without challenges. Some common issues include: Die Wear: Over time, the repeated cutting action can cause wear and tear on the die, leading to a decrease in the quality of cut parts. Material Fracture: Certain materials, especially brittle ones, can fracture during the blanking process, leading to defects in the finished parts. Maintenance: Regular maintenance is essential to ensure the die functions correctly and produces high-quality parts consistently. Conclusion Blanking dies are the unsung heroes of modern manufacturing, responsible for producing countless components that drive our industries forward. Their intricate design and precise operation are a testament to the art and science of metalworking. Understanding the basics of blanking dies sheds light on the complexity behind the seemingly simple task of cutting materials into shape, reminding us of the precision and skill that underpin our modern world.
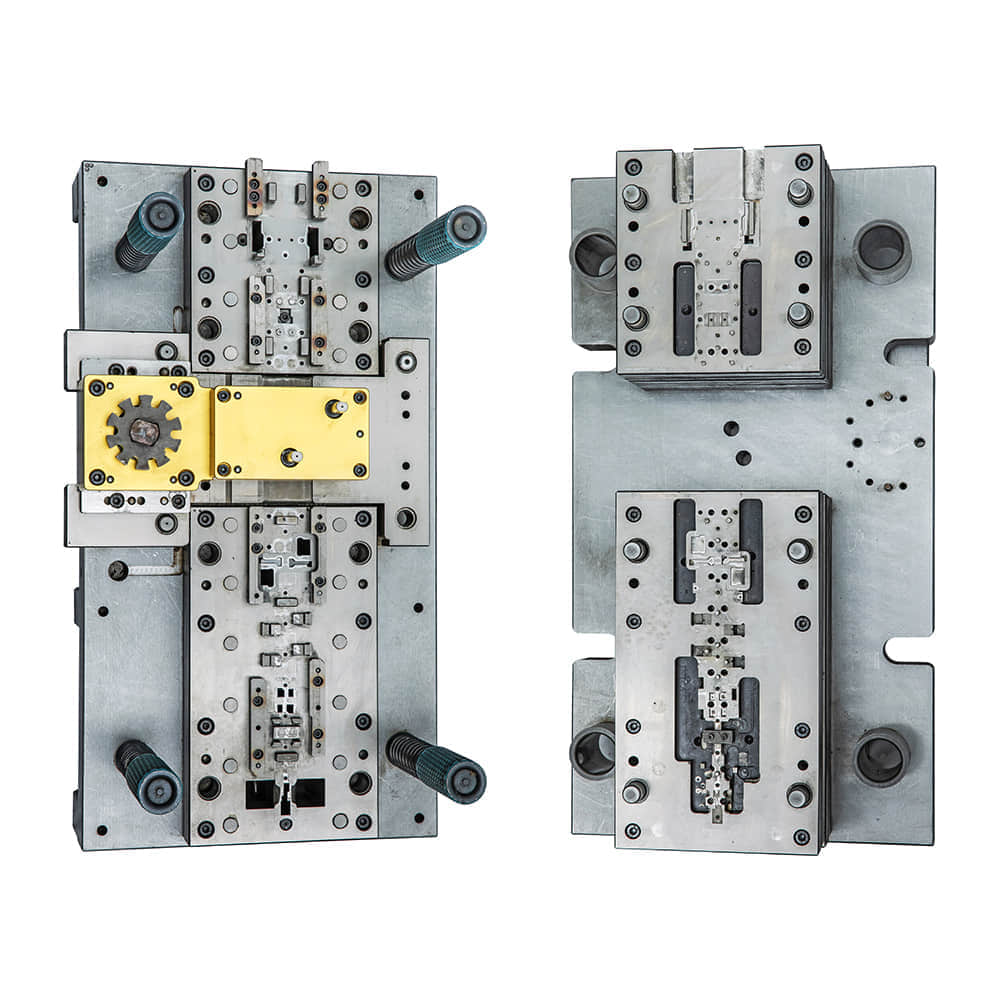