Thermosetting Compression Moulding: A Comprehensive Overview
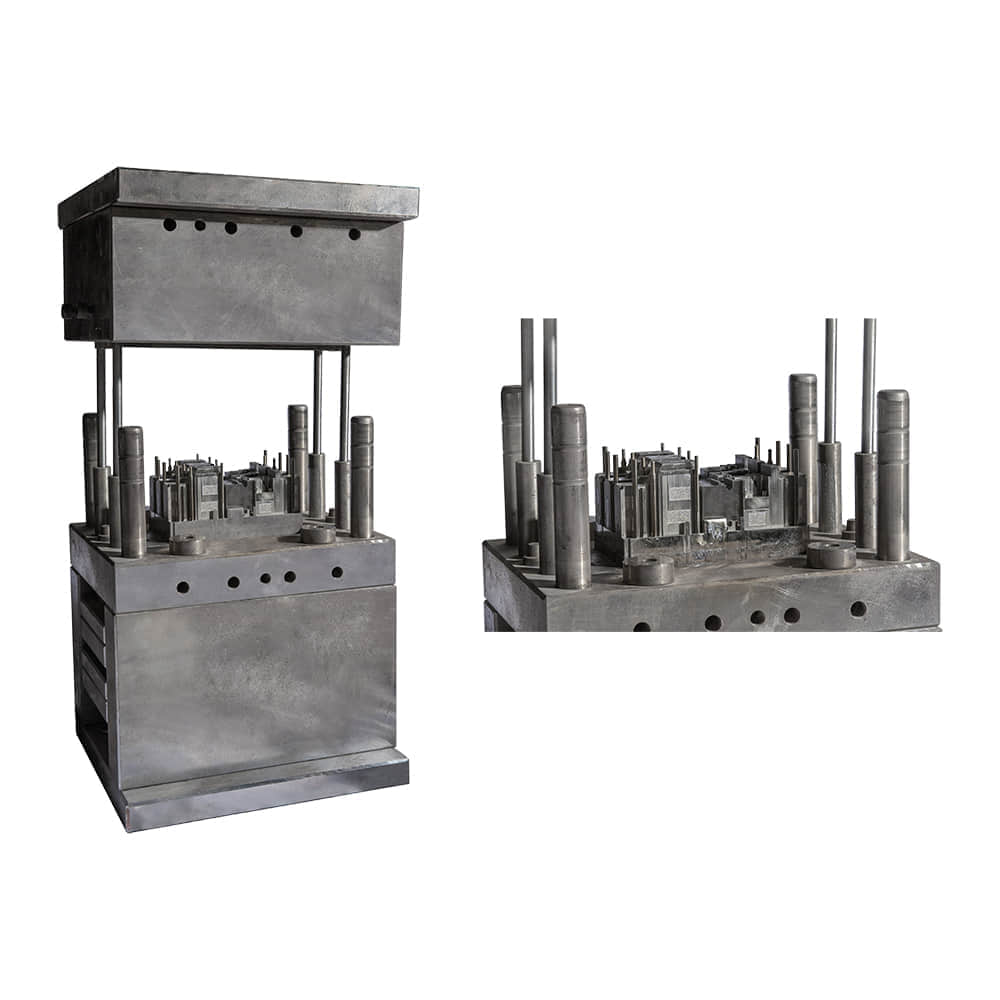
Introduction
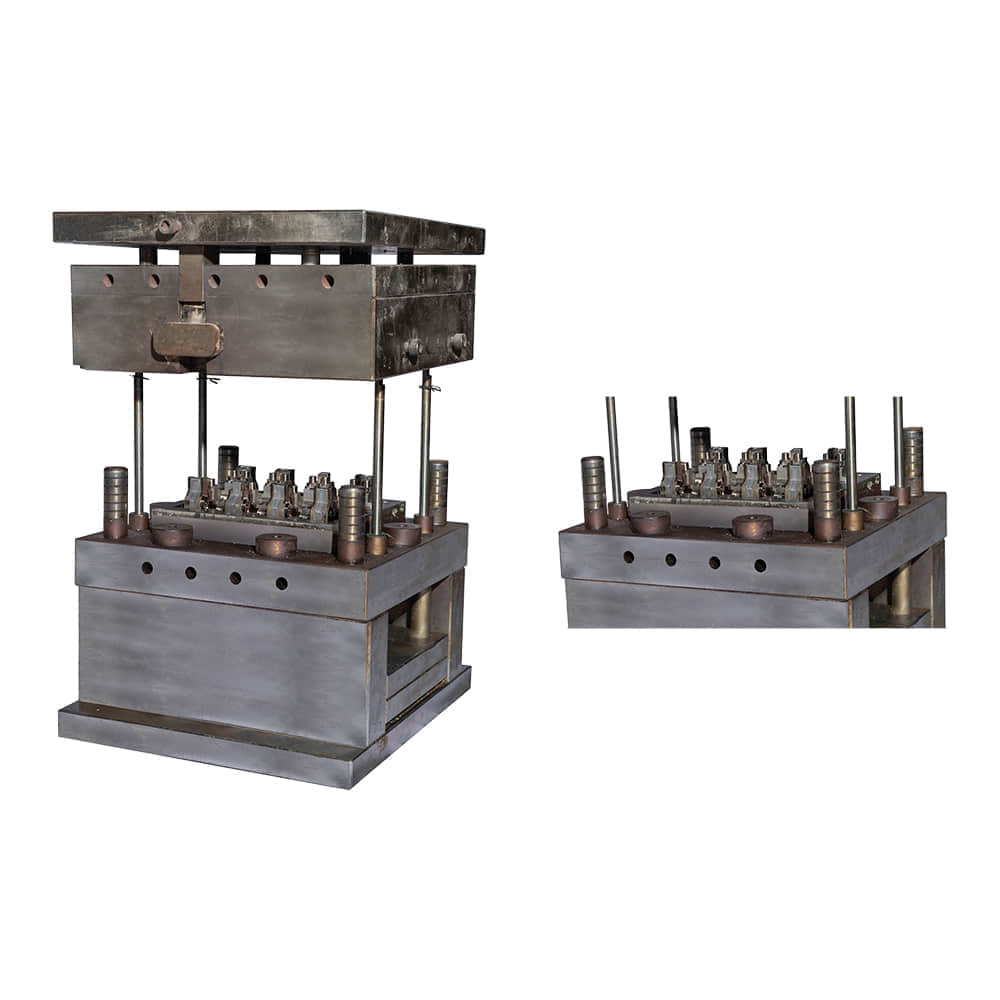
Thermosetting compression moulding is a widely used manufacturing process that plays a pivotal role in shaping various composite materials and thermosetting plastics into intricate and durable products. This article explores the fundamentals of thermosetting compression moulding, its applications, advantages, and some key considerations in the process. The Basics of Thermosetting Compression Moulding Thermosetting compression moulding is a manufacturing method that involves the transformation of thermosetting materials into desired shapes using heat and pressure. Unlike thermoplastic materials, which can be melted and reshaped multiple times, thermosetting materials undergo a chemical change during the moulding process. This irreversible transformation results in a final product that is highly durable and resistant to heat and chemicals. The Process Material Preparation: The process begins with the preparation of thermosetting materials, such as epoxy, phenolic, or melamine resins, in the form of granules, powders, or pre-impregnated sheets. Loading the Mould: The prepared material is placed into a mould cavity, which is often made of metal, with a specific design to produce the desired product shape. Applying Heat and Pressure: The mould is closed, and heat and pressure are applied simultaneously. The combination of heat and pressure causes the thermosetting material to flow and fill the mould cavity. Curing: During the heating phase, the thermosetting resin undergoes a chemical reaction known as cross-linking, resulting in a rigid and stable structure. This stage is called curing and typically occurs at temperatures ranging from 100°C to 200°C. Cooling and Ejection: After curing, the mould is cooled to solidify the part. Once cooled, the final product is ejected from the mould. Applications Thermosetting compression moulding finds application in various industries, including automotive, aerospace, electronics, and consumer goods. Some common products manufactured using this process include: Circuit boards and electronic components: The excellent electrical insulation properties of thermosetting plastics make them ideal for electronic applications. Composite materials: Thermosetting compression moulding is often used to produce composite parts for the aerospace and automotive industries due to its high strength and stiffness. Kitchenware: Melamine resins are used to create durable and heat-resistant kitchenware like plates, bowls, and utensils. Advantages of Thermosetting Compression Moulding Durability: Products produced through this process are highly durable and exhibit excellent resistance to heat, chemicals, and mechanical stress. Dimensional Stability: Thermosetting compression moulding offers tight tolerance control, ensuring precise and consistent part dimensions. High-Strength Parts: The cross-linking of thermosetting materials during curing results in high-strength parts with excellent mechanical properties. Cost-Effective: Once the mould is created, the process can be highly efficient for mass production, making it cost-effective for large-scale manufacturing. Considerations While thermosetting compression moulding offers numerous advantages, there are some key considerations: Mould Design: Proper mould design is critical to achieving the desired product shape and maintaining uniform pressure and temperature distribution. Material Selection: Choosing the right thermosetting material for the intended application is crucial for achieving the desired properties. Curing Time and Temperature: Precise control of curing time and temperature is necessary to avoid defects in the final product. Conclusion Thermosetting compression moulding is a versatile manufacturing process with applications spanning various industries. Its ability to produce durable, high-strength, and heat-resistant products makes it a preferred choice for many applications. Understanding the fundamentals of this process, its advantages, and the critical considerations involved is essential for successful thermosetting compression moulding operations.
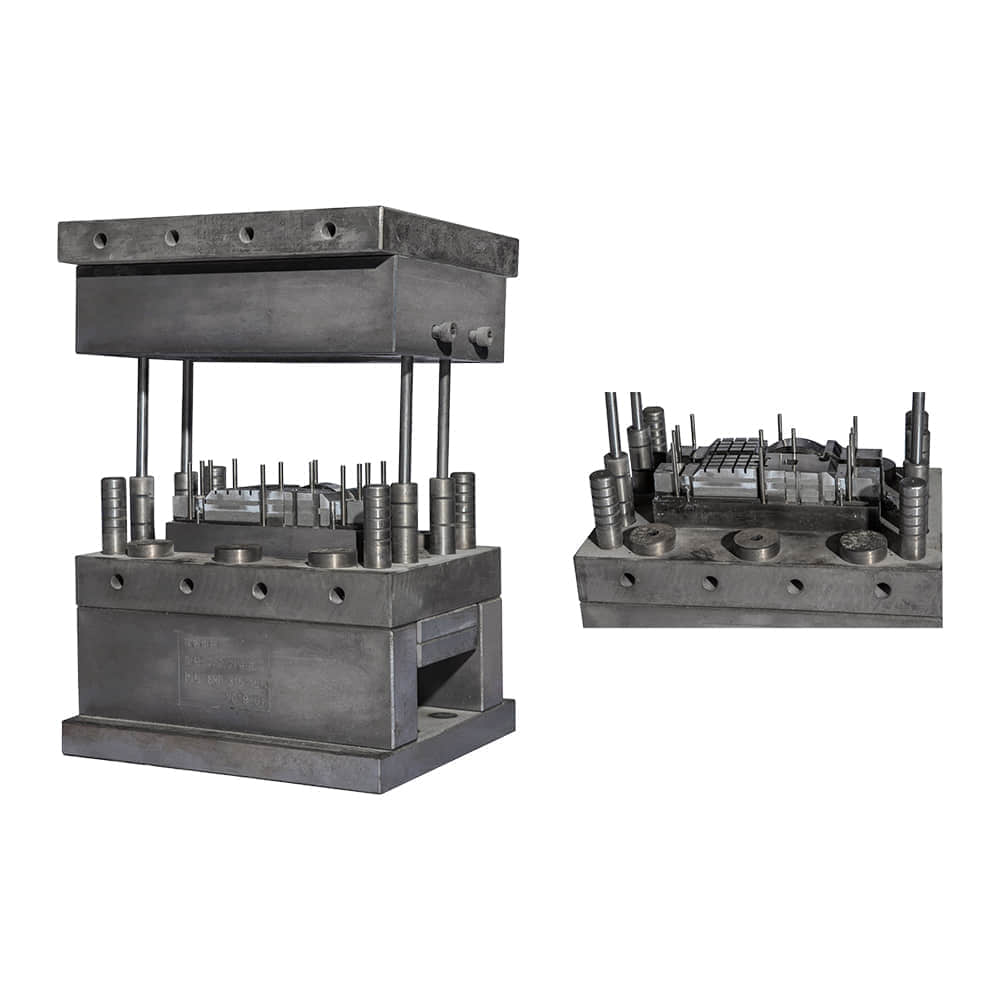