In the ever-evolving landscape of manufacturing and industry, technological advancements continue to reshape the way products are created and processes are optimized. Among these innovations, the rise of Direct Metal Casting (DMC) injection technology stands as a testament to human ingenuity and the relentless pursuit of excellence. This article delves into the intricacies of DMC injection, its applications, and the transformative impact it has on modern manufacturing.
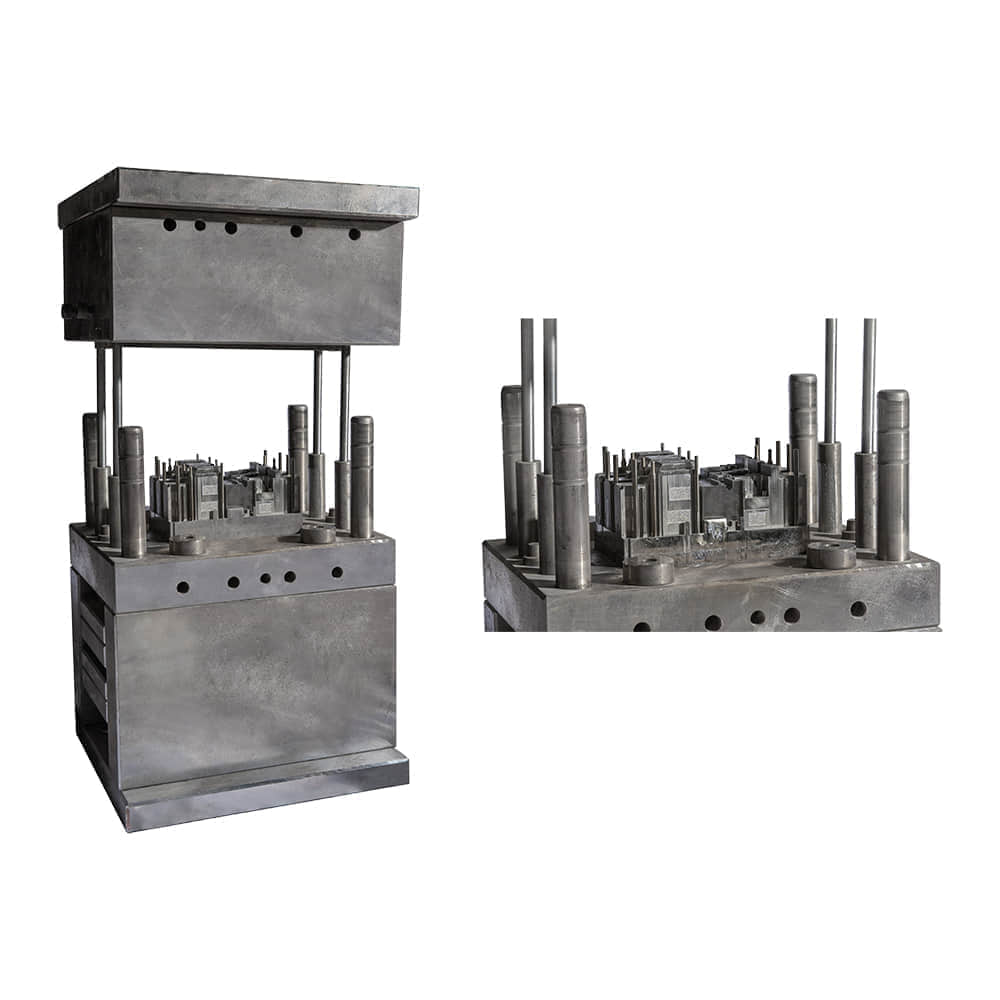
The Essence of DMC Injection
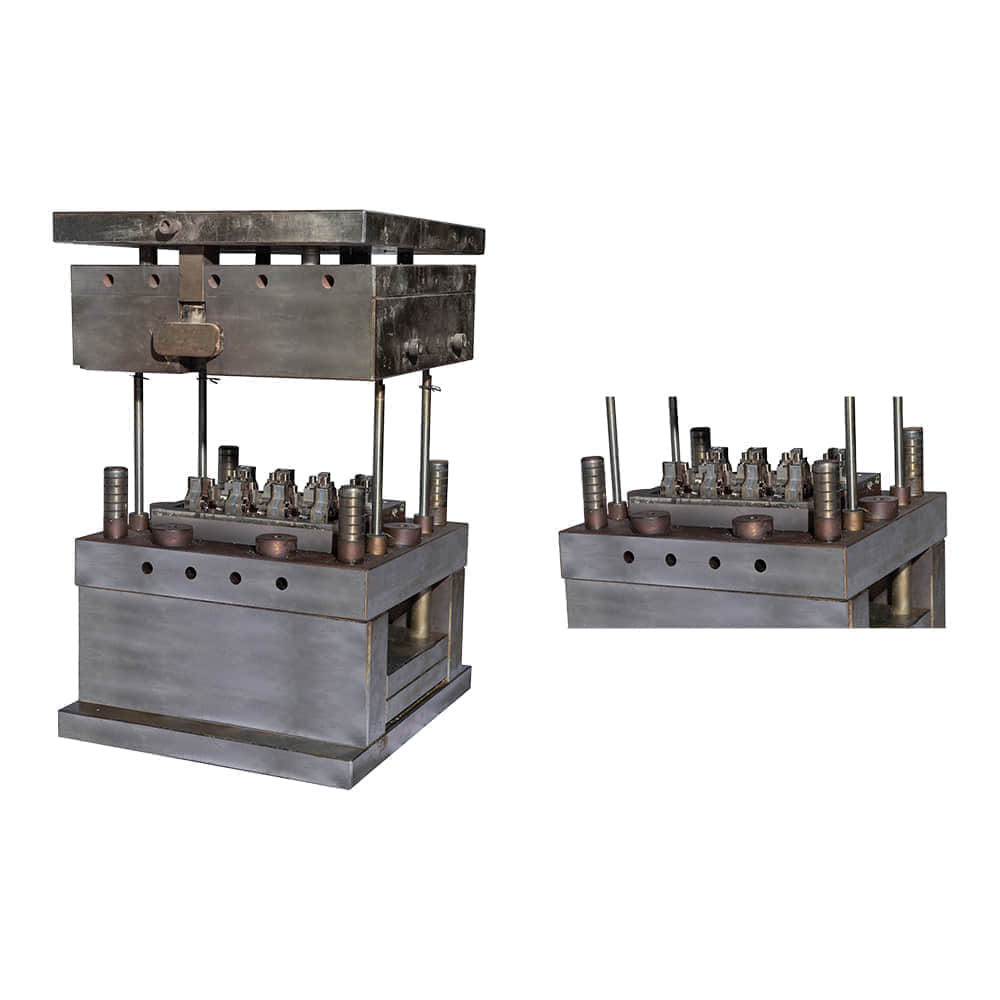
DMC injection is a cutting-edge additive manufacturing technique that harnesses the power of metal injection molding (MIM) and the precision of 3D printing. This fusion enables the creation of complex metal parts with unparalleled accuracy and efficiency. The process begins with the formulation of metal powders, which are combined with a binder material to create a feedstock. This mixture is then injected into a mold cavity with extreme precision. Precision Perfected One of the defining features of DMC injection is its ability to produce intricate and delicate designs with minimal limitations. Traditional manufacturing techniques often struggle with intricate geometries, but DMC injection thrives in this realm. The injection molding process allows for the creation of highly detailed structures, pushing the boundaries of what was once considered possible. Applications Across Industries The applications of DMC injection are as diverse as the industries it serves. In aerospace, this technology is used to craft lightweight yet robust components that contribute to fuel efficiency and performance. The medical field benefits from DMC injection through the production of intricate surgical instruments and implants tailored to individual patients. The automotive sector embraces this innovation to create complex engine parts that enhance overall functionality. Essentially, DMC injection finds its place wherever precision and durability are paramount. Advantages Unveiled The advantages of DMC injection extend beyond its impeccable precision. The combination of additive manufacturing and injection molding results in reduced material waste compared to traditional subtractive manufacturing. This translates to cost savings and a more sustainable production process. Furthermore, the speed at which DMC injection can produce parts is remarkable, facilitating rapid prototyping and accelerated product development cycles. Challenges and Future Prospects As with any technology, DMC injection is not without its challenges. Fine-tuning the parameters of the injection process and perfecting the feedstock composition require ongoing research and development. However, the promise that DMC injection holds for industries worldwide is too enticing to overlook. Researchers and engineers are working tirelessly to refine the technique, expand its material capabilities, and unlock its full potential. The Road Ahead The journey of DMC injection technology has been marked by remarkable advancements and continuous innovation. Its ability to merge the intricacy of 3D printing with the precision of injection molding sets a new standard in manufacturing excellence. As this technology matures, it will likely redefine the possibilities of what can be achieved across industries, bringing us closer to a future where complexity is no longer a limitation. In conclusion, DMC injection technology stands as a pinnacle of human achievement in the manufacturing realm. Its fusion of additive manufacturing and injection molding presents a promising path forward, redefining the boundaries of precision and complexity. As industries continue to harness its power, the transformative impact of DMC injection will be felt far and wide, reshaping the way we conceive, design, and produce metal parts.
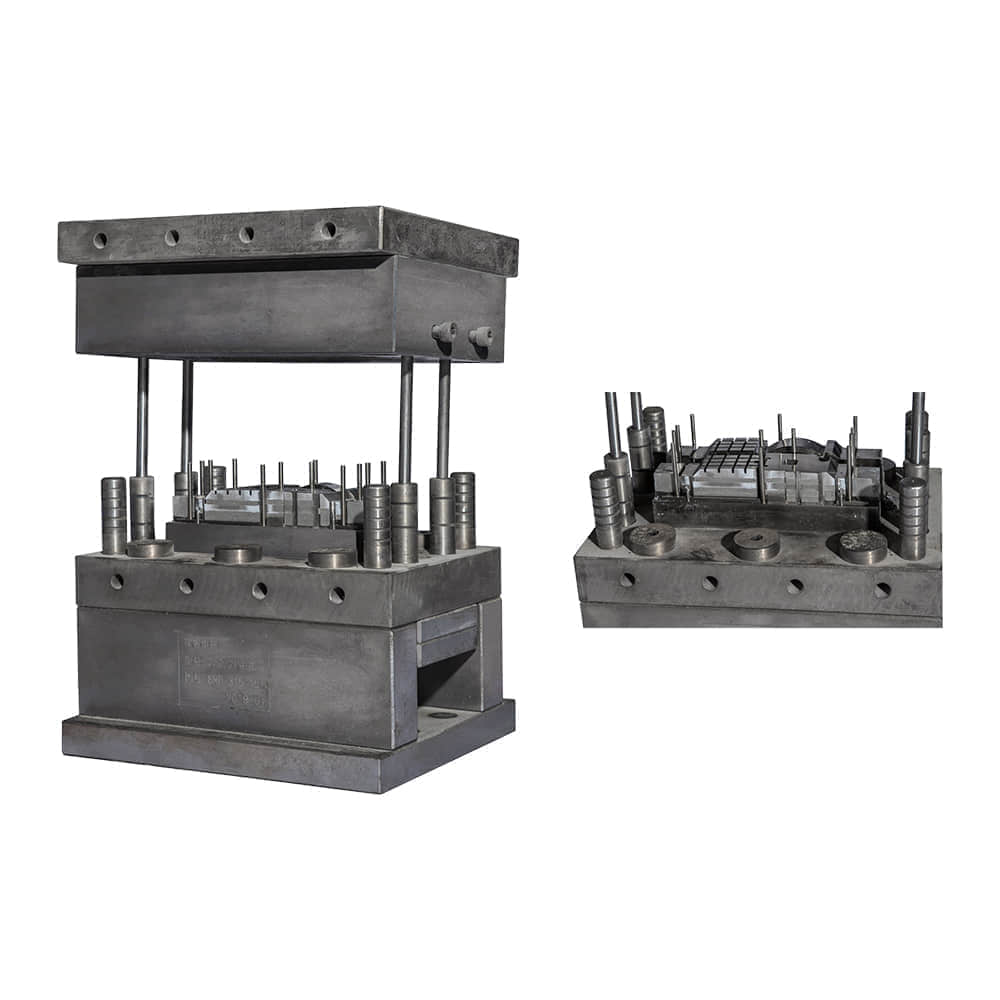