Thermosetting compression moulding is a vital manufacturing process used to create a wide array of products from thermosetting materials. This technique is particularly significant in industries such as automotive, electronics, and consumer goods due to its ability to produce durable and heat-resistant components.
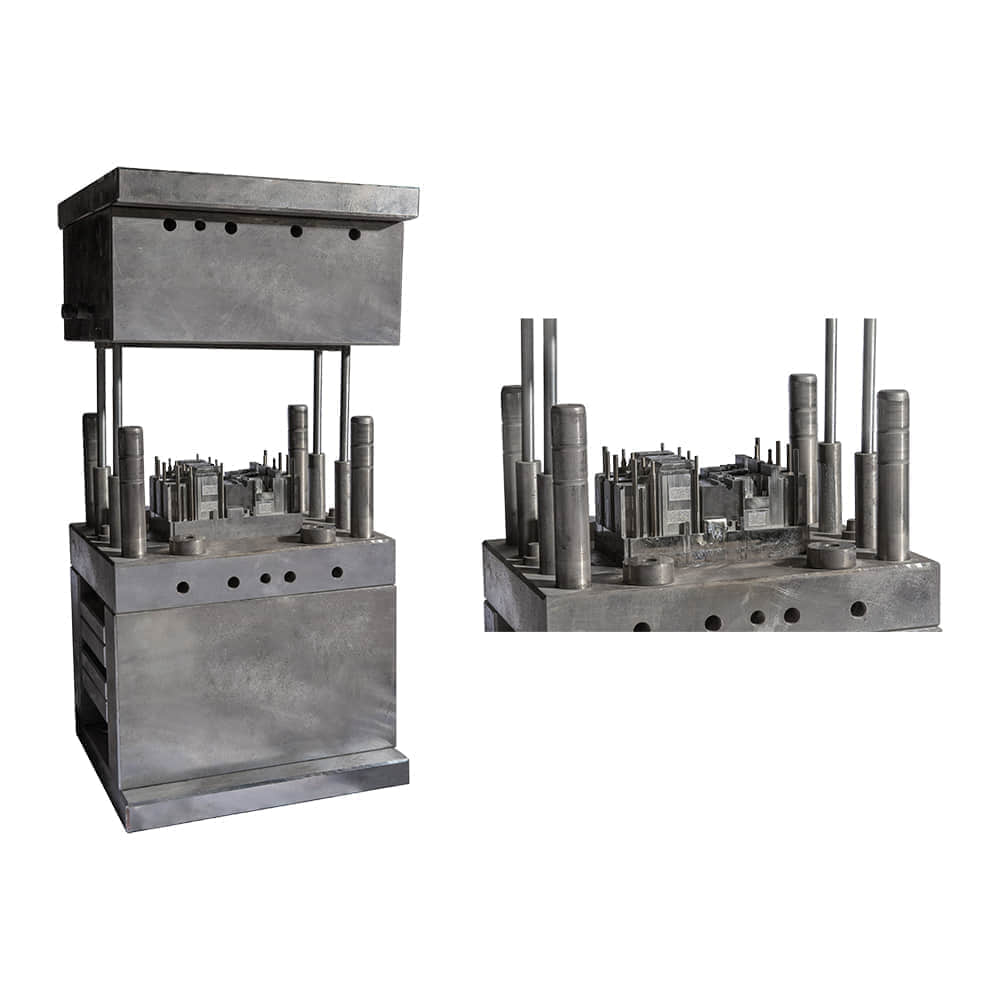
At its core, thermosetting compression moulding involves the shaping of thermosetting polymers—materials that, once cured, cannot be remolded or reshaped. The process begins with the introduction of a pre-measured quantity of thermosetting resin into a heated mould. The mould is then closed, and heat and pressure are applied. This combination causes the resin to flow and fill the mould cavity, undergoing a chemical reaction that transforms it into a solid, rigid form.
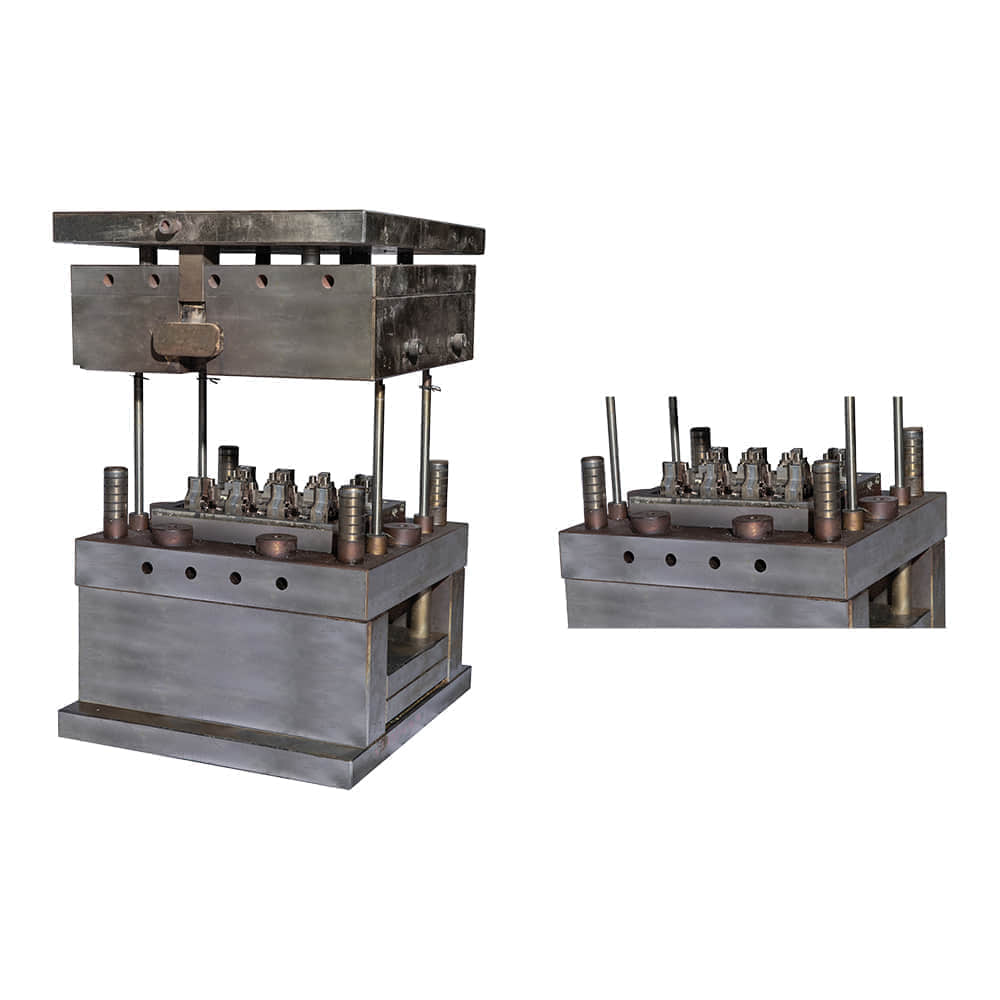
One of the key advantages of thermosetting compression moulding is its efficiency in producing complex shapes. The moulds can be designed to accommodate intricate features, allowing for a high degree of customization. Additionally, the process is highly repeatable, making it ideal for large production runs. Manufacturers can produce consistent parts with precise dimensions, ensuring quality control throughout the production cycle. The materials used in thermosetting compression moulding include epoxies, phenolics, and melamines, each offering unique properties suited for different applications. For instance, phenolic resins are renowned for their excellent thermal stability and electrical insulating properties, making them ideal for components in electrical applications. Epoxy resins, on the other hand, provide superior adhesion and chemical resistance, which is beneficial in automotive and aerospace applications.
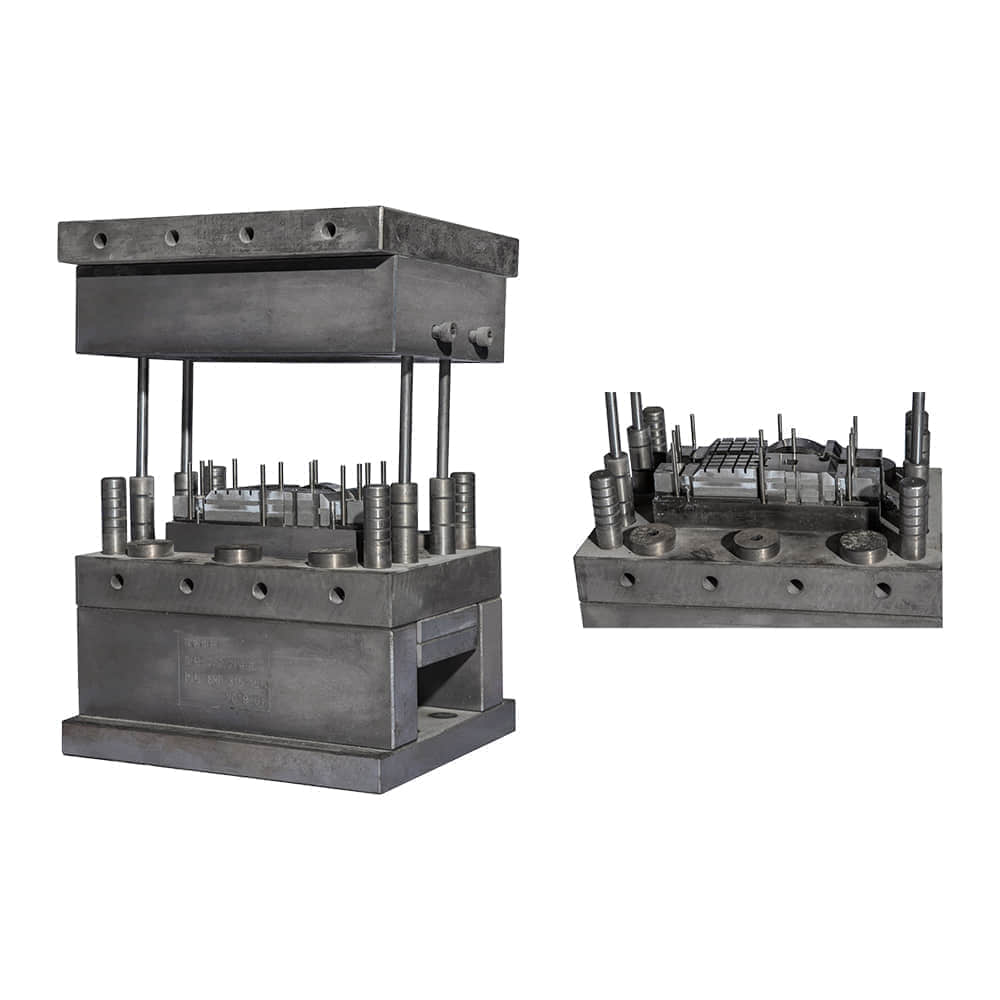