Metal Stamping Dies: Precision in Forming
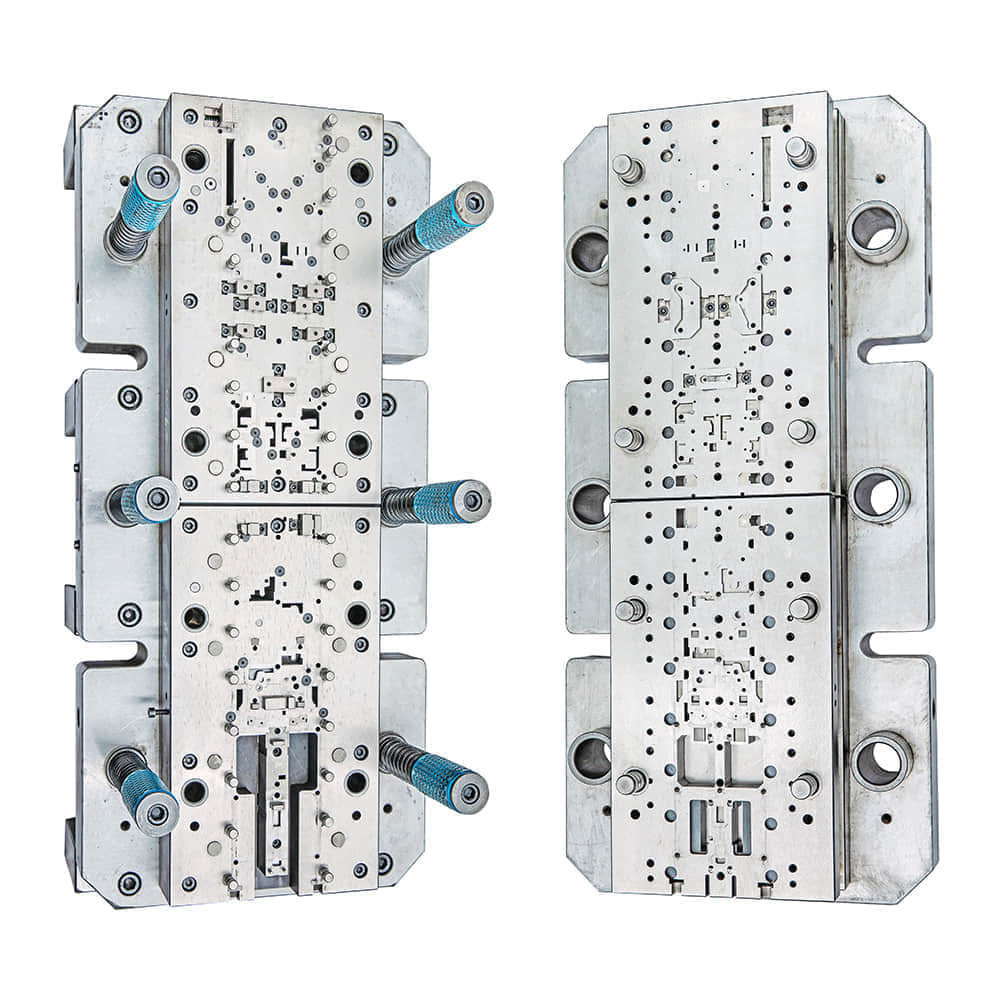
Metal stamping is a manufacturing process that has been a cornerstone of the industrial world for centuries. It involves shaping and cutting metal sheets into desired forms using specialized tools known as metal stamping dies. In this article, we will delve into the world of metal stamping dies, exploring their importance, types, and the intricate artistry that goes into creating them.
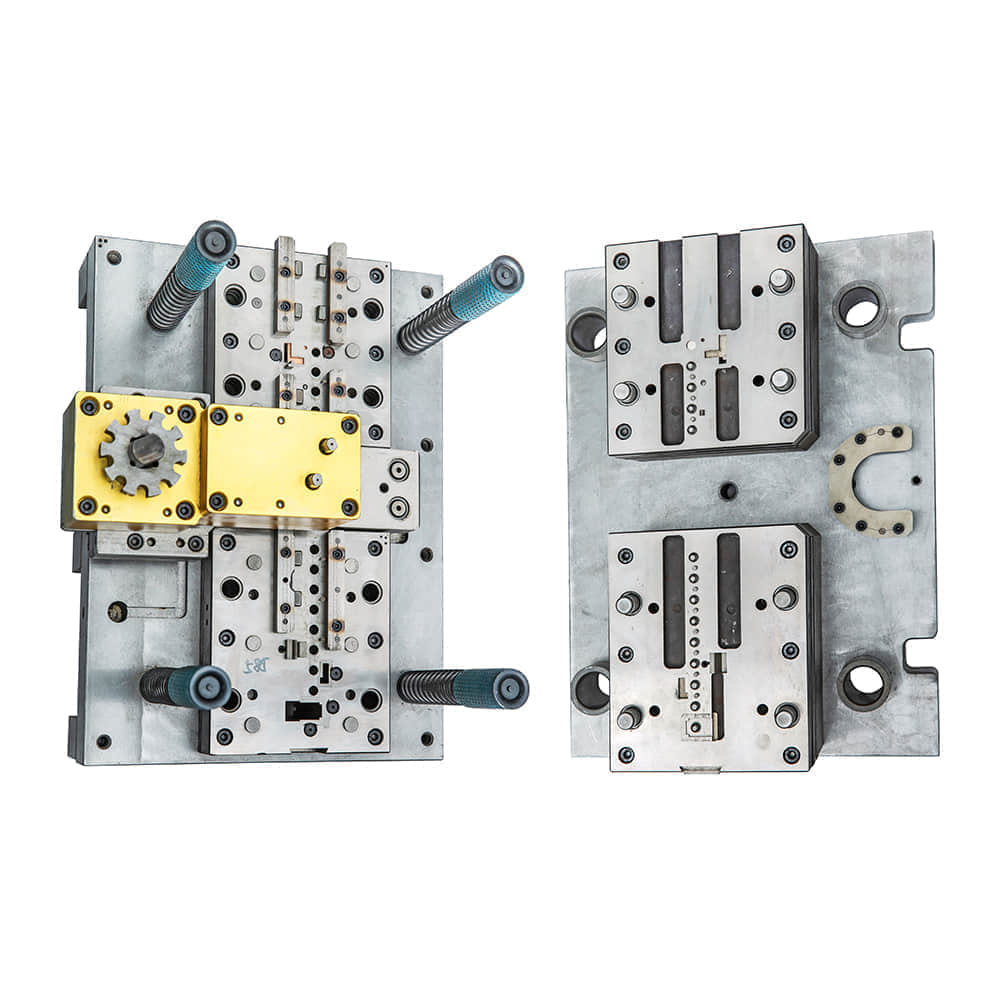
The Significance of Metal Stamping Dies Metal stamping dies are fundamental to various industries, including automotive, aerospace, electronics, and consumer goods. These dies enable the mass production of consistent and intricate metal parts with high precision and efficiency. Whether it’s producing car body panels, electronic components, or intricate jewelry, metal stamping dies play a pivotal role in shaping our modern world. Types of Metal Stamping Dies Blanking Dies: These dies are primarily used to cut flat pieces, or blanks, from a metal sheet. Blank pieces are often used as a starting point for further shaping or assembly. Piercing Dies: Piercing dies create holes or openings in metal sheets. They are commonly used in applications like making washers, gaskets, or perforated components. Forming Dies: Forming dies shape metal sheets into three-dimensional forms. They can range from simple bends to highly complex shapes, depending on the die design. Progressive Dies: Progressive dies are used for multiple operations in a single press. They can perform blanking, piercing, and forming in a sequence, making them highly efficient for high-volume production. Compound Dies: Compound dies combine two or more die types into a single tool. They are versatile and suitable for various operations, saving time and resources. The Artistry of Die Making Creating metal stamping dies is a meticulous craft that requires both engineering expertise and artistic finesse. Here’s a glimpse into the process: Design and Engineering: The process starts with meticulous design and engineering. Engineers use specialized software to create precise 3D models of the die, considering material properties, tolerances, and production volumes. Material Selection: Choosing the right material for the die is crucial. High-quality tool steels are commonly used due to their durability and ability to withstand high stress and wear. Machining: The die design is then translated into reality through CNC machining. Precision is paramount at this stage, as any deviation can affect the final product’s quality. Heat Treatment: To enhance the die’s hardness and durability, heat treatment is applied. This involves heating the die to a specific temperature and then cooling it rapidly. Assembly: Various components of the die, such as punches, inserts, and guide pins, are meticulously assembled. Testing and Fine-Tuning: Before the die goes into production, it undergoes rigorous testing to ensure it meets the desired specifications. Adjustments and fine-tuning may be necessary. Production: Once the die is approved, it is ready for mass production. The stamping process begins, and the die can produce thousands, if not millions, of identical metal components. Conclusion Metal stamping dies are the unsung heroes of modern manufacturing. They enable the creation of precise, complex, and consistent metal parts that are essential in numerous industries. The artistry behind the creation of these dies is a testament to human ingenuity and engineering excellence. As technology continues to advance, so too will the sophistication and capabilities of metal stamping dies, driving innovation and progress across various sectors.
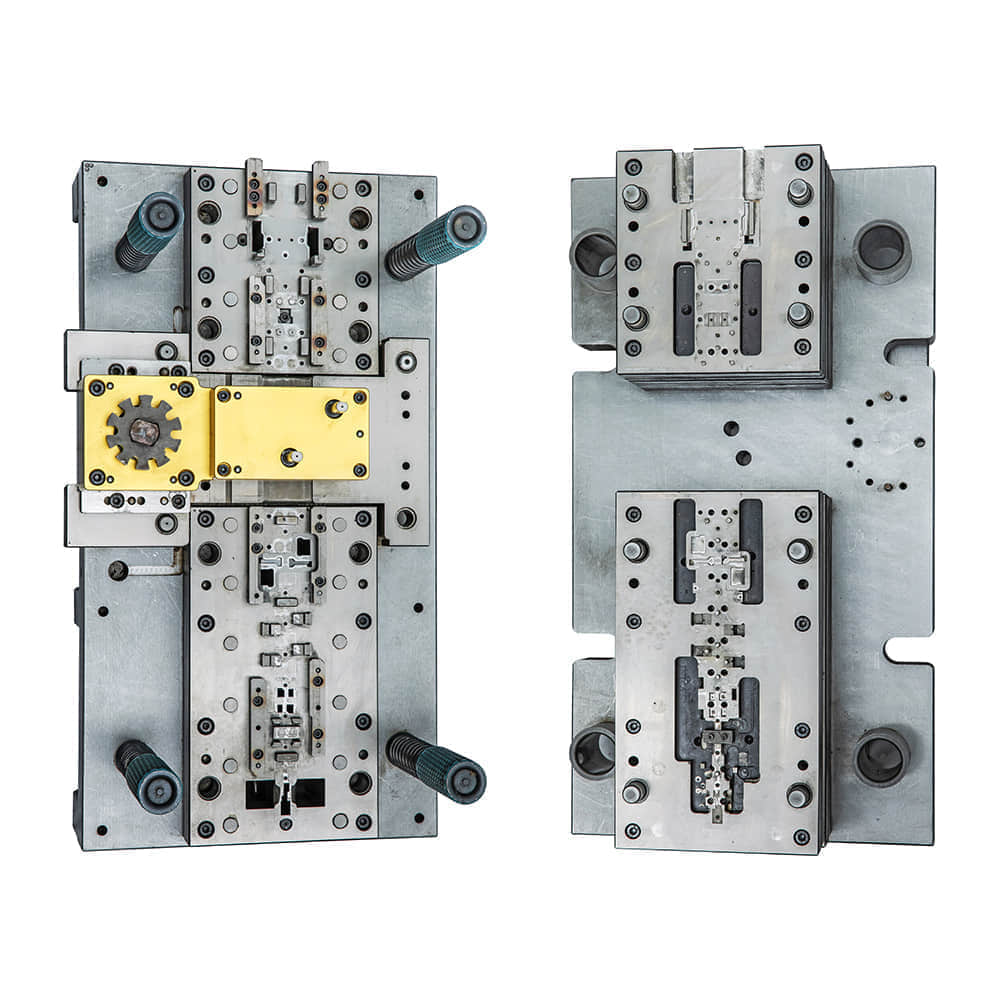